Conventional manufacturing methods such as soft lithography and hot embossing processes can be used to bioengineer microfluidic chips, albeit with limitations, including difficulty in preparing multilayered structures, cost- and labor-consuming fabrication processes as well as low productivity.
Materials scientists have introduced digital light processing as a cost-effective microfabrication approach to 3D print microfluidic chips, although the fabrication resolution of these microchannels are limited to a scale of sub-100 microns.
In a new report published in Microsystems and Nanoengineering, Zhuming Luo and a scientific team in biomedical engineering, and chemical engineering in China developed an innovative digital light processing method.
They proposed a modified mathematical model to predict UV irradiance for resin photopolymerization and guided the fabrication of microchannels with increased resolution. The advanced microfabricating method can facilitate major developments in precise and scalable microchannel formation as a significant next step for widespread applications in microfluidics-based strategies in biomedicine.
Microfluidic chips
The microfluidics chips offer a powerful tool to miniaturize applications in 3D cell culture for drug screening and testing applications and organ-on-a-chip assays. Conventional methods to develop microfluidic chips include soft lithography and hot capillary fabrication with a complicated engineering process, low productivity and high cost.
3D bioprinting has attracted increasing attention to innovatively design and manufacture customized structures at the microscale. Materials scientists have used digital light processing for layer-by-layer vat photopolymerization to microfabricate with resolutions up to tens of microns with rapid processing speed and ease of function.
In this work, Luo and colleagues developed a new digital light processing method for high-resolution and scale-up fabrication of microfluidic devices by dosing and zoning vat polymerization. The team fine-tuned the printing parameters and other parameters to precisely tailor the photopolymerization of neighboring resin layers and avoid channel blocking due to excessive UV exposure.
When compared to conventional methods, the process allowed the one-batch development of up to 16 microfluidic chips. The current method can facilitate major advances in precise and scalable microchannel development as a significant step forward of microfluidics-based devices in biomedicine.
Using a mathematical model to predict the characteristic parameters of resin
The team regulated the UV irradiation dosage by applying stepwise UV to polymerize the resin layer-by-layer by using a mathematical model. Upon UV irradiation for a specific exposure time, the scientists polymerized a specific depth of the resin solution. Then, using the mathematical model, they determined a comprehensive method to calculate the threshold of resin polymerization. The printing path incorporated in the work precisely divided the microchannel into the bottom layer, channel layer and roof layer.
Design rationale and experimental setup for microchannel development
Based on the outcomes, the researchers proposed a modified version of digital light process (DLP) printing strategy to fabricate substantially small microchannels through dosing- and zoning-regulated vat photopolymerization (abbreviated DZC-VPP). This process divided the microchannels into several layers. The capacity to regulate the zones for each projection step allowed the precise regulation of local resin polymerization, the scientists successfully printed the channels with significantly higher resolution.
The team studied the printing quality of the new approach by comparing it with the conventional method. While the conventional method led to poor fidelity of channels due to the accumulation of excessive UV exposure, the new method contrastingly offered microchannels with significantly improved printing fidelity to allow the development of smoother internal surfaces within the microchannels with significant impact on liquid manipulation. The DZC-VPP method is additionally highly scalable and cost-effective.
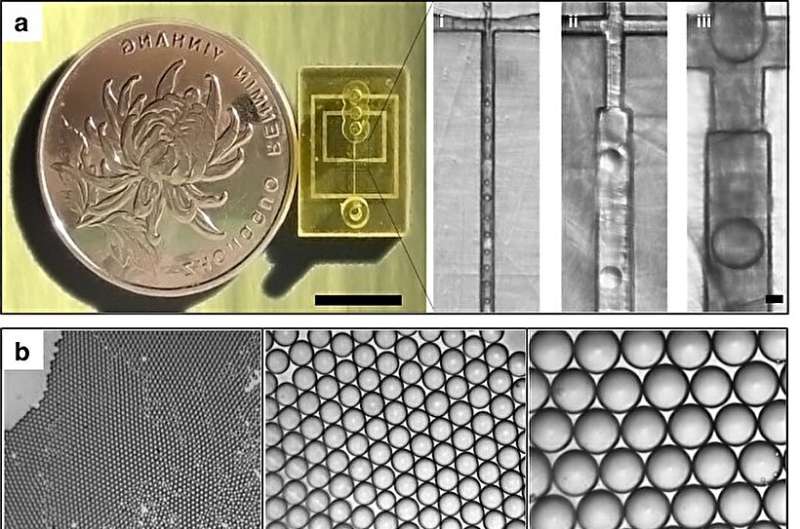
Mechanical stability of the developed materials
Luo and colleagues next investigated the mechanical stability of the microfluidic devices engineered with the new DZC-VPP method and again compared it with the conventional process. While mechanical stability is crucial for the microfluidic chips to tolerate high liquid pressure, the two materials demonstrated similar stress-strain curves.
The DZC-VPP fabricated chip showed significantly higher fracture stress and strain when compared to the DLP chip, indicating that the new strategy improved both printing resolution and mechanical stability of the engineered microfluidic chips.
Generating droplets and microgels and encapsulating cells with microgels
To accomplish microfluidic generation of droplets, the scientists used pure water as the aqueous phase and an oil-glycol emulsion to create monodisperse aqueous droplets. The team encapsulated the cells with microgels in the fabricated chips by using the alginate system. To prevent cytotoxicity in the instrument, the researchers tested the biocompatibility of the chips using cell-laden microgels.
Both HeLa cells and rat mesenchymal cells used in the study retained cell viability after encapsulation to gradually proliferate into cell clusters, indicating the biofriendly nature of the DZC-VPP engineered microfluidic device. The method is also best suited for other cell-related applications including the development of organ-on-a-chip instruments.
When compared to the conventional digital light printing process, the newer DC-VPP method can regulate the UV penetration depth for resin photopolymerization. The outcomes highlighted the reliability of the new process for high-resolution printing to fabricate 3D printed microfluidic chips.
Outlook
In this way, Zhuming Luo and the research team developed a new dosing and zoning regulated vat photopolymerization (abbreviated DZC-VPP) method to 3D print microchannels with improved resolution and mechanical stability. The team accomplished this by proposing a mathematical model to predict the accumulated UV irradiance for resin polymerization as a guide to design and print the microchannels.
Using the approach, the team printed a microchannel with conventional soft lithography or hot embossing to generate high throughput monodisperse droplets and cell-laden microgels. This highly efficient method of microfabrication represents a key step for high resolution, scaled up fabrication of microfluidic devices for widespread applications.
Subscribe to AM Chronicle Newsletter to stay connected: https://bit.ly/3fBZ1mP
Follow us on LinkedIn: https://bit.ly/3IjhrFq
Visit for more interesting content on additive manufacturing: https://amchronicle.com