[ihc-hide-content ihc_mb_type=”show” ihc_mb_who=”reg” ihc_mb_template=”3″ ]
[vc_row][vc_column][vc_column_text]Credits – www.3dprintingindustry.com
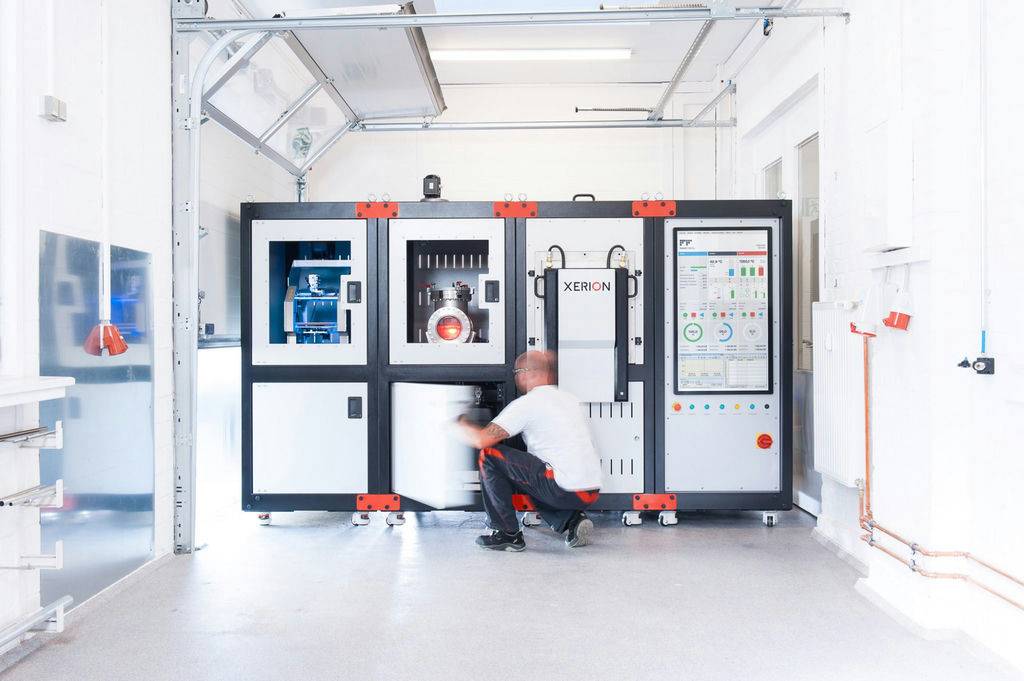
FDM/FFF metal printing
Dr. Uwe Lohse founded Xerion Advanced Heating in 1997. In 2016, a subsidiary called Xerion Berlin Laboratories was founded for the development of 3D printing technology. Both companies now form the Xerion Group.
Xerion’s latest achievement is an FDM-based metal 3D printer. As has been reported before, metal FDM/FFF printing is possible using metal composite filaments, such as The Virtual Foundry’s Filamet. Industrial companies are also experimenting with metal filaments. For example, Triditive is testing metal filaments made by the German chemical producer BASF.
However, metal filaments are mixed with polymers and therefore do not possess the extraordinary mechanical properties of pure metals.
Xerion’s Fusion Factory overcomes this limitation by combining printing, debinding, and sintering into one system. The Fusion Factory produces parts made purely of metal or ceramic, with a density between 98-99 percent.
