Credit: Article adapted from report written by Arjun Ramesh.
Manufacturing is the process of converting raw materials into finished product that confirms to end user requirements through a series of value addition process. Basically, manufacturing processes can be classified into four: Metal casting, Metal cutting, Metal joining and Metal forming. Be it any process, the production of any component involves the use of tooling. Additive manufacturing is the process of building a component from scratch to whole by deposition in form of layers of material one over another according to a predefined model. Ever since its birth AM is seen as a technology that is suited for hobbyists and prototyping. The consumer bubble that has surrounded AM has burst and it has made huge strides in mid volume manufacturing. Â This has happened due to improve in materials and printer parameters. Companies such as GE has 3D printed about 10000 brackets for installation in aircraft. This has helped GE to reduce time of manufacturing and reduce material wastage.
The tooling industry globally can be considered as fifth largest horizontal that sustains every vertical in the manufacturing sector. Tooling and Manufacturing are interdependent. The output of a manufacturing process depends on the quality and efficiency of tooling. Products that are countless in number put together with help of jigs and fixtures that are generally manufactured by moulding or casting. CNC machining is the most commonly applied method for manufacturing tooling. But CNC is a subtractive process and limitations exist. To mention a few
- Time
- Cost
- Material usage
- Limited to simple shapes
Tooling is a mid volume manufacturing entity. Tooling is a general term used to refer for components used in various manufacturing processes—including injection moulding, extrusion, stamping, casting, cutting, and assembly. Even the production of a single tooling can be complex because it is made up of more than one part. The process of tool-making eats up a lot of time and money. The process can be tiresome as a result of complex geometry and part requirements. A tooling can also be an assembly of multiple parts. If a tool breaks or the design changes, the entire production schedule can be delayed—or stopped completely—until a replacement part is available. It’s common for tooling components—such as mould cavity inserts, extrusion dies, end-effectors, stamps, and cutting inserts—to be produced in low volume, involve complex geometries. Each of these factors can have a significant impact on overall production cost and lead time.  Moulds, patterns, jigs, and features are generally produced in low volumes and feature complex shapes. This is where AM comes into play. The digital fabrication method is not weighed down by the material option and the profiles to be made. AM has been embraced by many industries such as automotive, aerospace, and healthcare and medical, among others, to integrate AM in their supply chain, including for tooling manufacture. Potential candidates that can take leverage of the benefits of additive manufacturing in tooling are:
- Moulding (blow moulding, soluble cores for composite materials, injection, etc)
- Casting (Investment casting, squeeze, sand, spin, etc)
- Forming (Hydroforming, extursion, puching, blanking)
- Machining, assembling and inspection (Jigs and fixtures)
- Robotics end effectors (End of arm tooling-grippers)
The application of tooling can take different forms. The type of usage may be customized, mid or mass manufacturing. The nature of usage is largely dependent on the industry. There have been lots of success stories and any AM technology adopter can look into as a motivation.
Look at successful implementation of AM in tooling:
- General Motors saved $300,000 by adopting 3D printed tooling. Traditionally, assembly tooling would be machined from metal, costing hundreds or thousands of dollars to produce. The machining process is subtractive manufacturing that leads to the material wastage. If the part gets broken, or needs improvement, it would result in further expenses to the producer. Jigs, tooling and fixtures can be manufactured at a minimal cost with 3D printing or additive manufacturing. General Motors has 3D printed a prototype tool that is used to align engine and transmission vehicle identification numbers and this 3D printing cost less than $3. If outsourced, the part would have cost the plant $3,000. New devices can be produced quickly on site, cutting down downtime or inefficiency due to a broken or faulty tool.
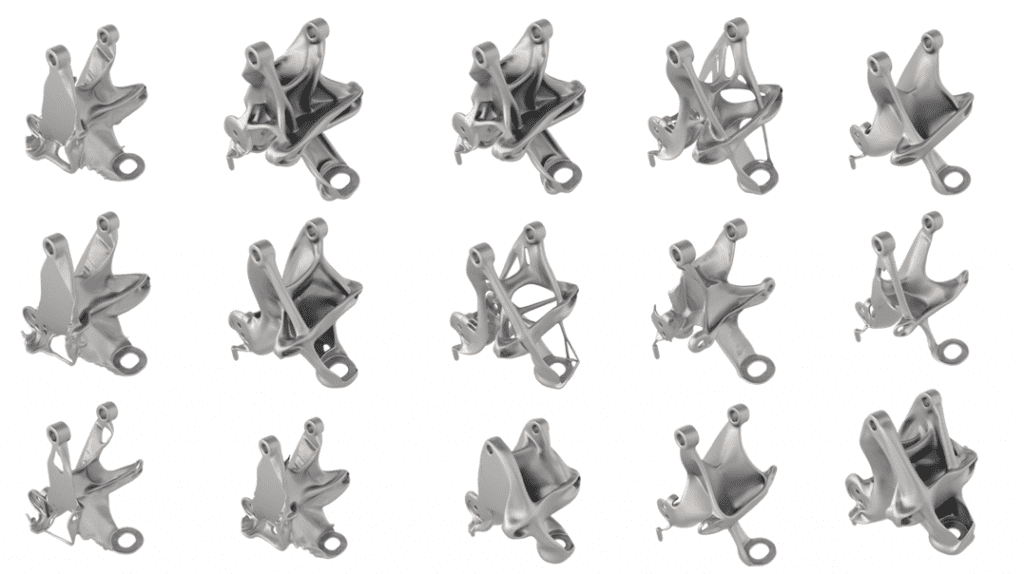
- Stratasys and Mclaren are involved in a four-year partnership, where Stratasys’ FDM and PolyJet based 3D printing solutions and materials will be used for production tooling and composite tooling.
