A research team led by Dr. Nanjia Zhou at Westlake University and Westlake Institute of Advanced Studies in China have recently introduced a new strategy to enable the 3D printing of soft hydrogel electronics. Their approach, introduced in a paper published in Nature Electronics, could help to lower the production costs of numerous hydrogel-based devices, including strain sensors, inductors, and biological electrodes.
Hydrogels are three-dimensional (3D) polymer networks that do not dissolve in water but retain large amounts of liquids. Due to this advantageous property, hydrogels are particularly promising material platforms for both biomedical and environmental applications, as they can survive in bodily fluids or in wet natural environments without dissipating.
Over the past decade, engineers and materials scientists have been developing numerous electronic devices based on soft hydrogels, including environmental and biomedical sensors, drug delivery devices, and artificial tissue. Despite the huge potential of these hydrogel-based devices, their widespread implementation has so far been hindered by their high production costs.
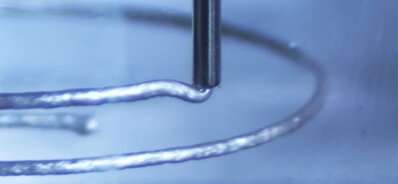
“We choose to study hydrogel production because while most of the current soft electronics are based on flexible elastomers and polymers, undeniably hydrogel is more similar to the human body and may lead to better tissue integration and less immune responses,” Dr. Yue Hui, one of the researchers who carried out the study, told TechXplore. “As suggested by previously studies, we think that hydrogel is a promising candidate for the creation of future health care electronic devices.”
The primarily goal of the recent study by Hui and his colleagues was to devise an efficient strategy to fabricate increasingly complex and biomedically useful hydrogel-based electronics. Their proposed approach is based on 3D printing technology, specifically utilizing a hydrogel-based supporting matrix and a stretchable silver-hydrogel ink.
“The embedded 3D printing method we developed involves the freeform printing of a conductive hydrogel ink into a hydrogel supporting matrix, and the subsequent curing of the two parts to form a soft and stretchable electronic device,” Hui explained. “These are based on the suitable rheological properties of the matrix and the ink, as well as the orthogonal curing mechanism of alginate and polyacrylamide, which are the main components of the hydrogel.”
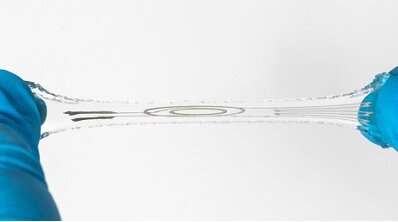
The researchers found that combining a conductive filler (i.e., silver flakes) with granular gel particles led to the formation of a segregated structure in the conductive 3D printing ink. This ink exhibited a remarkable electrical conductivity of over 1,400 S/cm.
To demonstrate the feasibility of their proposed strategy, Hui and his colleagues used it to create a series of hydrogel-based electronics, including strain sensors, inductors and biological electrodes. The resulting devices were found to perform exceptionally well, suggesting that this approach could be used to create a range of new hydrogel-based technologies.
“As we demonstrate in our paper, our method can be used to make various hydrogel electronic devices with different functionalities,” Hui said. “Particularly, we can directly print exposed electrodes that can communicate with the outside world, and we can incorporate components such as LEDs and chips into the circuitry via printing. Our findings imply that with delicate design we can really make functional hydrogel electronic devices.”
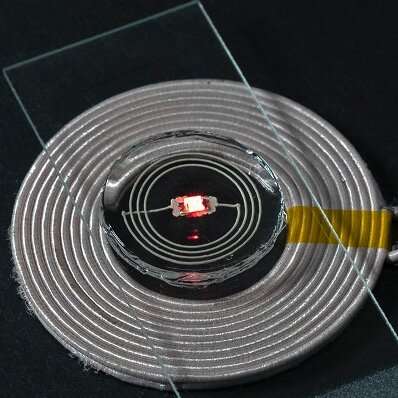
In the future, the recent work by this team of researchers could enable the fabrication of more complex and sophisticated hydrogel-based electronics, including biomedical devices and new technologies to monitor the environment. Hui and his colleagues are now working to improve their 3D printing strategy to further facilitate its real-world and large-scale implementation.
“We will now keep optimizing the materials and methods,” Hui added. “For example, a systematic and theoretical study regarding the conductive ink with segregated structure is still lacking, which may be the key to further improve its conductivity. We also plan to design and fabricate biomedical devices and validate their functionalities in animals.”
Subscribe to AM Chronicle Newsletter to stay connected: https://bit.ly/3fBZ1mP
Follow us on LinkedIn: https://bit.ly/3IjhrFq
Visit for more interesting content on additive manufacturing: https://amchronicle.com