Can a machine be trained to paint like Jackson Pollock? More specifically, can 3D printing harness Pollock’s distinctive techniques to quickly and accurately print complex shapes?
“I wanted to know, can one replicate Jackson Pollock, and reverse engineer what he did?” said L. Mahadevan, the Lola England de Valpine Professor of Applied Mathematics at the Harvard John A. Paulson School of Engineering and Applied Sciences (SEAS), and Professor of Organismic and Evolutionary Biology, and of Physics in the Faculty of Arts and Sciences (FAS).
Mahadevan and his team combined physics and machine learning to develop a new 3D-printing technique that can quickly create complex physical patterns—including replicating a segment of a Pollock painting—by leveraging the same natural fluid instability that Pollock used in his work.
The research is published in Soft Matter.
3D and 4D printing has revolutionized manufacturing but the process is still painstakingly slow.
The issue, as it usually is, is physics. Liquid inks are bound by the rules of fluid dynamics, which means when they fall from a height, they become unstable, folding and coiling in on themselves. You can observe this at home by drizzling honey on a piece of toast.
More than two decades ago, Mahadevan provided a simple physical explanation of this process, and later suggested how Pollock could have intuitively used these ideas to paint from a distance.
Reinforcement-learning controlled cursive handwriting using silicone oil. Credit: Soft Math Group/Harvard SEAS
Today, most 3D and 4D printing techniques place the print nozzle millimeters from the surface, all but eliminating the dynamic instability of the liquid stream.
But Mahadevan has a motto: Use the physics, instead of avoiding it.
“We wanted to develop a technique that could take advantage of the folding and coiling instabilities, rather than avoid them,” said Gaurav Chaudhary, a former postdoctoral fellow at SEAS and first author of the paper.
Pollock composed his famous drip paintings by placing a canvas on the floor and drizzling, pouring, dripping and splashing paint onto it from above. To the untrained eye, his technique may seem haphazard, but Pollock always claimed he had complete control over the flow of the paint.
Dubbed “action painting,” Pollock drew in the space above the canvas—creating shapes in the air that would fall to the canvas below.
“If you look at traditional 3D printers, you supply them a path from point A to point B and the nozzle deposits ink along that specified path,” said Chaudhary. “But Pollock’s approach of throwing paint from a height meant that even if his hand was moving in a specific trajectory, the paint didn’t follow that trajectory because of the acceleration gained from gravity. A small motion could result in a large splatter of paint. Using this technique, you can print larger lengths than you can move because you gain this free acceleration from gravity.”
The question was, how to control it?
To learn how to manipulate the nozzle to print at a distance and control fluid coiling, Mahadevan and Chaudhary, along with co-authors Stephanie Christ, a former student in Mahadevan’s Soft Math Lab, and A. John Hart, Professor of Mechanical Engineering at MIT, combined the physics of coiling with deep reinforcement learning, which is an algorithmic approach to improving performance iteratively. Mahadevan and his team used techniques developed by Petros Koumoutsakos, the Herbert S. Winokur, Jr. Professor of Computing in Science and Engineering at SEAS.
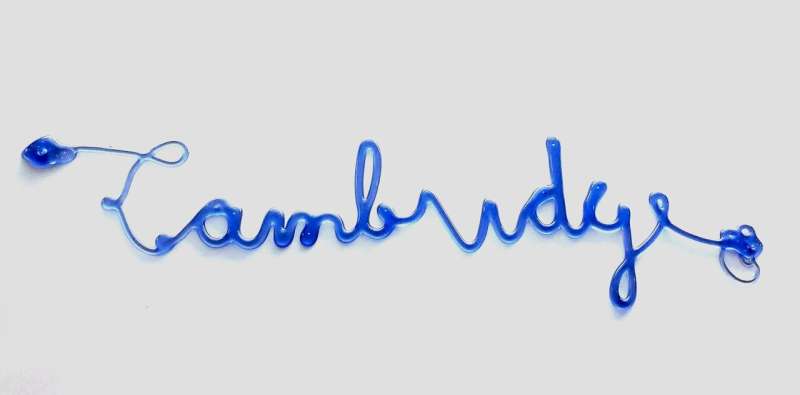
“With deep reinforcement learning, the model can learn from its mistakes and get more and more accurate with each trial,” said Chaudhary.
Using this technique, the researchers printed a series of complex shapes, painting like Pollock and even decorating a cookie with chocolate syrup.
The researchers used simple fluids for this research, but the approach could be expanded to include more complex fluids, such as liquid polymers, pastes and various types of foods.
“Harnessing physical processes for functional outcomes is both a hallmark of intelligent behavior, and at the heart of engineering design. This little example suggests, once again, that understanding the evolution of the first might help us be better at the second,” said Mahadevan.
As the research continues, there is no telling where Mahadevan may look for inspiration next.
“When you’re in Maha’s lab, nothing is off the table,” said Chaudhary.
Subscribe to AM Chronicle Newsletter to stay connected:Â Â https://bit.ly/3fBZ1mPÂ
Follow us on LinkedIn:Â https://bit.ly/3IjhrFqÂ
Visit for more interesting content on additive manufacturing:Â https://amchronicle.com