A duo of engineers from the University of Auckland’s New Dexterity research group have published an academic paper detailing the design and construction of a partly 3D printed robotic airship. The authors, Gal Gorjup and Minas Liarokapis, have stated that the low cost, open source design featured in the work is intended for indoor use and will be used for educational and research purposes.
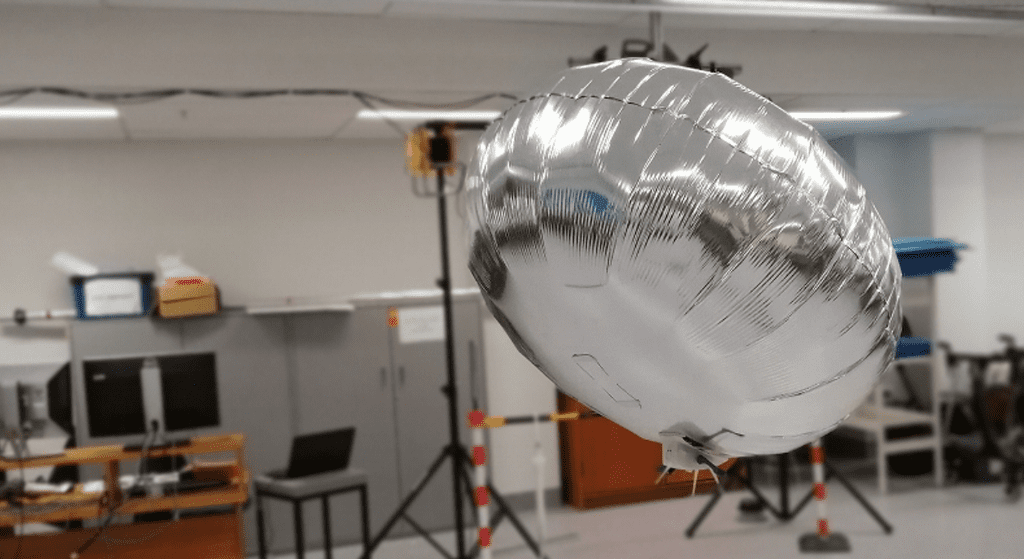
Miniature indoor robotic aircraft
When designing miniature aircraft for indoor use, there are a few things to consider. Firstly, it must be safe, especially if it will be in operation in a packed classroom. High speed contraptions with sharp edges and points are generally advised against due to the risk of eyeball impalement. There is also the issue of power consumption. Smaller wireless aircraft will have a limited onboard power supply due to a lack of space and, in turn, capacity.
The Auckland engineers, therefore, decided on an airship – a lighter-than-air (LTA) craft. LTA crafts rely on internal gases that are ‘lighter than air’, utilizing the difference in densities to stay afloat for longer without needing any extra power. They also tend to have a soft envelope and travel relatively slowly due to a lack of high speed rotors generating lift, so the risk of injury from collisions is minimized.
Design and construction
The first part of the project involved choosing the right lifting gas to fill the airship with. Gorjup and Liarokapis settled on helium over hydrogen or hot air due to its low density and lack of reactivity, making it a safe yet effective choice. Helium is nonrenewable, however, so choosing the right envelope material was also key to practicing financial and environmental responsibility.
The mechanical properties and helium retention capabilities of a number of contender materials were tested and evaluated by the duo. They looked at untreated latex balloons, latex balloons treated with Ultra Hi-Float, clear bubble balloons, and microfoil balloons. The lifting forces and surface areas of the balloons were measured daily over the course of 16 days. Eventually, the duo settled on microfoil for the envelope material due to its low strain rate, high tensile strength, and low cost.
