Scientists at Harvard University have unveiled a groundbreaking 3D printing technique that allows for unprecedented control over the properties of liquid crystal elastomers (LCEs), a class of “smart” materials known for their ability to change shape in response to external stimuli like heat or light. This innovative approach, published in the journal Science, opens up exciting possibilities for creating complex structures with precisely programmed shape morphing and mechanical behaviors, paving the way for advancements in fields ranging from robotics and aerospace to biomedical devices and wearable technology.
Understanding Smart Materials in 3D Printing
LCEs are composed of long, chain-like molecules that can be aligned in specific directions, giving the material anisotropic properties – meaning its behavior differs depending on the direction. This alignment, known as the mesogen alignment, dictates how the material will deform when triggered. Previously, controlling this alignment during the fabrication process has been a significant challenge, limiting the complexity of LCE structures and their functionality.
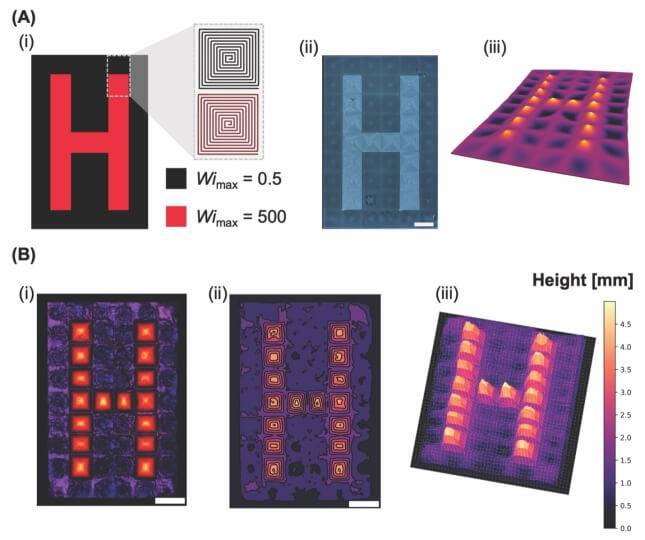
The Harvard team, led by Jennifer A. Lewis, the Hansjörg Wyss Professor of Biologically Inspired Engineering at the Harvard John A. Paulson School of Engineering and Applied Sciences (SEAS), has overcome this hurdle by developing a novel 3D printing method combined with real-time X-ray characterization. This technique allows them to not only print LCEs with intricate geometries but also simultaneously control the molecular alignment at the microscale, effectively “encoding” multiple properties into a single material.
“Our approach allows us to write complex patterns of mesogen alignment within the printed material,” explains lead author, Dr. Qiming Zhao, a postdoctoral fellow at SEAS. “This level of control unlocks the potential to create LCE structures with unprecedented functionality, where different regions can exhibit distinct responses to the same stimulus.”
The key to their breakthrough lies in the integration of an X-ray microbeam directly into the 3D printing setup. This allows the researchers to probe the liquid crystal alignment in real-time, during the printing process, providing immediate feedback on the material’s microstructure. This feedback loop is crucial for precisely controlling the alignment as the material is being deposited, layer by layer.
To demonstrate the capabilities of their new method, the researchers designed and printed a series of “H” shaped structures. By manipulating the printing parameters, they were able to create regions within the “H” with different mesogen alignments, resulting in a structure that bends and twists in a complex, pre-determined manner when exposed to heat. This precise control over shape morphing is a significant leap forward compared to previous methods, which typically only allowed for uniform alignment throughout the entire structure.
Furthermore, the team explored the use of different nozzle shapes – tapered and hyperbolic – to manipulate the flow of the LCE ink during printing. This allowed them to create filaments with varying alignment profiles. They successfully fabricated two distinct types of filaments: one with an outer layer of well-aligned molecules surrounding a poorly aligned core, and another with uniform alignment throughout the cross-section. This level of control over the filament microstructure opens up new possibilities for designing LCE structures with tailored mechanical properties.
The researchers used an X-ray microbeam, during printing, to locally measure liquid crystal alignment and direction inside the printer nozzle. This real-time characterization capability is essential for understanding and optimizing the printing process and for achieving the desired level of control over the mesogen alignment.
The implications of this research are far-reaching. Imagine a soft robot that can adapt its shape and stiffness on demand, navigating complex environments and performing delicate tasks. Or consider a wearable device that conforms perfectly to the body, providing personalized thermal regulation. This new 3D printing method brings these possibilities closer to reality.
“This work provides a powerful new tool for designing and fabricating smart materials with programmable functionalities,” says Professor Lewis. “We believe this approach will have a transformative impact on a wide range of applications, from soft robotics and adaptive optics to biomedical implants and advanced textiles.”
The researchers are now exploring the use of this technique to create even more complex LCE structures with multiple, independently controllable regions. They are also investigating the use of different stimuli, such as light or magnetic fields, to trigger shape changes in the printed materials. With this innovative approach, the future of smart materials and their applications looks brighter than ever.
Original Source