Eplus3D, as a Chinese leading AM manufacturer, also enters into railway industry with its large-format metal AM machines.
More from the NewsÂ
In the past few years, we have witnessed that 3D printing has been adopted by many different industries, from automobile to aviation industry. Urban transportation indeed benefits a lot from metal 3D printing. Railway is no exception.
The railway sector obviously needs a lot of high-quality parts. The safe and stable operation of a train is inseparable from the long-term maintenance and functionality guarantee the manufacturers of such equipment are in need to provide.When there is a need to replace parts but no replacement parts are in storage, the railway provider needs to contact the manufacturer to provide them quickly. At this time, the management cost as well as cost for spare parts procurement will be relatively high. With the rapid development of 3D printing technology, this technology is applied for assisting in train operation and maintenance, providing customized parts and replacing damaged parts. Compared with the traditional manufacturing processing, 3D printing has a faster response and is more cost-effective.
The speed of high-speed railways can reach 350km/h or higher. Although it’s relatively easy to drive, it’s difficult to stop. The main difficulty is that while braking, each train carriage weighing more than 60 tons will produce huge inertia, which generates huge kinetic energy, resulting into heating up of the brake discs due to friction while braking. As a consequence, the brake pads and brake discs should not only withstand the high temperature around 900 °C, but also ensure its good performance at the same time. It also needs to be able to work normally even in harsh environments such as rain, snow, sand and or dust. In recent years, the R&D and production technology of high-speed railway pads and brake discs. has gradually made breakthroughs. With the in-depth integration of metal 3D printing technology into railway industry, metal 3D manufacturers start to explore the application of metal 3D printing technology for performance improvements of brake pads and brake discs.
Earlier this year, Eplus3D cooperated with a railway company to provide them with a tailored metal AM solution by printing several braking discs with its large-format metal AM machine EP-M650 (quad-laser).
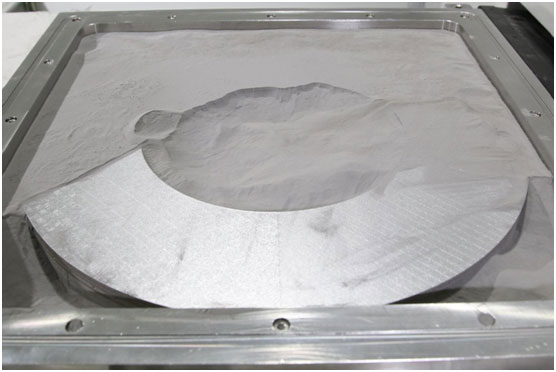
First design of brake disc: this brake disc is printed with Eplus3D metal 3D printer EP-M650 with 24CrNiMo. The part size is Φ648×90mm³ with the layer thickness of 50μm. Printing time: 631h.
The second design of brake disc: also printed by Eplus3D metal 3D printer EP-M650 for railway industry.
Limitations of brake discs with traditional manufacturing
Before 24CrNiMo was used to produce the brake discs, high-speed trains of the early days used composite brakes. Due to its low mechanical strength and poor impact toughness, the composite brake disc used in early high-speed trains is likely to have microcracks during operation. Besides, the brake material is sensitive to water. When the train is moving in the rainy season and wet areas, the moisture of the brake leads to less friction of the material, thus the braking performance will be weakened.
In the traditional manufacturing process, the brake pads and brake discs are created by powder metallurgy. In the sintering process, due to the different shrinkage coefficients of each component in the brake disc, it is likely to produce defects such as porosity and coarseness, resulting in low compactness of the brake disc, which affects its final mechanical properties and friction properties.
The traditional manufacturing of brake discs mostly adopts the “reduced material” manufacturing method combined with casting and forging, which will bring with cumbersome process, low material utilization rate and long production cycle.
How to optimize the brake discs with Eplus3Dmetal AM solutions?
Printing Material
After data analysis and survey, 24CrNiMo was selected as printing material.24CrNiMo steel is one of the high strength low alloy steels with excellent mechanical properties. It has high ultimate tensile strength, good fracture toughness and thermal stability and is widely used in the manufacture of high-speed railway brake discs. Brake pads and brake discs are the key parts in the braking device of high-speed train set. Parts printed with this material can effectively reduce its weight and improve the mechanical properties of the brake disc.
Metal Additive Manufacturing Machine
After design and material selection, Quad Laser Large Format metal 3d printer EP-M650 is selected for this project, with the building volume of 655x655x800mm³. Together with high beam quality and a detailed resolution, the forming accuracy and mechanical properties of the brake disc can be guaranteed.
Additive Manufacturing
Using metal 3d printer, Eplus3D is able to avoid material waste, shorten production time and product cost, giving full play to the advantages of metal 3D printing. The design of the surface hole in particular, different from the traditional manufacturing processing of casting and forging, 3D printing can directly print it through the model design, and fully improve the heat dissipation of the brake disc.
Advantages of applying Eplus3D metal printing parts to trains
- Improve the performance of brake discs.
The 3D printing technology directly prints the wear-resistant layer on the steel back surface. The high-energy laser beam used in the 3D printing process can fully react and highly densify the components in the brake disc, so that the obtained brake disc has better mechanical and friction properties.
- Lower cost and shorten time.
3D printing can optimize spare parts at lower cost and in a shorter time, so as to achieve a longer life cycle. In the past, one-time custom parts manufacturing was very expensive, because it is almost impossible to produce only one part at a time and manufacturers usually make a large number of parts at the same time, which will cause a waste of materials and property with the production cycle generally taking about two months. Now with Eplus3D metal additive manufacturing solutions for railway, the time can be effectively saved.
- Accelerate operation.
By using 3D printing technology to produce spare parts, trains can be started and operated faster, and the inventory of spare parts that lead to material waste can be reduced. With the development of science and technology, it can be expected that 3D printing will play a wider role in the railway field.
Subscribe to AM Chronicle Newsletter to stay connected:Â Â https://bit.ly/3fBZ1mPÂ
Follow us on LinkedIn:Â https://bit.ly/3IjhrFqÂ
Visit for more interesting content on additive manufacturing:Â https://amchronicle.com/
Company Press Release