A company out of Brisbane, Australia, has developed a manufacturing technology that combines 3D printing with injection molding. Cobalt Extreme works on producing technology geared for the engineering and manufacturing of innovative artificial lift equipment for oil production.
The company’s performance materials laboratory has developed a material concept called Synthetic Metal (worldwide patents pending), which was originally developed for extreme environments in deep oil wells. This technology also has the potential to open up applications in new markets.
David Nommensen, director of Cobalt Extreme, said that the biggest advantage of Synthetic Metals is the processability, mainly by injection molding a unique polymer in and around a metal endoskeleton.
“The injection molded polymer in and around the metal endoskeleton is not conductive and becomes an insulator, in addition to other benefits of the injection molded materials such as abrasion resistance, resiliently deformable, cost, impact resistance, non-corrosive, chemical resistance, color, temperatures, weight, etc.,” he said.
The company’s Synthetic Metal and Arpmax polymer technology combines the electronic characteristics of metal with the engineering properties of polymers.
“A metal endoskeleton creates mechanical strength to a polymer (think reinforced concrete),” he said. “Imagine a human body without a skeleton.”
Applications
An example of an application for Synthetic Metal is for electrolytic protection corrosion control in oil wells. Nommensen said that a sucker rod is a magnet for corrosion in the presence of water and chemical compounds H2S, CO2, and O2. Cobalt Extreme created the Cobalt Synthetic Metal sucker rod guide anodes to combat this.
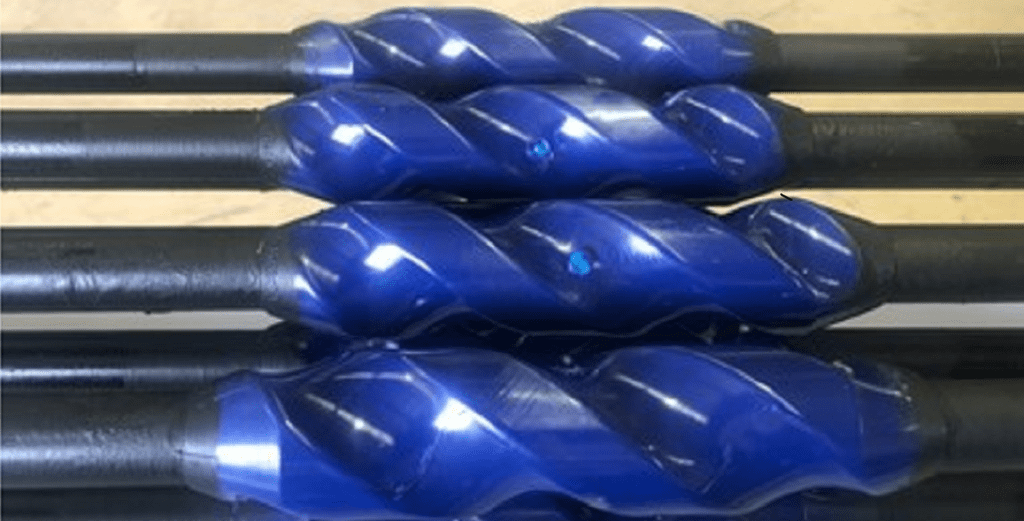
The process is unique in combining 3D metal printing of the anode matrix to align with the very specific shape of the company’s existing sucker rod guide designs. Nommensen said the design of the 3D metal printed anode matrix is in two halves that are snapped on to the rod prior to the injection molding of the spiral rod guide. The hydrodynamic design has taken into account anode thickness, strength, openness, consistent surface contact to ensure that the function of original centralizer is not compromised and that sufficient surface contact is made to create the required electrical circuit to be effective in preventing corrosion.
Nommensen said the current alternatives for managing corrosion in oil and gas wells are either preventative coatings (epoxy coatings, thermal spray metal coatings) or the injection of liquid corrosion inhibitor such as chemical treatment. The installation of Synthetic Metal anodes reverses the galvanic action and the corrosion then reacts on the anode rather than the tubing and the rods.
The Synthetic Metal anode is contained within an injection molded Arpmax polymer to both ensure the controlled cathodic protection of the metal sucker rod and the sucker rod are effectively centralized via the polymer guide/centralizer with the well production tubing.
“The Synthetic Metal innovation is to utilize advanced additive manufacturing technologies to combine proven anode metallurgy with Arpmax polymer technology to create a polymer with the electrical/ thermal/conductivity and the structural strength of metal,” he said.
Currently, Cobalt Extreme works with ProX DMP 320 metal printing technology and injection molding equipment, sourcing unique metal alloys and organic polymer materials suited to individual product characteristics.
Other potential applications of Synthetic Metal in conjunction with its Arpmax range of polymers include electronics, marine, aerospace, sports, medical and military.
“The Synthetic Meta technology also has significant non-oil field applications looking for a polymer with the electrical, thermal conductivity and structural strength of metal,” Nommensen said. “Synthetic Metal offers new and unique material characteristics, which have yet to be fully explored.”
Head - Marketing at Indian 3D Printing Network. Communications is an integral part of an organisation. It is the image an organisation portrays to the intended target audience. Understanding the immense responsibility this puts on me and deliver accordingly has always been and will continue to be my objective.