The construction industry, in the past industrial revolution, lags to contribute its significant participation in terms of digital fabrication while comparing with other industries.  However, in industrial revolution 4.0, the trend of the construction industry is now uplifted and actively participated after the implementation of digital fabrication, which enables automation in the field of the construction sector.  Concrete 3D printing has been effectively used digital fabrication technique in construction industry, especially in countries include Netherlands, China, and Switzerland.  The specific design consideration required for digital fabrication is generally called Design for Digital fabrication (DF2) to enhance the structural integrity and sustainability.  DF2 is a well-planned framework with the contemplation of manufacturability, structural stability, aesthetics, economical, and eco-friendly. All these elements can be efficiently executed by topology optimization.  Topology optimization (TO) has been extensively used in many industries including automotive, aerospace, medical and civil engineering to enhance the performance and manufacturability of lightweight structural components.  Moreover, Topology optimization is used in Architectural, Engineering and Construction (AEC) industries in the later 80’s since the rate of social acceptance in AEC industries is comparatively low.  However, in past decades, topology optimization is not efficiently utilized in construction industries due to high fabrication costs and the complexity of the optimized shape.
Moreover, the fabrication cost of the optimised structure is very expensive in the conventional fabrication methods. Â Due to complexity, the labour cost and traditional formwork material is more than sixty percent of the total fabrication cost of the optimized structure. Â Shape optimization is carried out with manufacturability constraints to reduce the complexity of the optimized shape, which may affect the optimality of the structure. Therefore, topology optimizations in construction industry cannot be economically implemented while adopting the conventional fabrication method due to its formwork costs, even though it reduces material costs and consumes more time and workforce. Â However, the Digital fabrication technique changes the scenario and enables the fabrication of complex shapes with minimum time and limited workforce.
DF2Â Considerations
During the design of digital fabrications, the key factors to be considered are given below.
- Material Considerations
- Anisotropic behaviour
- Rheological behaviour
- Rate of hydration
- Geometric Considerations
- Minimum cross-section
- Self-Supporting
- Overhanging angle
- Fabrication Considerations
- Layer thickness
- Orientation of printing
- Rate of printing
How the Topology Optimization Evolved in the Construction Industry?
Prior to the adaptation of digital fabrication, the topology optimizations are used with excess post-processing in the construction industry. The topology optimizations are used to optimise the shape of grid slabs in the early 80’s with costlier traditional formwork.  After the evolution of digital fabrication, topology optimisation has been successfully adopted by many engineers and architects. Several 3D concrete printed buildings are produced in several countries include Netherlands, Switzerland, Germany, China, Dubai and Africa. The first concrete 3D printed bridge for cyclists in Netherlands has been made and opened for the public in 2017. In 2019, the DFAB houses were fabricated using different digital fabrication techniques include smart dynamic casting and mesh moulding. The world largest Concrete 3D printed pedestrian bridge is fabricated in Shanghai, China, in 2019 (see Figure 1).  The length of the concrete 3D printed bridge is 26.3m long and 3.6m in width. Similarly, the concrete 3D printed pedestrian bridge of 29m long is fabricated in Nijmegen, Netherlands, in 2021.  The 12m long pedestrian 3D printed metal bridge is printed and examined with several tests to ensure structural stability.  The printed bridge passed all tests, and it was opened to the public in the city centre of Amsterdam, Netherlands.  The materials used for digital fabrication such as concrete, steel, polymers and clay.
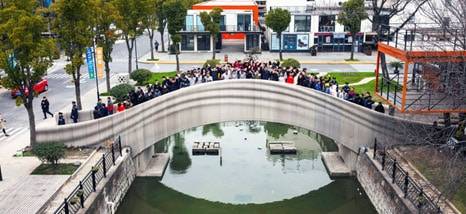
(Source: https://www.rdworldonline.com/the-worlds-largest-concrete-3d-printed-pedestrian-bridge/)
Steps for Topology Optimization
Topology optimization is a mathematical framework to optimize the material layout in a given design domain by considering the loads and support conditions and other constraints to minimize or maximize the objective. Â The objective might be maximizing the stiffness of the structure or minimizing the weight of the structures. Â The steps required for topology optimization are designing a 3D model using finite element software, assigning material properties and defining the loading cases and boundary conditions. Â The global objectives (i.e. stiffness and target body) and constraints (i.e. symmetrical plane and volume fraction) are described in the optimization criteria and subsequently run the program to obtain an optimized topology structure. Â The post-processing is carried out to ensure the manufacturability of selected fabrication methods. The conventional casting method needs excess post-process, which might affect the optimality of the structure. Â The digital fabrication technique can be adopted without an excess of post-processing in two ways, by fabricating formwork and fabricate using the shell and fill method or fully 3D printed structure. The detailed steps in making the hammerhead pier beam are illustrated in Figure 2.
