[ihc-hide-content ihc_mb_type=”show” ihc_mb_who=”reg” ihc_mb_template=”3″ ]
[vc_row][vc_column][vc_column_text]Credits – www.3dprint.com
That’s why Aditya Mahadik and Dr. Dale Masel, a pair of researchers from Ohio University (OU), are focusing on AM cost estimation instead, so users can learn more about the trade-off between cost and design changes.
The two wrote a paper, titled “Implementation of Additive Manufacturing Cost Estimation Tool (AMCET) Using Break-down Approach,” about their efforts to create a tool that can help engineers and designers understand the full cost impact of 3D printing at the beginning of the process.
The abstract reads, “The aim of this research is to develop an additive manufacturing cost estimation tool (AMCET) using a break-down approach. The total cost is an addition of costs for machine, material, labor, and post-processing, which are calculated using a limited number of primary user input parameters. If additional part or process parameters are available, the user can enter the secondary input parameters to increase the accuracy of an estimate. The build time is estimated by considering the activities undergone by machine for preparation of a single layer and multiplying it by the total number of layers.”
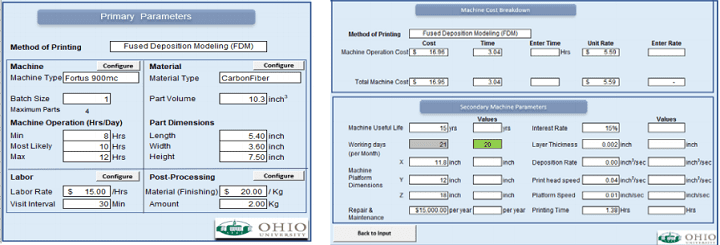
Cost estimation, or CE, can be used to help companies set product pricing, determine business potential, prepare budgets, and perform break-even analyses, in addition to providing customers with accurate quotations and helping entrepreneurs make decisions about manufacturing process and product design changes. How much any given product costs depends on the resources – like tooling, material, machine, and labor – that are used to make it. In order to properly estimate how much a company will spend manufacturing a certain product, it should estimate the cost associated with all of these resources.
The OU researchers used a breakdown approach in their AMCET, which calculates the cost components by “taking limited information from the user to support quick CE of a design when manufactured using one of seven different AM processes.”
“Time estimation is crucial for predicting cost because cost is directly proportional to the time to manufacture the product,” the researchers explained. “Build time of the product is estimated by calculating time required to prepare a single layer and total number of layers. The time required for a single layer is estimated by examining critical activities such as time to move the printer head, time to deposit material, time to fuse the material for forming a layer, and the time to lower the platform after preparing a layer.”
[/vc_column_text][vc_single_image image=”4493″ img_size=”full” add_caption=”yes” alignment=”center”][vc_column_text]AMCET calculates the total cost of a part by adding together machine, material, labor, and post-processing costs. The tool separates these four components into five different levels:
- Primary user input for cost components
- Additional user information to increase estimate accuracy
- Cost-component parameters calculated from primary and secondary parameters
- Sub-component cost estimates calculated based on Level 3 parameters
- Component cost estimate generated by the addition of sub-component cost estimates
“The user can analyse the contribution made by the individual cost components,” Mahadik and Dr. Masel explained. “The AMCET provides the cost of different part designs (batch) and cost of single part. The actual usage and the rate individual cost components is also estimated by AMCET to perform the detailed analysis.”
In the OU experiment, the estimates that the AMCET generated were validated by using three different 3D printing processes to manufacture two parts, and then compared the results with the true cost. According to the results, the cost of PolyJet 3D printing was estimated with 12.87% error, 14.65% for SLA 3D printing, and 19.14% for FDM 3D printing.[/vc_column_text][vc_single_image image=”4494″ img_size=”full” add_caption=”yes” alignment=”center”][vc_column_text]
“AMCET supports the quick cost estimation of AM parts by allowing the user to provide limited information. The user can refine the estimate based on availability of data for accurate cost estimation. The estimates generated by AMCET are with some errors but accurate enough for the estimation purpose. This helps selection and comparison of desired AM process based on the time and the cost constraint,” the researchers concluded.
“The companies investing in AM can make the use of AMCET to determine a break-even point to analyse the investment. Unlike, other AM cost estimation software’s where loading of .STL file is mandatory to generate an estimate, AMCET can generate an estimate by entering primary and secondary parameters. This will ensure engineering companies to protect their designs by not having to share it outside an organization.”
[/vc_column_text][/vc_column][/vc_row]
[/ihc-hide-content]
The AM Chronicle Editorial Team is a collective of passionate individuals committed to delivering insightful, accurate and engaging stories to additive manufacturing audiences worldwide.