A research team led by the University of Glasgow has developed a 3D printable carbon nanotube-based plastic material capable of sensing its own structural health.
More from the News
Inspired by porous cellular forms like beehives, sponges, and bone found in the natural world, the novel material is reportedly tougher, stronger, and smarter than comparable conventional materials, and could find new applications in medicine, prosthetics, automotive and aerospace design, where low-density, tough materials with self-sensing abilities are desirable.
“Nature has a lot to teach engineers about how to balance properties and structure to create high performance lightweight materials,” said Dr. Shanmugam Kumar of the University of Glasgow’s James Watt School of Engineering.
“We’ve Taken Inspiration From These Forms To Develop Our New Cellular Materials, Which Offer Unique Advantages Over Their Conventionally Produced Counterparts And Can Be Finely Tuned To Manipulate Their Physical Properties.”
3D printing carbon nanotubes
First discovered in 1991, carbon nanotubes have since gained a reputation for their desirable mechanical properties. Hailed as being up to a hundred times stronger than steel, harder than diamonds, and a thousand times more conductive than copper, carbon nanotubes hold potential for a range of potentially significant industrial applications, such as electronics and water purification filters, and can be used to develop composite materials with superior mechanical, thermal, and conductive properties.
To date, carbon nanotube materials have been used to 3D print shape memory polymers for use in soft robotics applications and to 3D print biocompatible tissue scaffolds.
Despite their promise, though, leveraging carbon nanotubes for 3D printing still presents several challenges. One such challenge is the spaghetti effect which commonly occurs when carbon nanotubes tangle together during printing, although researchers from Rice University have developed a novel solvent that could overcome this obstacle and enable the scale-up of industrial 3D printing with hydrocarbons.
Elsewhere, Arizona-based start-up Mechnano believes its own carbon nanotube technology for 3D printing materials could bring “dramatic changes” to the aerospace, defense, medical and automotive industries.
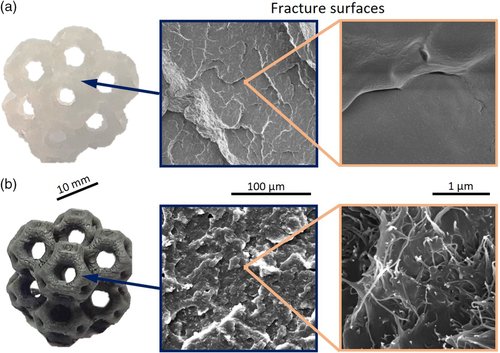
Self-sensing materials
Integrating sensing ability into a material is useful for monitoring the in situ deformation state or damage state of a structure. For instance, self-sensing lattices can be used as smart rehabilitation assistive devices and material architecture for soft robotics where sensing, control, and actuation are essential for increasing the efficiency of a robot’s function.
To form their novel material, the University of Glasgow Team combined a common polypropylene (PP) industrial plastic with carbon nanotubes to create a material that is reportedly tougher, stronger, and smarter than comparable conventional materials.
Integrating carbon nanotubes into the otherwise non-conductive plastic allowed it to carry an electric charge throughout its structure that changes when subjected to mechanical loads. This is known as piezoresistivity and gives the material the ability to “sense” its own structural health.
Leveraging the novel material, the team investigated the energy absorbing and self-sensing characteristics of three different 3D printed nanoengineered designs inspired by porous materials like beehives, sponges, and bone found in the natural world.
Utilizing an FFF additive manufacturing process, the researchers created a series of intricate designs with mesoscale porous architectures to produce designs with reduced weight and improved mechanical performance.
“The polypropylene random co-polymer we’ve chosen offers enhanced processability, improved temperature resistance, better product consistency, and better impact strength,” said Kumar. “The carbon nanotubes help to make it mechanically robust while imparting electrical conductivity.
“We Can Choose The Extent Of Porosity In The
Design And Architect The Porous Geometry
To Enhance Mass-Specific Mechanical Properties.”
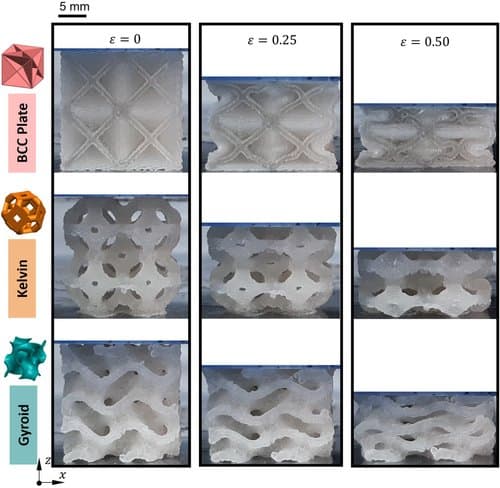
Fulfilling industry demand for self-sensing parts
The researchers tested a total of three differently-shaped porous designs, and found a cube-shaped “plate-lattice” structure exhibited the most effective combination of mechanical performance and self-sensing ability.
When subjected to monotonic compression – continual compression that neither increases nor decreases – the lattice structure showed an energy absorption capacity similar to that of nickel foams of the same density. The structure also reportedly outperformed several other similarly dense conventional materials.
Having observed the enhanced mechanical properties of their 3D printed designs, the team believes its smart material could find new applications within medicine, prosthetics, and automotive and aerospace design.
As these sectors increasingly focus on lightweight engineering, the researchers say there is a continual drive for developing low-density lattices with excellent mass-specific properties. Within these fields, the team sees its material fulfilling a growing demand for low-density, tough materials with self-sensing abilities.
“Lightweight, tougher, self-sensing materials like these have a great deal of potential for practical applications,” Kumar added. “They could help make lighter, more efficient car bodies, for example, or back braces for people with issues like scoliosis capable of sensing when their bodies are not receiving optimal support. They could even be used to create new forms of architected electrodes for batteries.”
Further information on the study can be found in the paper titled: “Multifunctionality of nanoengineered self-sensing lattices enabled by additive manufacturing,” published in the Advanced Engineerings Materials journal. The study is co-authored by J. Ubaid, J. Schneider, V. Deshpande, B. Wardle, and S. Kumar.
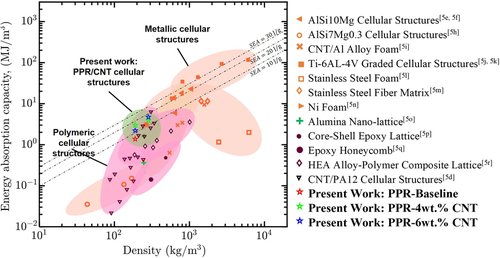
Subscribe to AM Chronicle Newsletter to stay connected: https://bit.ly/3fBZ1mP
Follow us on LinkedIn: https://bit.ly/3IjhrFq
Visit for more interesting content on additive manufacturing: https://amchronicle.com/