On the sidelines of Advanced Manufacturing Technology Conference earlier this month, I had the opportunity to speak to Kartik Rao, Head of AM Commercial and Strategy, Oerlikon AM about his journey in the Additive Manufacturing industry, the challenges which need to be addressed by the industry and the role Oerlikon AM is playing in advancing Additive Manufacturing.
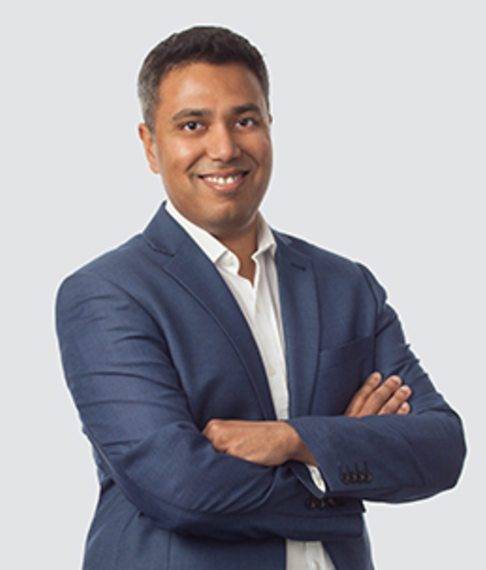
Kartik is head of the AM business unit’s commercial strategy and leader of its business excellence team. In this newly created role, Kartik combines the knowledge and experience he brings from his previous roles as Head of AM Marketing and Head of the AM Materials business line. He enjoys working in an entrepreneurial group within a larger established company, and particularly likes the challenge of identifying customer groups who can benefit from additive manufacturing and pairing them with the appropriate experts and technology at Oerlikon AM. Before joining Oerlikon AM in 2016, Kartik worked in business and product development at a VC-backed powder technology company in the UK. He was also responsible for technology licenses and helping raise capital for venture capitalist and strategic investors. Kartik holds a master’s degree in aerospace materials engineering and a Ph.D. in titanium production from Imperial College in London.
You have been part of the Additive Manufacturing industry for over 12 years. How has your journey been and how has the Metal Additive Manufacturing material space evolved in this span of time ?Â
My interaction with the Additive Manufacturing industry began on the materials side. I am a powder metallurgist by background and the journey began with working towards manufacturing spherical powder, which could be used in a Metal AM printer. When I started working with metal powders, the printer technology that we had access to were small research grade printers. At that time it was not very clear how the Additive Manufacturing market was going to grow. However over the years, the technology has evolved towards larger bed platforms, more lasers with a drive towards productivity. Additive Manufacturing is no more an interesting technology, but is making its way towards becoming a production grade manufacturing technology.
My role in the Additive Manufacturing industry has changed as well from looking after the metal powder business to the service side of the business. Now in a general management role, I am taking care of the service facility in North Carolina, US which as 15+ Printers servicing the aerospace and defense industries in the US. What I have seen on the service side that the technology is maturing however it is not yet matured completely. We are still in a position where it is highly capital-intensive industry and to achieve the next level of breakthroughs we need certainty of demand.
Additive Manufacturing over the past 12 years has evolved from being a materials science R & D Program, a business which is focused on selling powders and printers to a point now where the industry is much more focused on serializing production of parts.
What are the key challenges or concerns which need to be addressed for further adoption of Additive Manufacturing in production or serial manufacturing applications?
I will split the key challenges into three main segments based on my understanding and observations
1) Market – One of the greatest commercial challenges we have had in the industry is the certainty of the demand from the end user market. In the last 5 years the focus was primarily on the commercial aviation industry due to the presence of large number of narrow bodied airlines which translate into larger part counts. However due to the pandemic the entire commercial aviation industry is on pause and that has been one of the industry, which was able to provide the certainty of demand forecast. The question now is from the remaining participants from the space, defence or power generation sector is to get a commercial visibility. This is very essential as there is large amount of investment still needed to grow this technology. The end user industry and the supply network need to work together towards identifying the long-term demand.