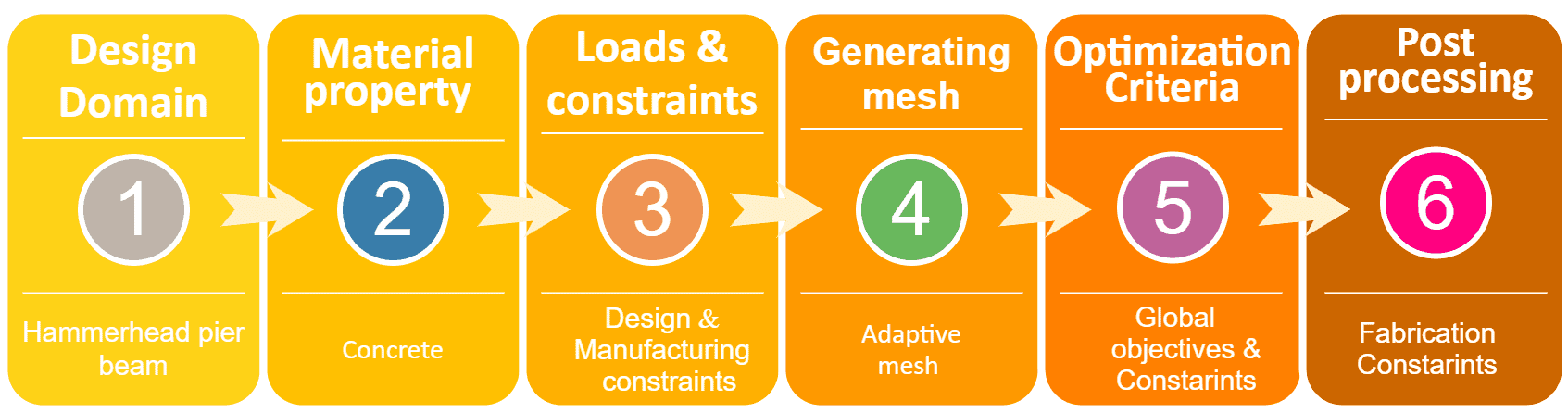
Topology Optimization for Conventional Casting Method
The Topology optimization is carried out over a hammerhead pier beam to reduce the structure’s weight without affecting the structural efficiency. Â Moreover, it is carried out by considering the manufacturing constraints of the conventional casting method and the limitation of complex shapes. Â As a result, thirty percentage of the structure’s weight is reduced, as shown in Figure 3. Â However, the fabrication cost of conventional formwork for topology optimized hammerhead pier beam is high due to its complexity. Â Furthermore, the fabrication of a topology optimized hammerhead beam requires three times more workforce and time. Hence, the rate of social acceptance of topology optimization is low in the ACE industries.
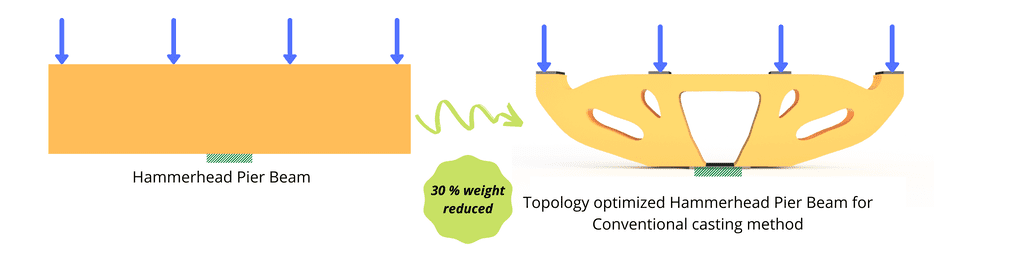
Topology Optimization for Digital Fabrication
The topology optimized hammerhead pier beam can be fabricated using the Digital fabrication technique.  Digital fabrication extends the boundary by reducing manufacturing limitations while manufacturing complex shapes.  The fifty percentage of weight is reduced, as shown in Figure 4.  However, the design for digital fabrication is twenty percentage lightweight as compared with the conventional casting method.  The fabrication part is fully automated.  Therefore, the workforce and fabrication time is reduced. The main advantage of digital fabrication is the elimination of conventional formwork.  As a result, there is no need to spend the higher cost for creating the formwork for complex shapes.  The strength to weight ratio is comparatively higher and maximum deflection is minimized after the adoption of digital fabrication. Concrete 3D printing and other digital fabrication methods are economical for topology optimized structures.
