The growth of additive manufacturing (AM) has been remarkable in the last few decades. This is due to advances in market-driven technologies, increased personalization, new and improved  materials, customization, shorter product development cycles, and emergence of new business models. New AM techniques have been implemented in industries such as aerospace, biomedical, transportation, etc. with processes such as selective laser melting (SLM), fused deposition modelling (FDM), binder jetting, selective laser sintering (SLS), and other advanced processes. Also, thanks to increased precision in AM machines, a variety of materials can be manufactured with enhanced mechanical properties, with designs that are impossible to manufacture with conventional manufacturing techniques. AM thus aims to integrate the advantages of engineering design and prototypes into a final functional product.  Â
Vast opportunities have begun to open up with AM given its benefits of freedom of design, topology optimization, opportunity to experiment with different materials or combination of materials, colors, strength, and surface finish for finished products. Despite several advantages offered by AM, manufacturing constraints such as small holes, thin walls, overhang structures, and enclosed voids prevent removal of unmelted material or support structure. Besides, anisotropy and thermal distortion, residual stress, and internal cracks in super alloys are inherent process limitations which could compromise the final product outcome. Hence, it is paramount for design engineers to be exposed to both the capabilities and the process limitations while designing for AM, or Design for Additive Manufacturing (DfAM).
Freedom of design offers several opportunities to modify the original design or, in most cases, arrive at a new design and address the challenges in conventional manufacturing. DfAM approaches such as introduction of cellular or lattice structures, consolidation, part complexity, design for performance enhancement, light weight, etc. are often used to address these challenges. One of the approaches that has gained significant importance is cellular or lattice structures, due to its ability to selectively dispense material in specific regions of the part to improve strength and mechanical properties. Cellular structures take inspiration from nature such as structures of cork, corals, sponge, bone, honeycomb etc., which are often replicated to achieve desired strength. These designs, coupled with a suitable material, allow high strength-to-weight ratios, high heat transfer, energy absorption, and thermal insulation in the manufactured part which is beneficial for industries such as aerospace and health care where lower part weight  is a fundamental requirement. Â
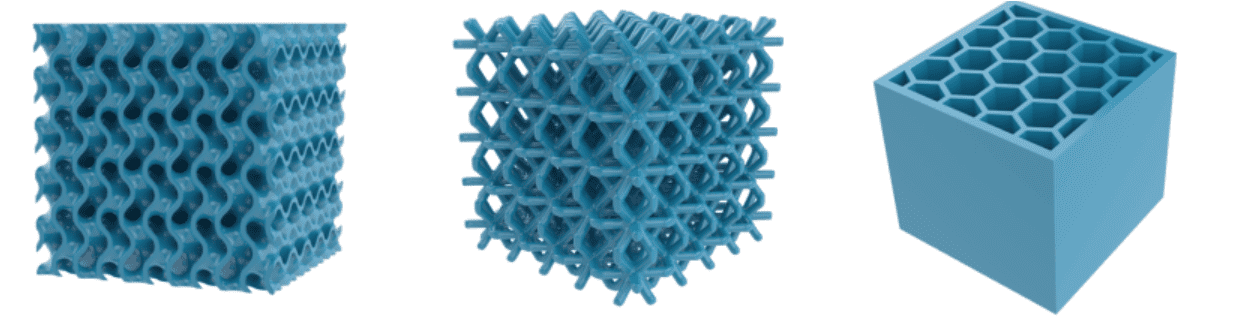
Fig. 1 (L to R): Types of lattice structures—surface based, strut based, planar based (Image Source: gen3d.com)
Many engineering components come with multiple parts that are independently designed and assembled to create a functional part. However, designing parts individually and further assembling with appropriate fasteners and welding, followed by NDT tests to eliminate losses, damage etc., are extremely laborious, increase lead time, and pose challenges in maintaining the spares for each part in case of failure. Additive manufacturing allows the designers to consolidate all the parts that are feasible to manufacture with AM in the design stage itself. DfAM accounts for part thickness, orientation, critical regions of failure, desired surface finish, and creates a model that is not only convenient to manufacture but also simplifies processes in supply chain and quality management systems.
Fig. 2 refers to a rectangular waveguide, a conducting cylinder of rectangular cross section used to guide the propagation of waves. The conventionally manufactured waveguide is manufactured in three segments followed by joining them either by welding or by fastening. If we choose to use fasteners, 103 parts are required for a foolproof assembly. However, there are chances of losses due to poor assembly or wear and tear. Additive manufacturing gives the freedom to consolidate 103 parts and bring the entire assembly count to one, thus eliminating the need for any test for losses or strength, besides improving the part life and efficiency.Â
Fig. 2: Rectangular wave guide—103 parts reduced to 1 (Image source: Unique Broadband Systems)
Heat sinks find application in diverse engineering domains such as transportation, aerospace, appliances etc., with a functional objective to effectively transfer heat—conductive material and design being determinants of its efficacy. However, despite selecting an appropriate conducting material, due to design constraints, conventional manufacturing systems restrict the freedom to increase the surface area of heat transfer. Due to the design freedom offered by AM, additively manufactured heat sinks enjoy the benefit of both highly conducting materials and also increased surface area of heat transfer, thus improving the efficiency and performance (Fig. 3).Â
Fig.3: Modified heat sink using principles of DfAM
Additive manufacturing is rapidly growing into a revolutionary technology that has the ability to transform design methodologies. Although it is not feasible to manufacture every part with AM, technically complex parts or high-mix, low-volume parts are often best candidates for AM. The DfAM approach integrates AM process parameters and materials and then designs parts to meet functional needs with a focus on creating value-added parts and providing industrial solutions. DfAM’s impact is not just limited to the part, but extends to the entire product ecosystem.Â
Subscribe to AM Chronicle Newsletter to stay connected:Â Â https://bit.ly/3fBZ1mPÂ
Follow us on LinkedIn:Â https://bit.ly/3IjhrFqÂ
Visit for more interesting content on additive manufacturing: https://amchronicle.com/
Â