2) Industrialisation – This has been one of the key topics of debate at the earlier MTC’s as well about challenges for industrialization. These can again be split into:
a) Repeatability of production – Huge steps have been taken by various stakeholders including Oerlikon primarily drive by quality functions to make sure repeatable processes are able to to produce uniform parts.
b) Reliability of production – This is dependent on the quality of hardware and the service thereafter. One of the things I have realized with running the service business is that the machine manufacturers need to step up in terms of service. Service levels are not quite where they need to be, to run the machines over and over again. It is very important to maximize the laser ON time. If machines are down for long durations, this is hugely damaging in terms of cost for the service provider and loss of credibility (The end users are benchmarking additive manufacturing against conventional technology, extended down times damage credibility of the process on the whole)
3) Cost
Each year the production costs are coming down, and we need to ensure that this curve continuous on the downward trajectory. As the production costs come down new markets will start opening up with the potential of mass adoption, example – Automotive Industry. It is very important for all stakeholders to work together to bring down the costs of the technology.
What role is Oerlikon AM playing in making the Metal Additive Manufacturing process more reliable, sustainable, cost-effective and efficient ?Â
Advanced Manufacturing Technical Conference
Co-creating AMTC is definitely a key role Oerlikon AM is playing in creating a forum for the AM ecosystem to share knowledge, share best practices and try and break those competitive tensions which generally hold the market back. The recently concluded AMTC in Aachen was focused on building momentum for growth. Coming out of the pandemic, there is going to be an element of bounce back. However our aim is to carry on the momentum beyond just recovering from the pandemic by building the further roadmap for growth.
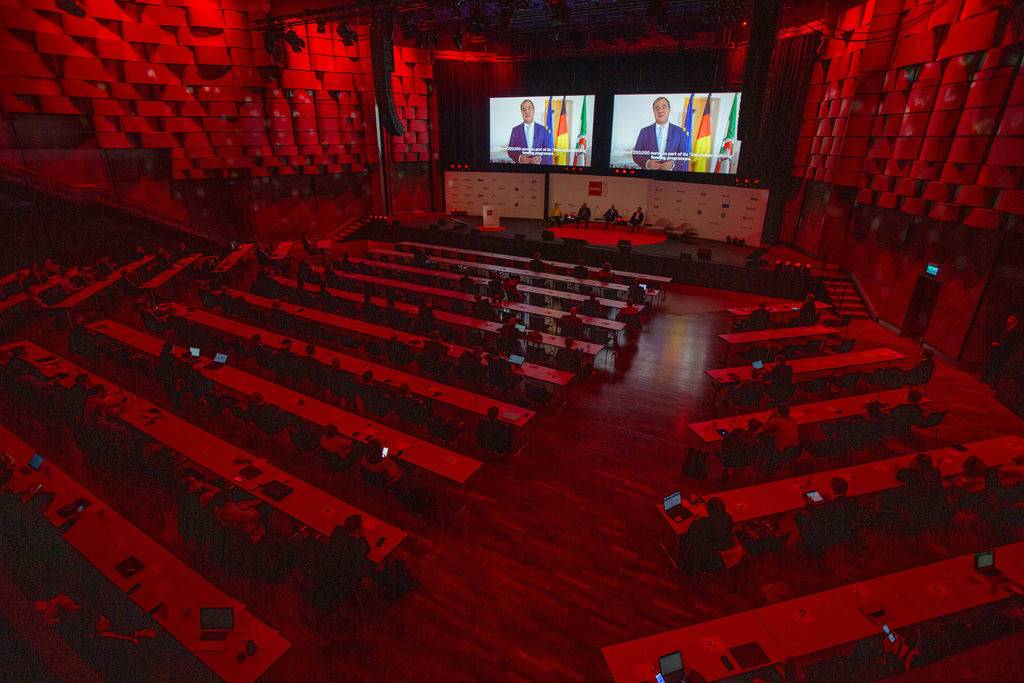
Integrating the Value Chain
Linking several discrete aspects of the value chains as a I see is a strong role player by Oerlikon AM. We have been in the business of manufacturing metal powders for close to 50 years, and we also produce gas atomized spherical metal AM powders which are suitable for Additive Manufacturing. We are also one of the very few players out there who have the knowledge from powder manufacturing all the way to post-processing technologies and surface technology, along with strong linkages with the machine manufactures.
Optimising processes with Global Insights
Operating on global basis with a service business in China, USA and Europe, we are able to share knowhow between those sites and optimize the process based on that feedback. We are also able to bring those market insights back to our vendors – software manufacturers, machine manufacturers or powder manufacturers for them to improve their solutions in turn adding to the success of Oerlikon.
