Sweden-based materials firm Gränges Powder Metallurgy has launched its very first additive manufacturing powder.
More from the News
Developed as part of the company’s DISPAL family of materials, AM S220 (AlSi35) is a high-performance aluminum alloy suitable for laser powder bed fusion 3D printing. The material is characterized by its high stiffness, low thermal expansion, excellent wear and tear behavior, good machinability, and low density.
According to Gränges, the alloy’s properties are similar to those of steel, except it’s a third of the weight. This makes it a strong choice for performance applications in sectors such as aerospace and automotive.
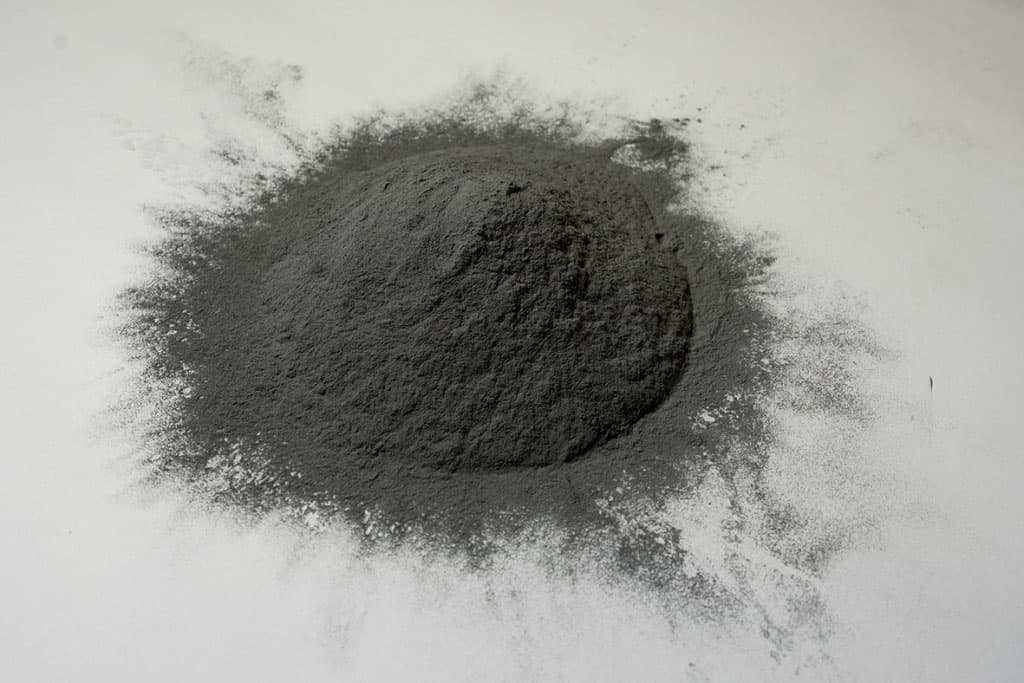
30 years of aluminum powder manufacturing
Gränges boasts over 30 years of experience in aluminum powder manufacturing. The company actually developed and commercialized its original DISPAL S220 alloy back in the 1980s as part of a wider materials family. As such, S220 isn’t actually new, but its use in laser powder bed fusion marks Gränges’ debut in the 3D printing sector.
To complement the new AM S220 offering, the firm is currently working on creating an entire product line of aluminum-based 3D printing powders, which are expected to be launched before the end of 2022.
What makes AM S220 unique?
Gränges’ AM S220 alloy is special in that it has a high silicon content, giving it a unique blend of low density and low coefficient of thermal expansion (CTE). The low CTE is what enables the powder to maintain high precision under extreme stresses and temperatures, making it a great choice for 3D printed precision robotics. The property also allows the material to preserve accurate communication over large distances, meaning it’s also suitable for optical applications in space.
Additionally, the fine silicon particles in the alloy are evenly distributed, which lends itself to excellent wear and friction characteristics
“I am not aware of any other alloy on the AM market that has such a low CTE,” stated Greta D’Angelo, Business Development Manager at Gränges Powder Metallurgy. “In the past, we had many success stories of customers replacing steel and carbon fiber applications with the conventional DISPAL S220. Now, we are excited to offer the same material for Additive Manufacturing, giving our customers the opportunity to take advantage of even more geometrical freedom in the design of their next-generation products.”
