The Technology Innovation Institute (TII) is a leading global research center dedicated to pushing the frontiers of knowledge. One of the areas of research at TII is additive manufacturing, also known as 3D printing. TII has several additive manufacturing initiatives underway, aimed at developing new technologies and applications for this rapidly growing field.
TII’s additive manufacturing initiatives are making a significant impact on the global technology landscape. The centre’s research is helping to develop new additive manufacturing processes and materials that are more efficient, cost-effective, and versatile. The innovation lab is helping to accelerate the development of new additive manufacturing applications in a variety of industries. And the entrepreneurship programme is helping to create new additive manufacturing businesses that are driving economic growth and job creation.
TII’s work in additive manufacturing is helping to make the technology more accessible and affordable, and it is driving the development of new and innovative applications. TII is a leading force in the global additive manufacturing community, and its work is helping to shape the future of manufacturing.
One of TII’s additive manufacturing initiatives is the development of new materials for 3D printing. TII researchers are working on developing new materials that are stronger, lighter, and more durable than traditional 3D printing materials. They are also working on developing materials that have specific properties, such as high conductivity or flame resistance.
Research Works on Additive Manufacturing at TII
The paper “Incorporating the Roles of Feature Size and Build Orientation in Laser Powder Bed Fusion Process Simulation for the Prediction of Mechanical Properties” by TII’s team investigates the effects of feature size and build orientation on the mechanical properties of parts fabricated by laser powder bed fusion (L-PBF). The authors developed a finite element model to simulate the L-PBF process and used it to study the effects of different feature sizes and build orientations on the temperature distribution, residual stress, and tensile properties of the parts. The results showed that feature size and build orientation have significant effects on the mechanical properties of L-PBF parts. Smaller feature sizes and build orientations that favor the fusion of powder particles lead to improved mechanical properties. The paper provides valuable insights into the factors that affect the mechanical properties of L-PBF parts and can be used to guide the design and optimization of L-PBF processes.
In other study conducted by TII’s team, they investigates the feasibility of conducting in-situ heat treatments during PBF-LB of AlSi10Mg parts. The authors found that it is possible to in-situ direct age the material by increasing the printing time from 5 hours to 11 hours while printing at 220°C. This resulted in an increase in hardness and strength of the parts. The authors also found that it is possible to in-situ solution heat treat the material by using build plate temperatures between 450°C and 500°C for 11 hours. However, this resulted in a reduction in ductility of the parts. The research paper investigates the feasibility of conducting in-situ heat treatments during PBF-LB of AlSi10Mg parts. The authors found that it is possible to in-situ direct age the material by increasing the printing time from 5 hours to 11 hours while printing at 220°C. This resulted in an increase in hardness and strength of the parts. The authors also found that it is possible to in-situ solution heat treat the material by using build plate temperatures between 450°C and 500°C for 11 hours. However, this resulted in a reduction in ductility of the parts.
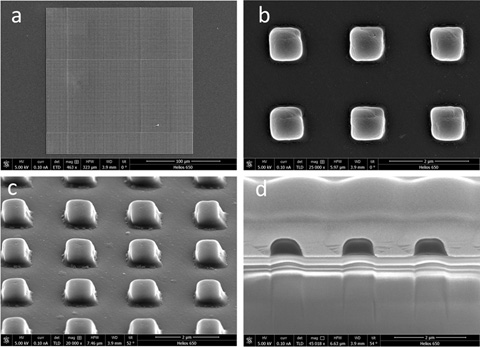
In other study conducted by the Advance materials research center at TII, researchers investigated the use of 3D-printed microcubes as drug delivery vehicles for catalase. 3D-printed microcubes are small (800 nm in length and 600 nm in height) and uniform in size, making them well-suited for targeting macrophages passively. The authors concluded that 3D-printed microcubes are a promising new drug delivery system for catalase and other therapeutic proteins.
TII’s additive manufacturing initiatives are making a significant impact on the field of 3D printing. TII’s research is helping to develop new materials, processes, and applications for 3D printing, which is making this technology more accessible and useful to businesses and industries around the world.
References:
Phutela, C.; Bosio, F.; Alhammadi, A.; Alshehhi, N.; Kindleyside, L.; Aboulkhair, N.T. Incorporating the Roles of Feature Size and Build Orientation in the Process-Structure-Property Relationship for Additively Manufactured Parts. Metals 2023, 13, 151. https://doi.org/10.3390/met13010151
Bosio, F., Phutela, C., Ghisi, N., Alhammadi, A., & Aboulkhair, N. T. (2023). Tuning the microstructure and mechanical properties of AlSi10Mg alloy via in-situ heat-treatments in laser powder bed fusion. Materials Science and Engineering: A, 145268.
Lee S, Lee DW, Rajput N, Levato T, Shanti A, Kim TY. 3D-Printed Microcubes for Catalase Drug Delivery. ACS Omega. 2023 Jul 20;8(30):26775-26781. doi: 10.1021/acsomega.3c00789. PMID: 37546651; PMCID: PMC10398707.
Subscribe to AM Chronicle Newsletter to stay connected:Â Â https://bit.ly/3fBZ1mPÂ
Follow us on LinkedIn:Â https://bit.ly/3IjhrFqÂ
Visit for more interesting content on additive manufacturing:Â https://amchronicle.com