A research team at ETH Zurich displays a decorative new ceiling called the HiRes Concrete Slab, which had been created with a new, energy-saving fabrication method. The prototype occupies ETH Zurich’s NEST Research Building — a so-called living lab which had just been completed this past fall in Dübendorf, Switzerland.
More from the News
The work has been installed within the two-story ‘HiLo unit,’ an office space used by a robotics research group. and showcases the advantages of the technologies — such as 3D-printed formwork — which the team is currently exploring.
THE INNOVATIVE FABRICATION PROCESS OF THE HIRES CONCRETE SLAB
The development of the thin-shell HiRes Concrete Slab involved a collaboration between ETH Zurich’s Digital Building Technologies (DBT) team, its Block Research Group (BRG), and Architecture and Buildings Systems (A/S). The work at once showcases the function and efficiency of the technology and the ‘spectacular aesthetic of free form.’
To make the slab, concrete is poured into 43 thin 3D-printed molds which are held by a laser-cut timber waffle. ‘The 3D-printed parts are only five centimeters in thickness to reduce material and production costs.’ The process further allows for the integration building services including heating, cooling and ventilation during the construction process. Four custom ventilation ducts developed by the A/S team were 3D printed with polymer into the structure before the concrete was poured.
The team comments: ‘This new approach can have a significant positive impact on the built environment: reducing embodied carbon and operational energy, increasing user comfort, and giving architects unprecedented design freedom.‘
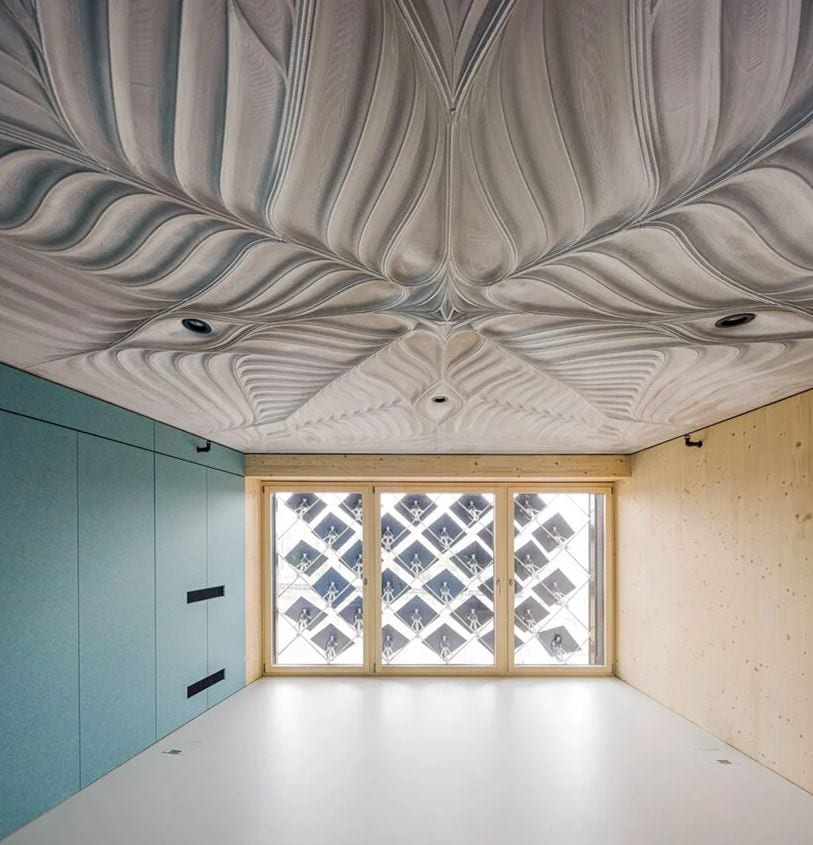
THE PART-TO-WHOLE ASSEMBLAGE
The HiRes Concrete Slab at ETH Zuruch’s NEST research building takes shape as a thin, doubly-curved shell based on the structural concept developed by BRG. The group elaborates: ‘Vertical stiffeners transfer loads to the boundary supports through compression forces only. The forces are concentrated in the corners, where their horizontal thrust is distributed to post-tensioned ties.
‘Thus, material is placed only where it is structurally needed, according to the flow of forces through the shell. This approach results in a 70% reduction of material compared to a standard reinforced concrete slab.’
The slab as a whole is assembled as a collection of parts which easily fit together. The seams between each part are read as the most prominent contours, suggesting the a continuous, uninterrupted surface.
HIGH-RESOLUTION CONCRETE
Along with its aesthetic qualities and ultra-efficient fabrication process, the highly-articulated soffits of the HiRes Concrete Slab enhance the acoustic qualities of the space. The team at ETH Zurich explains: ‘the flowing contours reach their highest density in a central peak and fade out towards the perimeter.’ This decorative pattern is informed strictly by its function, the constraints of the fabrication process, and efficient assemblage and demountability.
Subscribe to AM Chronicle Newsletter to stay connected: https://bit.ly/3fBZ1mP
Follow us on LinkedIn: https://bit.ly/3IjhrFq
Visit for more interesting content on additive manufacturing: https://amchronicle.com/