Although AM S220 is not yet commercially available, Gränges is offering a dedicated 3D printing service through its global network of manufacturing partners. As well as part printing, the service also includes aid with part selection, development, and quality assurance.
“We want to support our customers through the whole process, and deliver finished components of high quality, being that prototypes or serial production,” adds D’Angelo. “We are aware that onboarding a new material can be a daunting process, especially for a new technology like AM, therefore we take care of that part for our customers so that they don’t have to worry about it.”
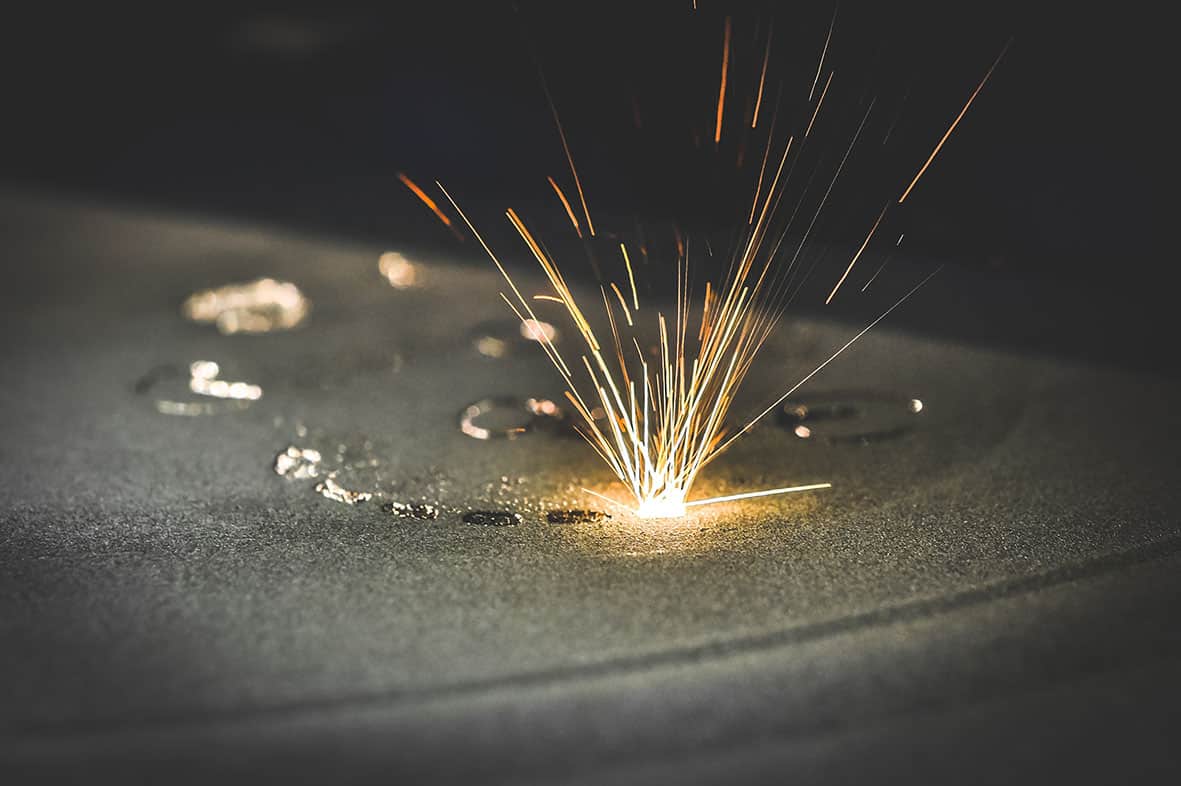
The 3D printing materials sector is as active as ever. Just this month, engineering firm Sandvik announced the development of a novel 3D printable cemented carbide. Previously only used in manufacturing via other technologies, the material features a tough cobalt and tungsten carbide matrix structure, giving it the durability needed to print parts for demanding industrial applications.
Elsewhere, in the filaments space, materials firm The Virtual Foundry launched a new tungsten-based radiation shielding filament, Rapid 3DShield Tungsten. The material is the densest FFF filament the firm has ever developed, and it’s capable of providing radiation shielding benefits without the need for debinding or sintering.
Subscribe to AM Chronicle Newsletter to stay connected: https://bit.ly/3fBZ1mP
Follow us on LinkedIn: https://bit.ly/3IjhrFq
Visit for more interesting content on additive manufacturing: https://amchronicle.com/