Wipro 3D, the metal additive manufacturing (AM) business of Wipro Infrastructure Engineering (WIN), and the Engine Division of Hindustan Aeronautics Ltd. (HAL) announced that their collaboration has resulted in the manufacture of a metal 3D printed aircraft engine component.
The collaboration will work towards development, manufacturing and airworthiness certification of a critical aero-engine component operating in the hot zone.
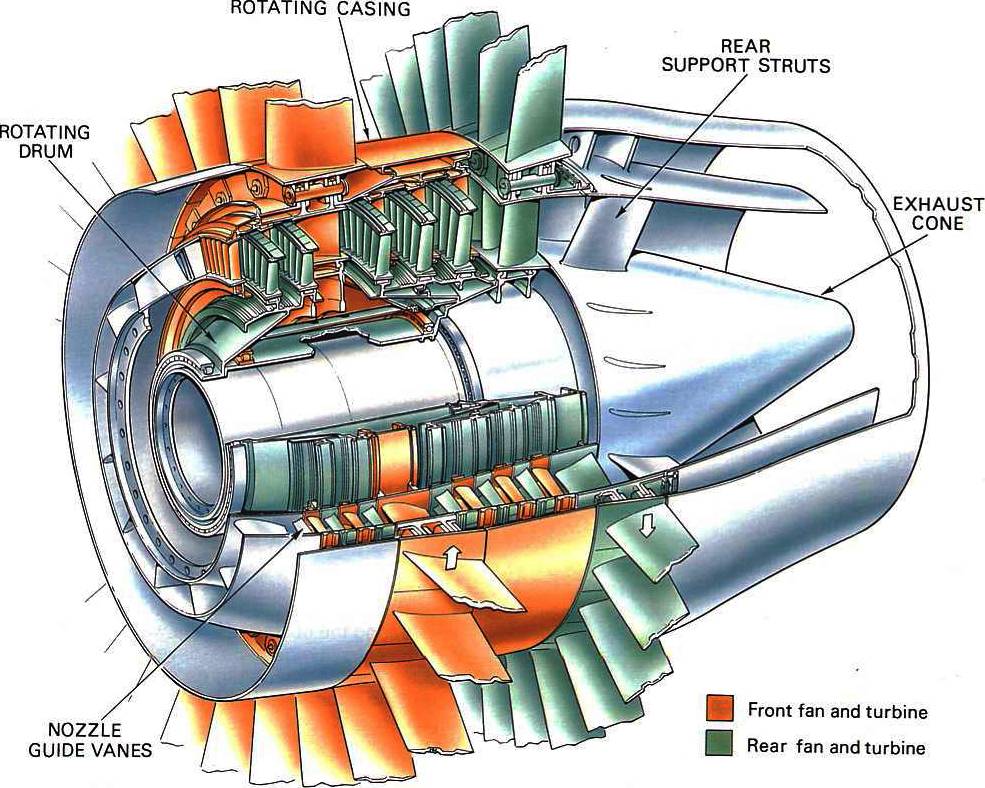
According to a statement released by Wipro3D, “The Nozzle Guide Vane (also called the Inner Ring), 3D printed in a high-temperature resilient steel A286, has been awarded Airworthiness certification by Centre for Military Airworthiness and Certification (CEMILAC), the regulatory body of Defence Research and Development Organization (DRDO).”
The statement also revealed that, “The Wipro3D manufactured components shall be installed in HAL manufactured helicopter engines.”
Commenting on this recent development, the CEO of Bangalore Complex, HAL, Amitabh Bhatt said, “Additive Manufacturing is a disruptive technology and is going to play a big role in the manufacture of components used in the Aerospace and Defence Industry in the future. Complimenting Wipro 3D and HAL Engine Division for successfully developing a 3D component for use in the hot section of an aero-engine.”
Bhatt added, “It is indeed a significant achievement towards ‘Aatmanirbhar Bharat’ Policy of Government of India.”
The latest collaboration follows the earlier MoU between the two organisations entered into last year in January 2020. This MoU relates to the design, development, validation, manufacture and repair of Aerospace components using metal 3D printing technology.
Under this MoU, validation is a key element that will help in accelerating the use of metal 3D printing in the aerospace industry.