Sustainability
Oerlikon released their first sustainability report recently. Climate change has become more and more of a concern and we see a lot of customers focusing on this aspect, I feel Additive Manufacturing is a perfect fit with its inherent advantages in the sustainability journey. We are able to consolidate parts, which reduces weight, we are able to add coatings which can reduce weight as well leading to cost savings and reduction in carbon emissions. If you look at the Oerlikon portfolio of coatings, we are roughly able to save close to 25 MT of CO2 emissions. Oerlikon’s investment in Additive is also complimentary to our sustainability drive as well
Any success stories for Oerlikon AM in specific sectors you would like to speak about ?
I would like to mention a couple of success cases at the two ends of the application spectrum. One is with a space company in the USA and the other with a cycle manufacturer in Germany.
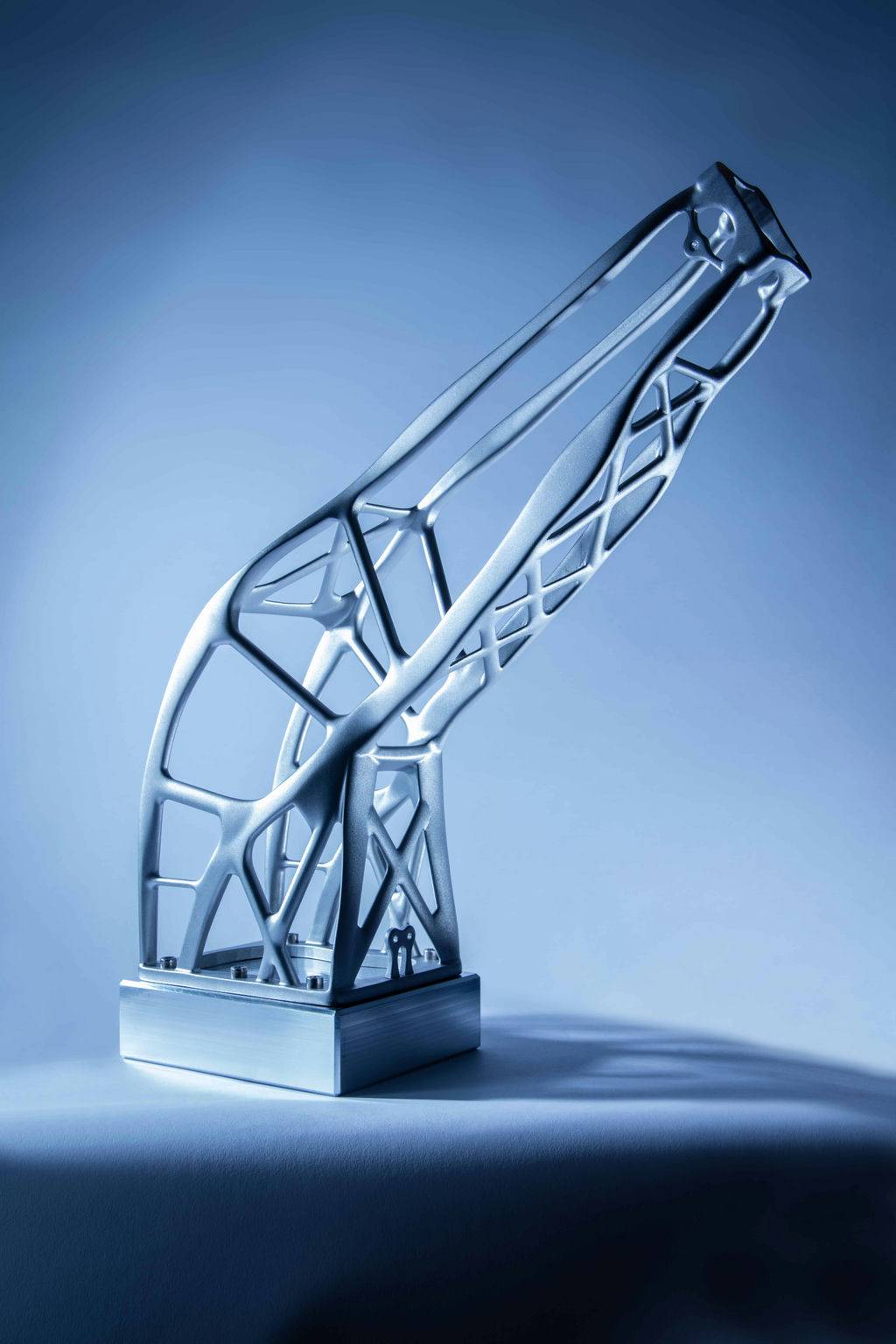
United Launch Alliance
United Launch Alliance is one of our flagship customers. They are an American spacecraft launch service provider that manufactures and operates a number of rocket vehicles that are capable of launching spacecraft into orbits around Earth and to other bodies in the Solar System. We helped them begin their Additive Manufacturing journey. Saving weight for space applications is hypercritical, every kg that you reduce, saves thousands of dollars of launch costs. We partnered with them so that they were able to design optimal components using DfAM  and Oerlikon as a sole source supplier manufactured these components. The process include helping them design parts which have best functionality, consolidate parts if needed be and then taking it up one step further by manufacturing those parts for them.
