In a world where used seats, mattresses, and insulated boxes are often discarded, the question arises: where will they eventually end up? Will they contribute to the growing problem of garbage disposal or find a way to be efficiently recycled? Polyurethane foams, a material widely used in many aspects of our lives, have long posed a challenge when it comes to their destination after being discarded.
In response to this long-standing challenge, Professor XIE Tao’s team from the College of Chemical and Biological Engineering at Zhejiang University has demonstrated a groundbreaking approach to upcycling commodity thermoset polyurethane foams to manufacture high-value, high-performance 3D photo-printing resins. Their research findings, published in the journal Nature Chemistry, offer a cost-effective and highly practical solution. This innovative method not only mitigates environmental burdens but also unleashes new possibilities, making it a promising alternative to polyurethane material disposal.
Back in the 1960s, polyurethane foams were developed to improve the safety and impact resistance of airplane seats. Thanks to their adjustability in hardness and ease of production, they have since found extensive use in manufacturing car seats, furniture mattresses, crash pads, insulation materials, thus becoming synonymous with “comfort” in our lives. Currently, the global annual production of polyurethane foams exceeds a staggering 12 million tons and 400 million cubic meters, enough to encircle the Earth’s equator 36 times if converted into standard 20-centimeter thick mattresses.
Regrettably, once this highly favored material reaches the end of its life cycle, it is often relegated to waste, either ending up in landfills or being incinerated, thereby posing a significant environmental burden. In the 1960s and 1970s, scientists endeavored to re-process the material at high temperatures and pressures, only to find that the performance of the re-processed material plummeted.
“The challenge of recycling has been around for years, and no ideal solution has emerged,” XIE Tao remarks. “Thermoset polyurethane foams are a type of crosslinked polymer network, very different from typical uncrosslinked polymer chains for thermoplastic polymers, their network structure makes it extremely difficult to depolymerize and reshape.”
In the quest to find an optimal “destination” for polyurethane foams, numerous efforts have been made over decades. At present, the most common approach involves “complete degradation”, where thermoset polyurethane foams are fully decomposed at high temperatures of 160 to 260 degrees Celsius for several hours. Some of the recovered polyols are then added to fresh polyols and isocyanates to produce new thermoset polyurethane foams. This approach can be likened to dismantling an entire LEGO house, picking out a few green blocks, and building a new structure. However, since only a portion of polyurethane foams are recycled, this process still generates a substantial amount of waste. “This approach is neither economical nor environmentally-friendly,” XIE Tao stresses.
It seemed like a dead end until XIE Tao and his team, inspired by a previous study, decided to approach the problem with a fresh perspective. They previously discovered that many thermoset polymer materials are not entirely ‘immutable’ and contain chemical bonds that are dynamically reversible, such as urethane bonds. These unique bonds can not only connect polymer chains to form a network structure but also open under specific conditions, allowing for the “loosening” of the internal network of polyurethane foams and partial degradation into non-crosslinked, active end-group-containing polymer oligomers.
“A material doesn’t just have two states: the finished state and the completely decomposed state. In fact, there are many ‘intermediate states’ in between!” Realizing this, Xie Tao’s team proposed to opt for the “useful intermediate states” and reprocess them into new materials. In other words, they didn’t have to completely dissemble the LEGO house into blocks; rather, they could break it down into a few bulky components and build a new house.
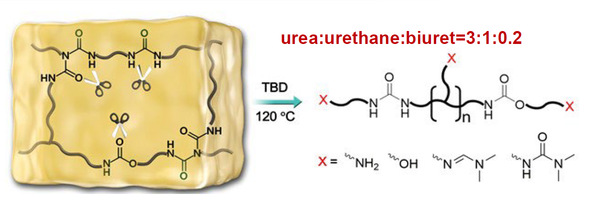
The research team found that this idea was feasible in polyurethane foams, and the process was simple. They heated polyurethane foams at 120 degrees Celsius for 20 minutes in the presence of a solvent and a catalyst. The urethane bonds would open, causing the “loosening” of the foams to yield dissolvable oligomers. With a further step of chemical modification, scientists then turned these oligomers into high-performance 3D photo-printing resins.
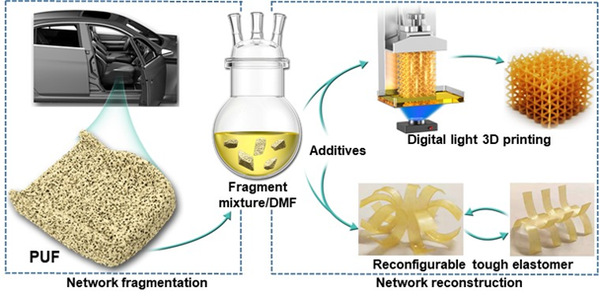
High-performance 3D printing liquid resins are relatively expensive, selling at approximately $50 per kilogram. XIE Tao’s team, however, demonstrated that polyurethane foams could be transformed into these resins in just four steps. This process involved degrading the foams into oligomers in DMF solvent and alkaline catalyst, chemical modifying the oligomer end-groups to enable 3D printing, performing photopolymerization for 3D printing, and finally, thermally treating the printed objects. Experimental results showed that these photo-printable resins exhibited tunable mechanical properties superior to many commercial high-performance counterparts.
The approach proposed by XIE Tao’s team boasts two distinct strengths: milder reaction conditions and the ability to convert the resulting mixture into new polymer materials without purification. This can not only reduce recycling costs significantly, but also open doors to the creation of various high-value products with remarkable performance.
In fact, recycling a 20-centimeter-thick mattress using this approach can yield 22 kilograms of high-performance 3D printing resins. In their future work, the research team aim to expand this approach to value-added upcycling of other thermoset polymer materials, offering a glimmer of hope in the ongoing battle against plastic waste.
Subscribe to AM Chronicle Newsletter to stay connected: https://bit.ly/3fBZ1mP
Follow us on LinkedIn: https://bit.ly/3IjhrFq
Visit for more interesting content on additive manufacturing: https://amchronicle.com