Prof. Dr Leonid Ionov and his team at the University of Bayreuth have developed a new type of 3D printing technology that combines hydrogels and fibres. The innovative process, combined in one device for the first time, enables the production of constructs with fibrous structures and uniaxial cell alignment. The research results, published in the journal “Advanced Healthcare Materials”, harbour potential for the artificial production of biological tissue.
Biofabrication, a specialised field of medical technology that deals with the production of biologically relevant structures, aims to replicate the complex architecture of human tissues and organs. One promising approach to counteracting the global shortage of donor organs is the use of 3D (bio) printing, an advanced biofabrication technique. This technology was integrated, in a single, with a fiber spinning technology called touch-spinning. This approach has been under development at the University of Bayreuth since 2018 and enables the production of tissue-like structures. An innovative device for this has now been invented and patented in Bayreuth and could represent a significant advance in the production of living tissue. In addition, great progress has been made in the area of efficient production of fibres and composites.
In the latest study by Prof Dr Leonid Ionov, Professor of Biofabrication, and his team at the University of Bayreuth, various types of hydrogels were extensively tested for the 3D printing of tissues. A hydrogel is a water-retaining and at the same time water-insoluble polymer. In addition, the cell containing-hydrogels, also known as bioink, are combined with fibres to create a composite material. This is achieved by using 3D (bio) printing with an integrated touch-spinning process.
Touch spinning is a scalable process for producing of fibres from a polymer solution or melt. The Bayreuth scientists have now combined 3D (bio) printing technology with touch-spinning technology in a single device for the first time.
“The insights gained in this study are of great importance for the production of tissues and in particular tissues with fibrous structures and uniaxial alignment of cells such as connective and muscle tissue,” explains Prof. Dr Leonid Ionov.
In an article recently published in the journal “Advanced Healthcare Materials”, the Bayreuth researchers Prof. Dr. Dr. Elisabetta Ada Cavalcanti-Adam, Chair of Cellular Biomechanics, Prof. Dr. Leonid Ionov, Professor of Biofabrication, Waseem Kitana, PhD student at the Chair of Biofabrication, and their colleague Dr. Victoria Levario-Diaz from the Max Planck Institute for Medical Research, report on a novel approach for the production of multilayer bioink fibre composites.
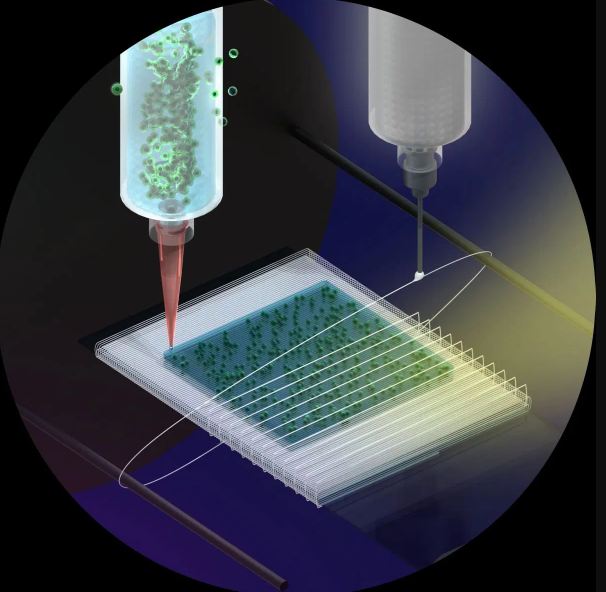
The Bayreuth scientists used various hydrogels in the experiments and compared their properties. Hydrogels have been widely used as scaffold materials in the fields of tissue engineering and biofabrication for decades. Tissue engineering is the umbrella term for the artificial production of biological tissues.
The combination of a hydrogel system with a fibre system reduces the processing requirements for hydrogels, such as cross-linking to improve their mechanical properties, as the mechanical properties of these composite materials are covered by the fibre system. In addition, the requirement for a low degree of cross-linking is advantageous for subsequent tissue formation. “The hydrogel provides the cells with an aqueous environment that promotes the good functioning of the cells, while the fibres should control the orientation of the cells along the main direction of the fibre,” says Prof. Ionov.
Building on the invention of the new and already patented device that combines these two techniques, the Bayreuth scientists have founded the start-up company “biovature GmbH” under the leadership of PD Dr habil. Alla Synytska (co-founder and CEO).
The German Research Foundation (DFG) research cluster SFB/TRR 225 provided financial support for the research.
Subscribe to AM Chronicle Newsletter to stay connected: https://bit.ly/3fBZ1mP
Follow us on LinkedIn: https://bit.ly/3IjhrFq
Visit for more interesting content on additive manufacturing: https://amchronicle.com