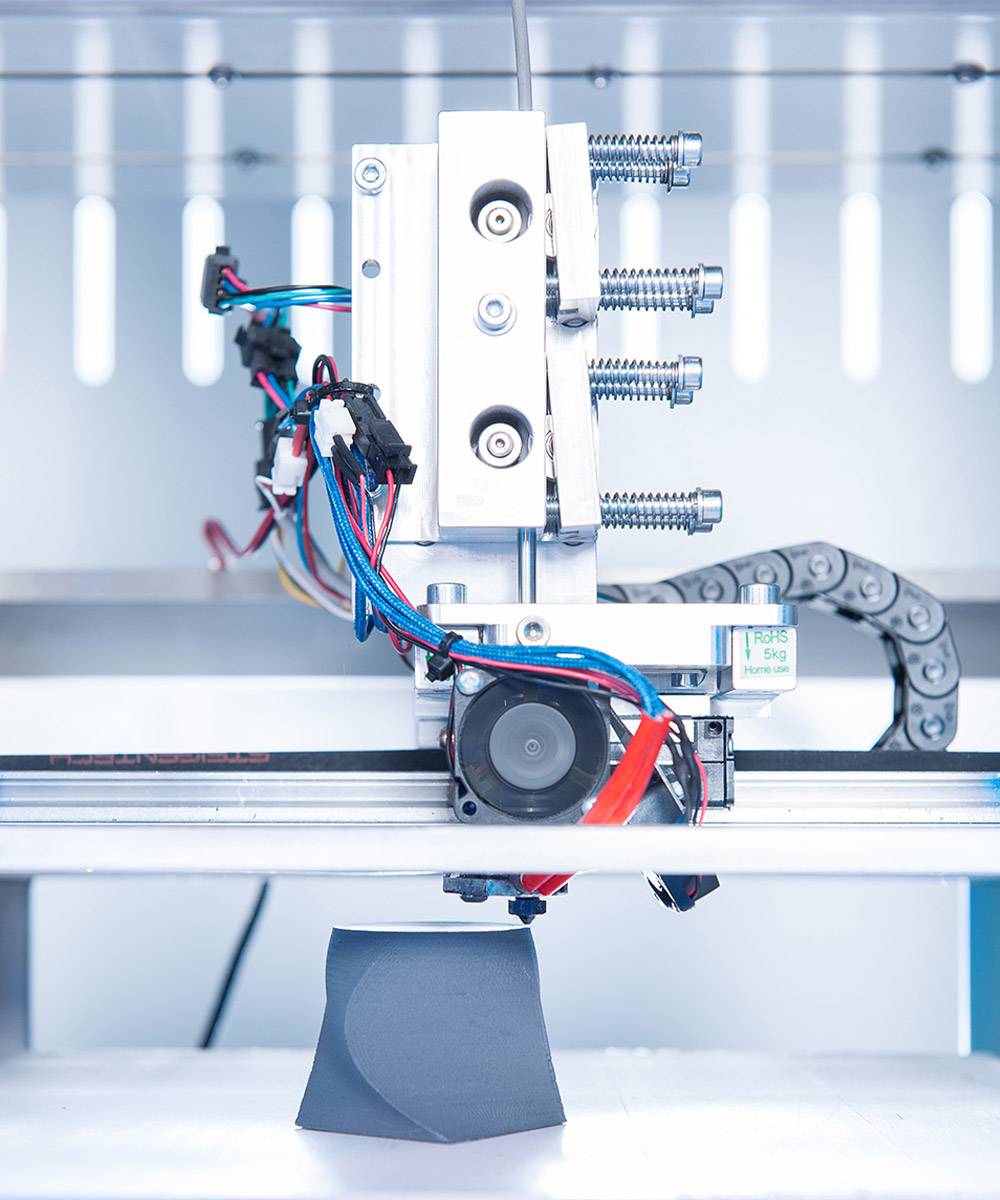
The Fusion Factory
The Fusion Factory is divided into three parts, a 3D printer, a debinding station, and an electrical furnace.
The 3D printer is like any FDM/FFF printer except with a modified nozzle and feed mechanism made of hundred-percent stainless steel. The printer can print metal or ceramic composite filament on a build volume of 24.5 cm x 23 cm x 20 cm.
Once a part is printed, it is moved to the debinding station where it is dipped into a chemical solution. This process is largely automated and the operator of the machine does not make contact with the chemical solution in any way.
After a few hours in the debinding solution, the part is removed. At this stage, the 3D printed part is free of non-metal particles and contains only metal (or ceramic, depending on the filament used). Therefore the part is fragile. To make into a fully finished metal (or ceramic) part, the component is transported to a specially designed electrical furnace. Here, it is sintered at a temperature above 1,000°C for more than ten hours. In the furnace the outer layers of the metal melt and fuse to make a full metal part.
Some part shrinkage does occur during sintering but this can be countered during the modeling stage.
