When a vessel is in need of a spare parts, it is conventionally shipped from a central warehouse to the ship’s next port destination. However, with vessels that are decades old at best, delivery and production is not always as straightforward as they require spare parts that are either no longer manufactured or require a long lead time. This process often becomes costly and inefficient.
Over the last decade however, we have seen Additive Manufacturing (AM), or 3D printing, make its way into the maritime sector – redefining the maritime and offshore spare parts supply chain and the way spare parts are made with its ability to manufacture rapidly and with flexibility. Its varied modalities have been largely proven in other sectors with improved mechanical and economic performance.
According to Jabil’s research (2021), there is steady progression of industry adopters where AM accounts for at least 10% of spare parts production. The research also indicates customers placing an emphasis on design capabilities, ability to scale and companies’ expertise in AM when selecting an outsourced partner for printing.
The partnership between thyssenkrupp and Wilhelmsen addresses these points specifically through their AM Fulfilment Platform. With thyssenkrupp’s expertise in AM and Wilhelmsen’s long standing supply chain know-how and maritime distribution network, the platform enables a more cost effective, on-demand manufacturing solution, providing just-in-time deliveries.
Vessels now have the option to print their needed spare parts upon demand to its required measurement, using the most appropriate material. With the platform’s many global partners, it allows spare parts to be fabricated at locations closest to the vessel within a short lead time. There is no doubt this business model is effective in strengthening on-demand AM capabilities across the entire spare parts supply chain while increasing cost performance.
The partnership is unique in that it relies on a decentralised manufacturing approach yet provides spare parts that meet industry standards and expectations customers have come to uphold from such established global companies. A Quality Assurance Framework endorsed by DNV governs the workflow and ensures that quality and fitness-for-purpose is considered at every step of the fabrication process.
Cooperating with several Original Equipment Manufacturers (OEMs), the venture empowers OEMs to reduce their supply chain costs and improve customer experience through increased serviceability and shorter delivery times in key locations. The thyssenkrupp and Wilhelmsen partnership has since successfully printed and delivered quality parts for customers across the world through its fulfilment platform.
HVAC Condenser Fan Blade
The part shown is a HVAC Condenser Fan Blade, which is used to extract heated air from the condenser coil. By printing the part using fused deposition modelling, production lead time was shortened to 3 days.
The fan was fabricated using high temperature carbon fibre nylon instead of aluminium to eliminate corrosion issues. The part is not only 30% lighter but has maintained equal strength and thermal stability. This translates to quieter operation, fewer maintenance requirements and lower running costs.
The thyssenkrupp and Wilhelmsen 3D printing venture has also expanded their technology capabilities to encompass metal binder jetting deposition. The spare part was done in relation to the Singapore Joint Industry Programme, together with DNV, Ivaldi, tytus3D, and a number of OEMs and end users.
The Worm Gear is part of a specialised high pressure-generating system. This obsolete part faces long lead times or, more often than not, non-availability due to the complex gear tooth profile.
Employing the binder jetting process, the Worm Gear was enhanced both in functionality and durability through passivation for extra corrosion resistance and the usage of a comparable material. With the customisable function, in terms of materials or dimensions, it allows for replacement of a damaged component instead of the whole system.
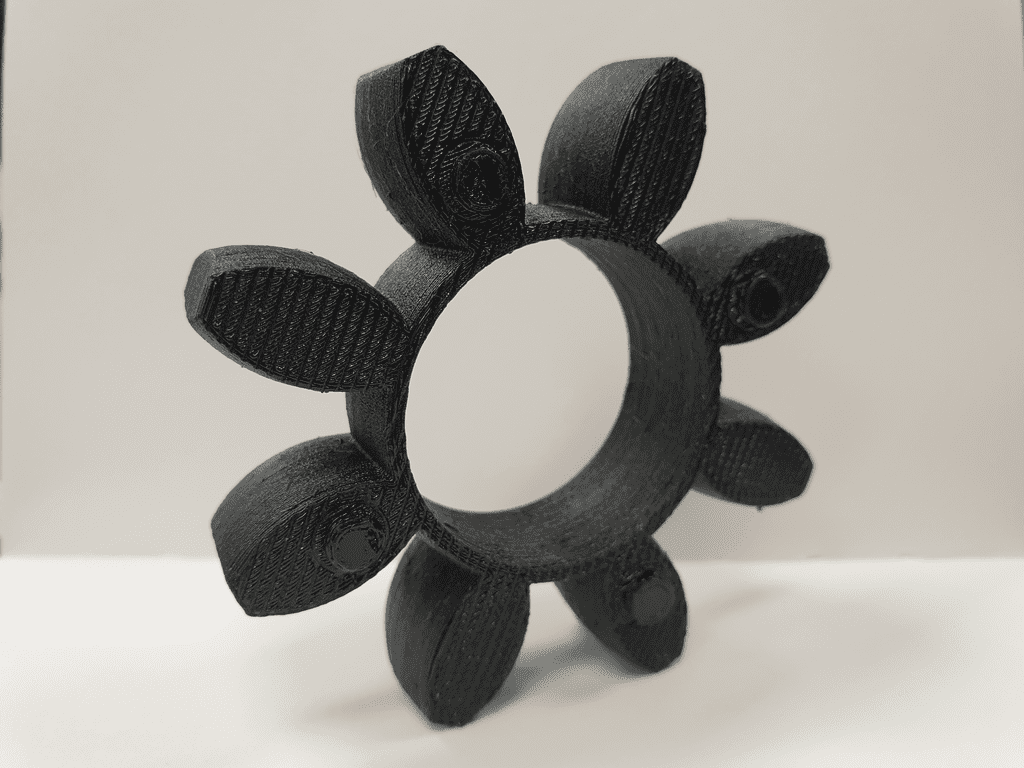
Spider Coupling
“Yinson recently received a 3D printed spider coupling for the Hydroclone Process Skid LP Pump. I would like to appreciate the quality of the material and accuracy of the workmanship provided by thyssenkrupp and Wilhelmsen. The item was also fabricated and delivered in a relatively short time” said Yinson – Maintenance Supervisor FPSO Helang
Manufacturing spare parts using AM technologies will greatly reduce both lead time and costs with greater flexibility as well as improve performance and increase service life. It can address part obsolescence, while shifting distributed supply chain and storage to a digital warehousing solution with local print-on-demand for replacement of spare parts.
With this one-stop digital manufacturing platform, thyssenkrupp and Wilhelmsen are bringing together a global footprint of partners, consisting of OEMs, end users, 3D Printing manufacturing partners and classification societies. The vast network will strengthen the feasibility for commercial adoption of AM, reshaping the maritime and offshore spare parts supply chain.