Urwahn
With a rising trends towards people taking up biking, Oerlikon AM is working with a cycle manufacturer in Germany – Urwahn to rethink cycle frames. Oerlikon AM is working with them to build light and functional frames.
Great to have this interview with you on the sidelines of AMTC and it is a great line up again as usual, What would you say are the key objectives of AMTC and how is it contributing to push the adoption of AM?
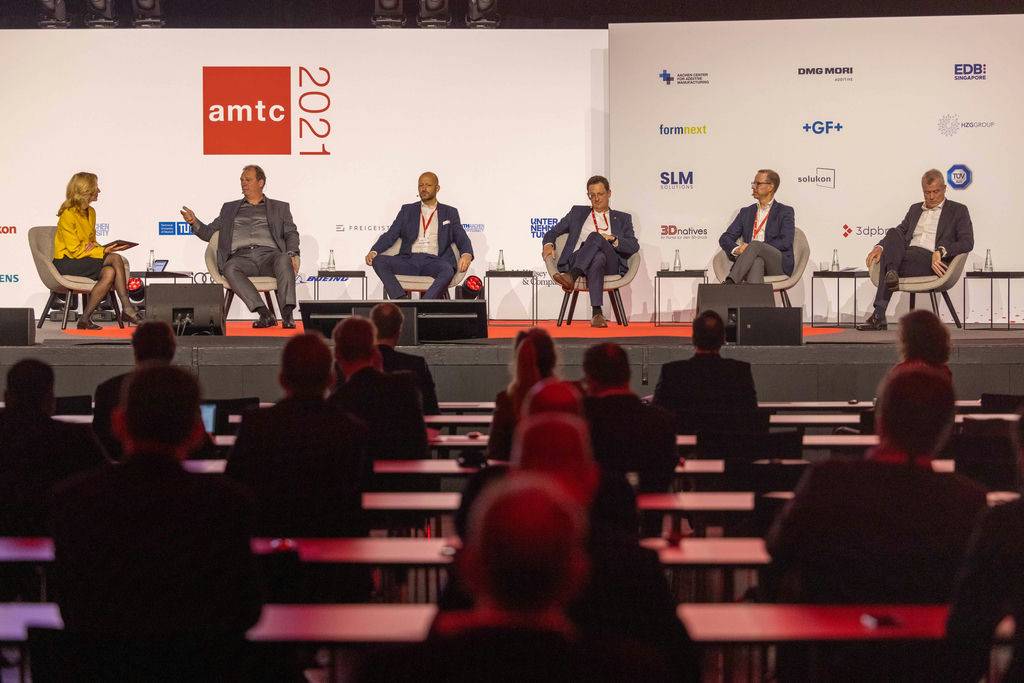
This conference followed three Munich Technology Conferences and the aim of this conference was to use the post-pandemic bounce back to fuel further growth. This platform provides the perfect forum for the entire ecosystem to come together to exchange their knowledge, best practice examples, network and find business opportunities together.
For a new technology to really grow in the earlier years the ecosystem has to come together and collaborate. The regulations, standards need to be developed by all stakeholders at an industry level so that it gives the customers confidence that his technology is reliable, scalable and cost-effective. This platform provides this opportunity to the industry, academia and policy makers to come together and collaborate.