CA Models, a specialist in high-quality, fast-turnaround metal and plastic additive manufacturing, is using new investment in two wire-erosion machines from Sodi-Tech EDM to optimise the process of removing 3D-printed parts from their build platforms.
Established in 1983, Stirling-based CA Models has been setting the standard for excellence in rapid prototyping for decades. Providing a varied, extensive and streamlined service to meet the challenges and demands of a growing market, CA Models has five different additive manufacturing departments, including metal laser sintering. This process allows components to be 3D printed from powdered metal that includes aluminium, titanium and steel. The 35-employee company can provide printing, finishing and optional post-machining, all in-house.
“We had two Sodick wire EDM machines that were still running well but getting on in years,” explains founder and Managing Director Clark Campbell. “I felt it was the right time to bring in some new technology for the next decade. The new Sodick machines are even more accurate and faster. At CA Models we are in the ‘quick’ business, where just about every client wants their parts yesterday. That’s why we need an in-house resource when it comes to wire erosion. Every time we have a really complex, accurate part to produce, the clock is ticking.”
With two Sodick machines already in-situ and proving their worth over many years, the company had no hesitation in returning to Sodi-Tech EDM for its new investment. “I think Sodick technology is brilliant and the reliability of the machines warrants some loyalty in my opinion,” says Mr Campbell. “I went to an open day at Sodi-Tech EDM’s Warwick facility and was really impressed with the latest machines, which will play their part in a big way over the coming years.”
Installed in September 2022, the new Sodick ALC600G and ALC800G wire EDM machines are already busy.
“For example, take a titanium build platform with 14 motorsport parts on the base,” says Mr Campbell. “When the printing process is complete, the entire platform goes into our furnace for heat treatment for 24 hours, after which we wire-off all the components from base plate using our Sodick technology. As the wire cuts so finely we do not lose any dimensional accuracy in the parts. Furthermore, the machines wire so quickly that we get a head start in finishing the components. Although this process is the underlying reason behind our investment, we also get many subcontract CNC machining projects, some of which lend themselves to wire EDM. It’s great to have that flexibility, particularly for complex, intricate parts required by sectors such as Formula One.”
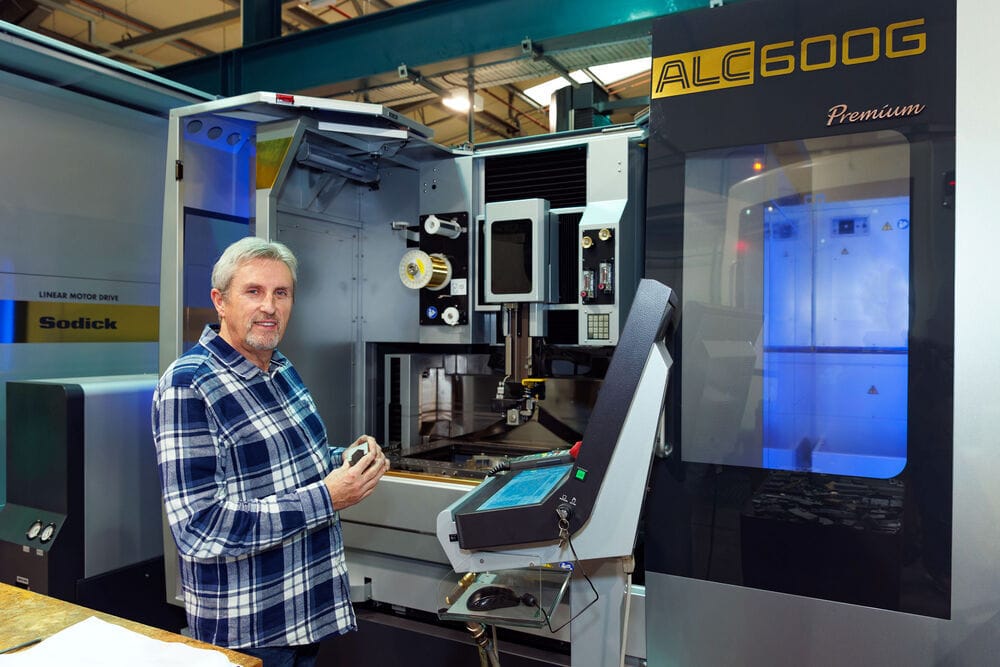
(Source: Mark Ferguson)
The ALC600G is a rigid linear motor driven wire EDM machine that offers features such as Sodick’s next-generation SPW control with Smart Pulse Generator and other performance boosting technologies. While offering axis travels of 600 x 400 x 350 mm, CA Models thought it prudent to also invest in the larger Sodick ALC800G wire EDM, which provides 800 x 600 x 500 mm (Z-axis option of 800 mm).
“As far as wire EDM is concerned it’s always nice to have a big machine because we sometimes get large or unusual requests,” explains Mr Campbell. “I think we’re the only company in the UK to have the ALC800G model.”
Without the Sodick wire EDMs, CA Models would have to remove additively manufactured parts from base plates using its large bandsaw, which is far from ideal.
“It’s something we’ve done before, but it always feels a little unsafe and not exactly best-practice in my opinion,” states Mr Campbell. “Wire EDM is far more practical, efficient and effective. Furthermore, once finished, the support plate looks brand new and ready to use again, which is really helpful.”
Although CA Models serves clients across a host of industries that include aerospace, defence, medical and energy, among the busiest sectors at present is motorsport, particularly Formula One, where teams are designing and manufacturing parts for next year’s cars.
“I think we could be particularly busy this time around as Formula One currently has one dominant team, so the others are very keen to make up ground,” says Mr Campbell. “We received a nice order last week from a team towards the back of the grid, who should really be towards the front. These are aerodynamic body parts made from aluminium that we will additively manufacture and finish in-house. Undoubtedly, the parts will end up on the Sodick machines for base plate removal. It’s something we’ve come to rely on.”
Subscribe to AM Chronicle Newsletter to stay connected: https://bit.ly/3fBZ1mP
Follow us on LinkedIn: https://bit.ly/3IjhrFq
Visit for more interesting content on additive manufacturing: https://amchronicle.com