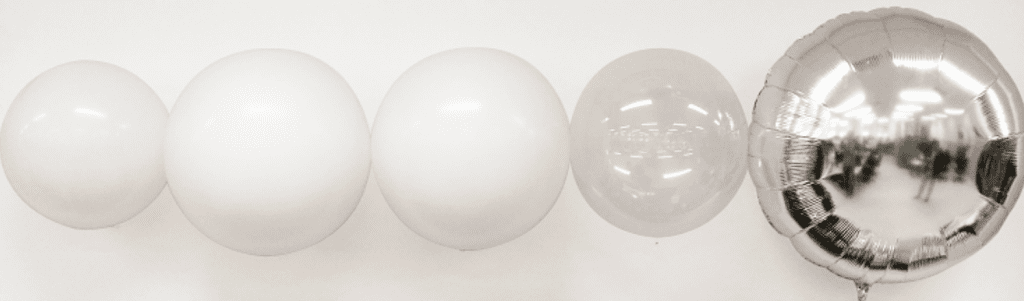
The final portion of the project involved designing the gondola on the underside of the envelope. The gondola was 3D printed and housed a Raspberry Pi Zero W, the motor drivers, a set of DC motors, a step-up voltage regulator, three propellers and a camera to provide a dynamic viewing angle. All in all, the components cost around $90 in total. The gondola was secured to the underside of the microfoil envelope with velcro straps.
After finalizing the design, the engineers concluded that the airship would be suitable for education and research while being both financially and environmentally viable, with students being able to develop and test PID controllers for use with the airship. The open source nature of the physical design also allows for customization and optimization, giving students an opportunity to develop their CAD and rapid prototyping skills.
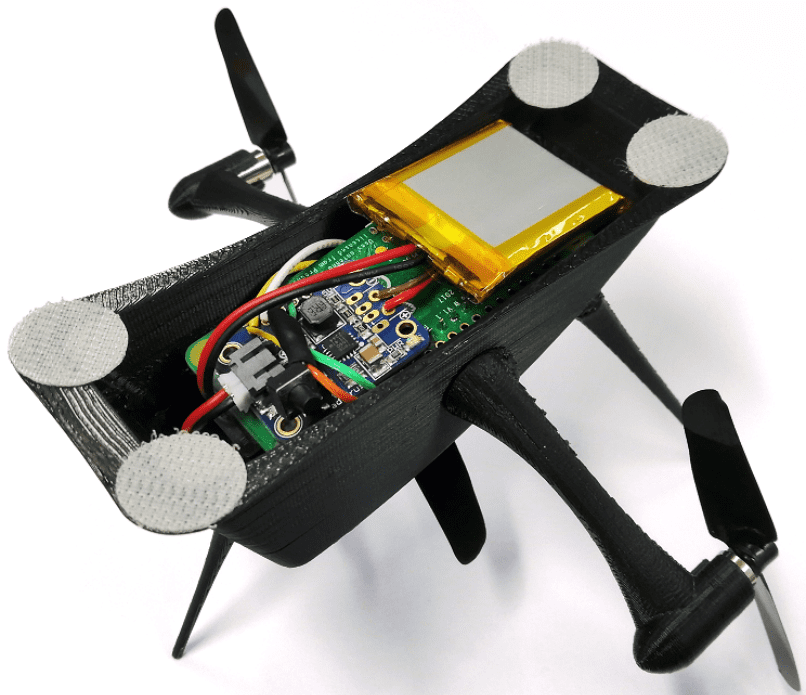
Full details of the design and evaluation of the airship can be found in the paper titled ‘A Low-Cost, Open-Source, Robotic Airship for Education and Research’. It is published in the IEEE Access collection.
The design freedom granted by 3D printing makes it perfect for highly customizable remote controlled vehicles such as drones. Last year, SkyBox Engineering teamed up with Italian 3D printer manufacturer Roboze to produce dampers for an unmanned drone. Made from Carbon PA, the dampers were designed to absorb the vibrations generated by the high speed motors. Elsewhere, in Bengaluru, direct metal laser sintering specialist Poeir Jets developed India’s first 3D printed heavy lift hybrid drones. The drones are designed to lift up to 75kg for 120 minutes at a time.