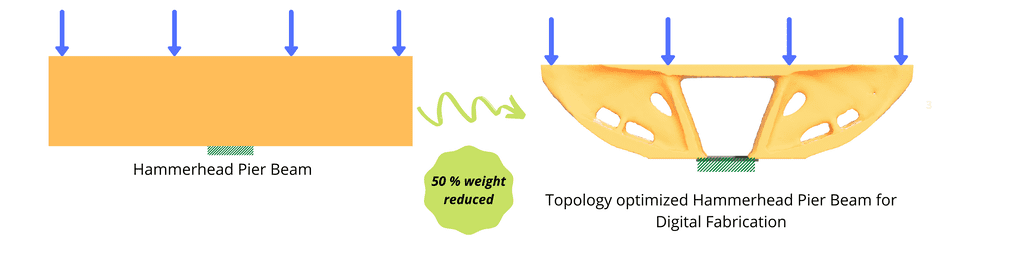
“3D printing eliminates the conventional formwork for the fabrication of concrete structures.”
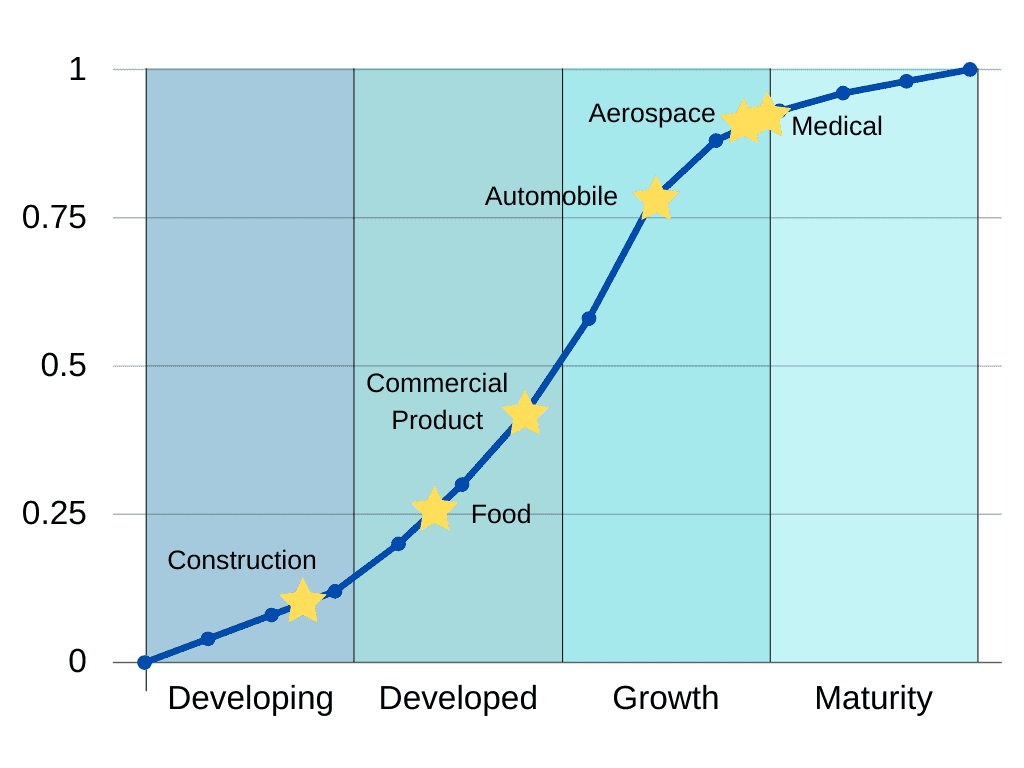
Future of Digital Fabrication
The impact of digital fabrication offers a wide range of mass customization and fabrication of tailored design with a minimum carbon footprint, ensuring ubiquitous and proliferation growth to make a more sustainable future. Â Digital fabrication, in construction industries, is now at the developing stage, while all other industries are ahead as illustrated in Figure 5. Numerous researchers have been conducting their investigations in the field of Concrete 3D printing, Smart dynamic casting, sub-millimetre formwork (eggshell), binder jet, selective paste intrusion, mesh moulding and other techniques. Â The standards and building codes are need to be developed to ensure the stability and safety of 3D printed and other digital fabricated structures. Â Concrete 3D printing is beneficial during a pandemic situation for the rapid fabrication for isolation and hospitalization. Â The rate of growth and adaptation is increasing in the past few years, many start-ups, industrialists, and researchers are giving their part in it. Â By incorporating topology optimization and digital fabrication helps to change the quote, “concrete is the second most widely used material in the world” in the future by reducing material utilization. Â The sustainability of construction can be ensured using minimum consumption of concrete and reducing carbon footprint.