Huntington Ingalls Industries, the largest military shipbuilding company in the U.S., has produced a 3D printed piping assembly for nuclear-powered warships.
The additively manufactured metal component will be installed on U.S. Navy aircraft carrier, the USS Harry S. Truman (CVN 75), where it will be evaluated over the course of a year.
“The advancement of additive manufacturing will help revolutionize naval engineering and shipbuilding,” said Charles Southall, Vice President of engineering and design at Newport News Shipbuilding, a division of Huntington Ingalls Industries.
“IT ALSO IS A SIGNIFICANT STEP FORWARD IN OUR DIGITAL TRANSFORMATION OF SHIPBUILDING PROCESSES TO INCREASE EFFICIENCY, SAFETY, AND AFFORDABILITY. THIS IS AN ACCOMPLISHMENT WE ALL SHOULD BE PROUD OF.”
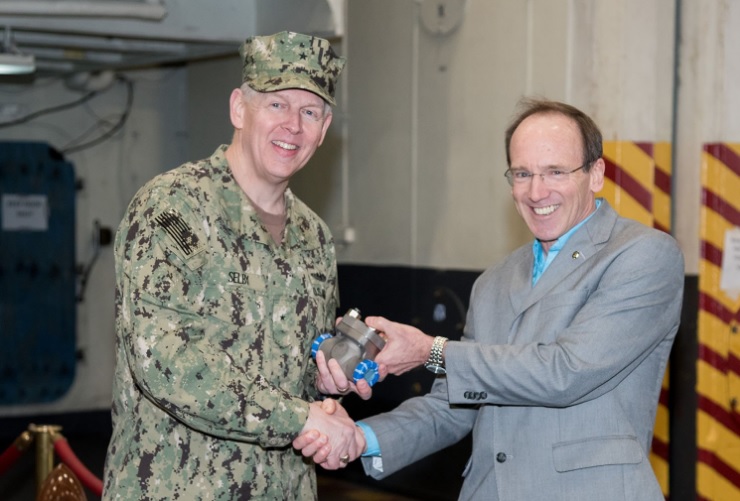
3D printed parts at sea
Last year, the U.S. Navy’s Naval Sea Systems Command (NAVSEA) and HII approved the technical standards for 3D printing. This was done to enable cost and time efficient processes for naval ships. As such the partners, as well as other shipbuilding manufacturers, began thorough tests of 3D printed parts and materials, through an engineered test program.
According to HII, the 3D printed piping assembly is the first transformational part to be installed on a nuclear-powered aircraft carrier. A few months prior, NAVSEA approved the first 3D printed part, a prototype drain strainer orifice (DSO) assembly, for shipboard installation on the CVN 75.
This metal 3D printed prototype, a steam system component, passed functional and environmental testing, which involved the evaluation of material, welding, shock, vibration, hydrostatic, and operational steam. HII proposed installing the DSO assembly on the CVN 75 ship for test and evaluation.

Huntington Ingalls Industries, NAVSEA & additive manufacturing
HII’s Newport News Shipbuilding division is actively working to qualify metal additive manufacturing for use in the construction of naval warships. Through a naval warship building contract with 3D Systems, the division has integrated several ProX DMP 320 industrial 3D printers to shift elements of its production to additive manufacturing.
With this technology, Newport News Shipbuilding ultimately aims to produce “marine-based alloy replacement parts for castings as well as valves, housings and brackets – for future nuclear-powered warships.”
Furthermore, as the largest of the U.S. Navy’s five systems commands, NAVSEA has previously integrated new technologies such as additive manufacturing to advance overall ship maintenance.
The command has 3D printed a tie bolt anti-rotation tool used for fixing structurally supportive frames and trusses, an F-35 stealth fighter landing gear door component, and flip-top valves for oxygen masks worn by Naval aircraft crews.
Source: 3dprintingindustry