- Mapal, a leading tool manufacturer is using AM for producing QTD drill inserts, allowing for the inclusion of a spiral cooling channel, which boosts the performance of the drill and offers long service life for the drills.
- GKN serves more than 90 percent of aircraft and engine manufacturers with aero structures, associated technologies and engine systems. The company has invested in Stratasys to reduce lead time for production tools to create complex profiles. For the manufacturing of tooling on the F900 printer, GKN is using Stratasys material ULTEM 1010 resin.
- In the medicine field, tools play different roles: in surgical procedures, guides are used to direct the surgeon to the precise location. The surgical guides need to be easy and quick to produce, accurate and customizable to the specific patient. Consensus Orthopedics is using Materialise Knee Guide System that facilitates surgeons to plan and conduct surgery that are specifically customized.
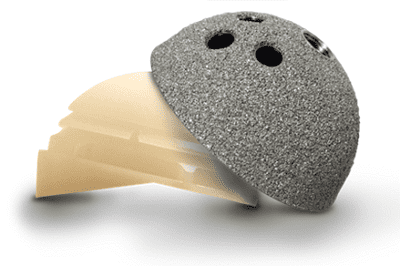
The potential advantages Â
1) Lead time is shortened
Sometimes companies are redundant towards changes in tool design, as it will lead to investment in development of new tooling. Additive manufacturing reduces the time span of product development. With help of new generative AM softwares, it is possible to obtain the most suitable design from all permutations. With Additive manufacturing it is possible to enable quick design changes. It enables companies for frequent replacement and improvement. In-house tool development helps companies to overcome the supply chain uncertainties.
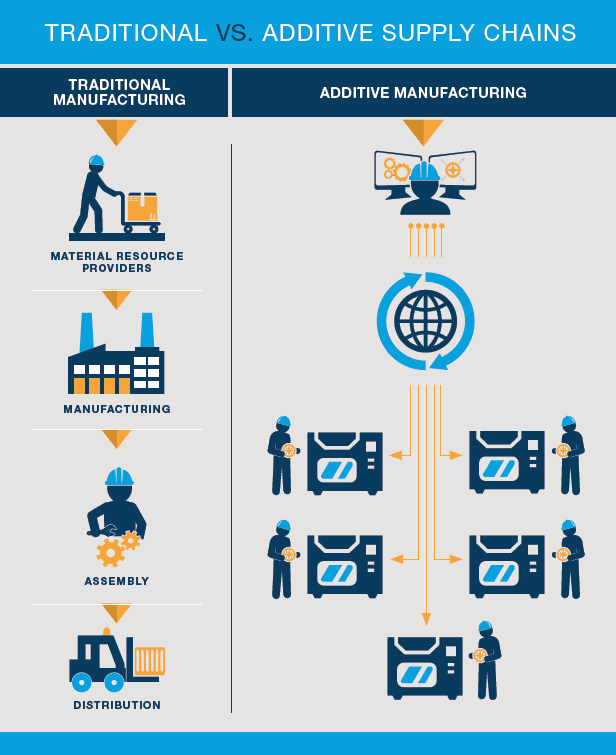
2) Costs can be reduced
Metal additive manufacturing of tooling is costlier on comparison with conventional manufacturing processes. The area where cost reduction can be achieved is in plastic. For batch of small products and specific geometries metal AM is beneficial but not on a large scale. In instances where inventory holding cost and production time increase exponentially AM can be used as the go to technology which can manufacture the tooling with at most precision in a short span of time.
3) Improved tool design facilitates more functional final products
An additive manufactured tooling has specific metallurgy. It generally posses refined microstructure that gives rise to fully dense parts. A tooling that requires sub assemblies can create tolerance issues but a tooling made by AM is a single part. AM enables free-form channel geometry to ensure a conformal cooling, more optimal and homogeneous, which eventually leads to higher-quality parts and lower scrap rates.
4) Customized tools for customized end products
This is very advantageous in healthcare industry where personalized medical devices and surgical guides have to manufactured within a short period of time
5) Optimizing tooling improves ergonomics and bottom line performance
Conclusion:
Additive Manufacturing for Tooling applications can be a valuable and good investment for companies. However, this can happen only when the nature of Tooling needs is fairly assessed. Suitable opportunities are low-volume production cases in which the ability to create complex geometries can improve tooling performance.
As the systems scale up in technology, size and speed, it opens up more applications for AM in Tooling. It will further impact supply chain and final products by pushing innovation forward and boosting traditional manufacturing methods.
Credit: Article adapted from report written by Arjun Ramesh.