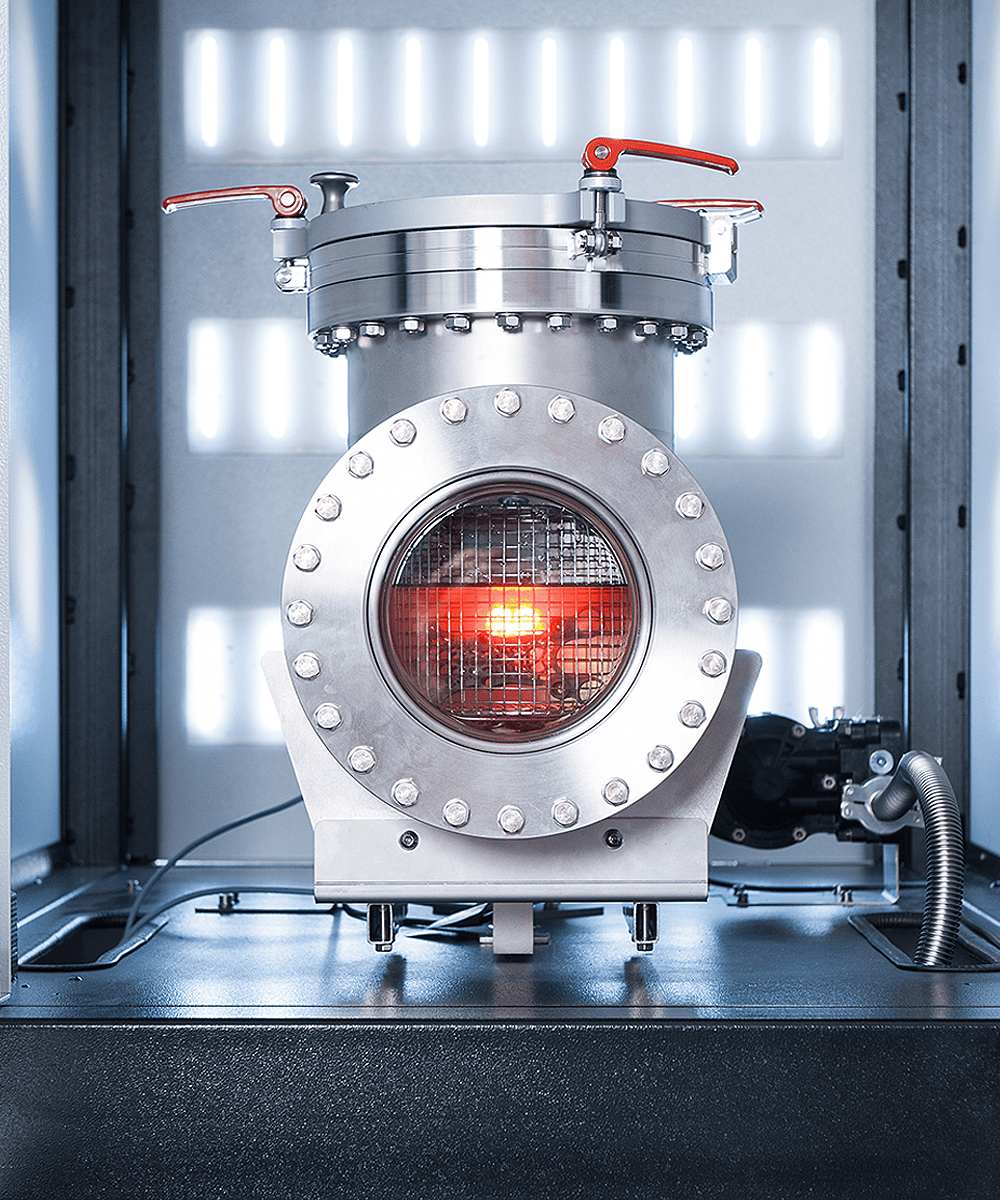
Future of the Fusion Factory
Currently available technology, in particular, metal powder fusion, can be inconvenient and hazardous, as the powder is inflammable. Using metal filament, Dr. Lohse explained, “You don’t have the problems with powder handling. Of course, filament is easy and convenient to handle. You have filament spools that you can swap out very quickly.”
Furthermore, FDM metal printing offers the option of adding infills to a part, which can increase its strength.
Dr Lohse further said, “The printer also features a dual extruder, which means that it can print with two different filaments at the same time, which opens up the possibility of mixing the filaments to produce parts made up of metal and ceramic compounds.”
In the future, the Xerion wants to make the debinding module without a solvent, and integrate a 3D scanner into the system that could compare the printed model with the CAD file to find inconsistencies.
The Fusion Factory system is priced at $283,000.[/vc_column_text][/vc_column][/vc_row]
[/ihc-hide-content]
The AM Chronicle Editorial Team is a collective of passionate individuals committed to delivering insightful, accurate and engaging stories to additive manufacturing audiences worldwide.