Exploring the full potential of Additive Manufacturing in Tooling at STEPL
Sridevi Tool Engineers have always been at the technology adoption forefront and we keep looking for innovative technologies in the modern tool-making world. Realising that the Metal Additive Manufacturing technology has fairly settled down to give reliable results, we embarked on our first project to build an Additively Manufactured insert with inbuilt conformal cooling channels and reaping benefits of having a well cooled core and thereby reduced cycle times for part production and enhanced part quality.
Impeller Fan, this was one part where we knew right from the beginning that cooling the core with the conventional methods was not going to be effective. It needed to be cooled with the 3D printed way and today, in spite of all the teething challenges, we are happy that it was a job well done by the team and it opened up the opportunity for further mold inserts and doors to the immense scope that AM offers to the Tooling Industry.
An invitation to present the use of this technology at Indian 3D Printing Network’s expo last year in Mumbai was the high point for us in this journey.
Here is a synopsis of the discussion and would find common ground with our friends from the tooling industry. There are primarily four listed advantages of AM for Tooling Industry that are being explored, Conformal Cooling systems, Combining Multiple Process Operations, Tool Repair and use of Hybrid printing.
The use of topology based optimization and printing with lattice structures of the whole mold or local inserts have been done in the West for small parts but it is not yet mainstream industrialized.
Combining Multiple Operations– All the processes right from Procurement of Steel to Pre Milling – Sizing – Grinding – Cnc Milling – Roughing – Cooling lines can be skipped if AM technology is used.
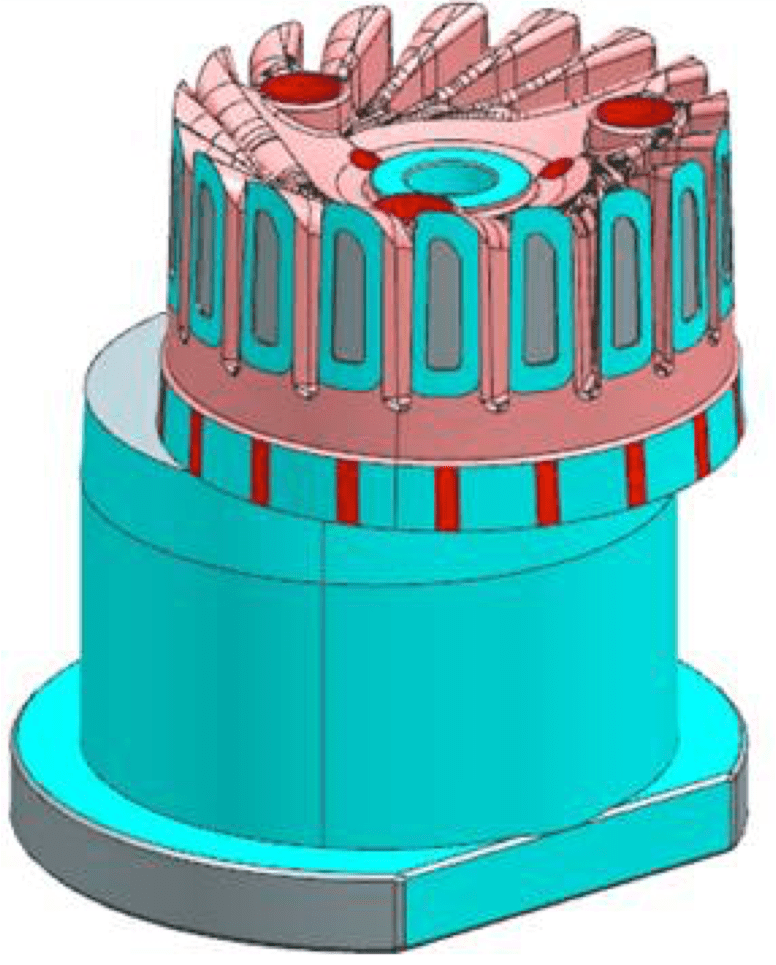
Hybrid Construction– In this the Base of H-13 is conventionally made and printing of Maraging is carried out on top of the flat base and then the whole insert is finally heat treated again in assembly.
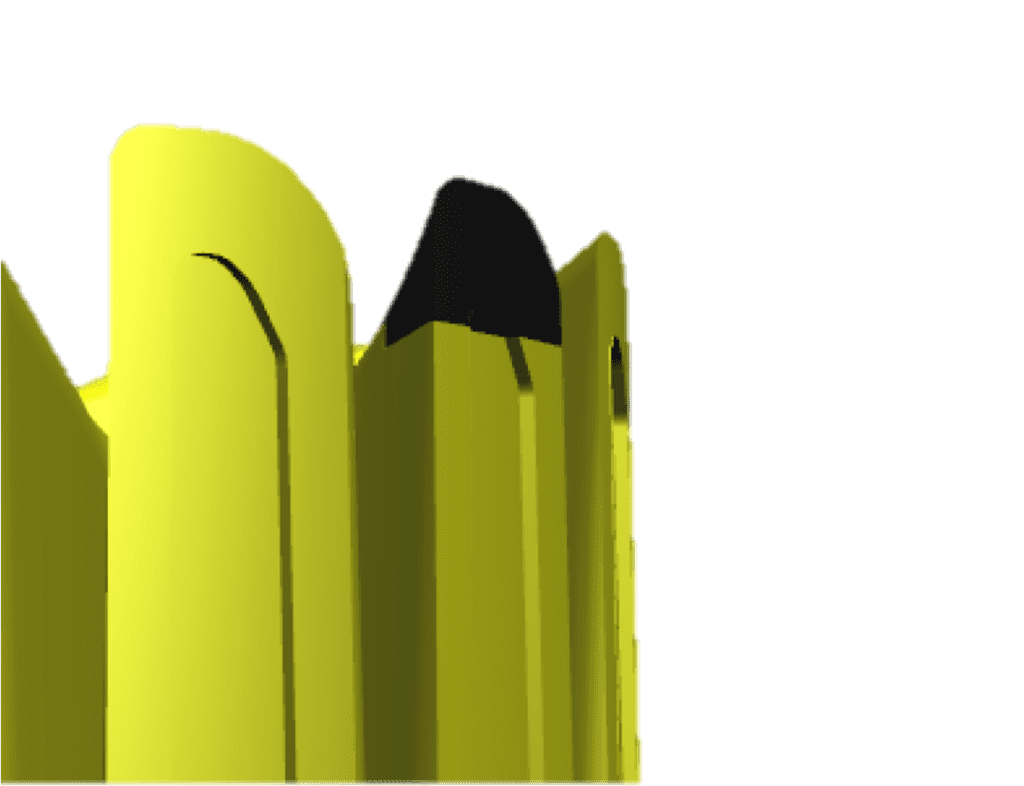
Tool repair – For locally chipped areas, 3D printing on top of local damage areas is a good option to the toolmaker as it offers the same strength with minimal heat and least amount of post processing machining.
We are now technology ready. Each job gave its own learnings and slowly & steadily, we are climbing up the learning curve by building Plastic and Mold design guidelines for AM and devising Design Best practices on the go.
Mr. Akshay Kalyanpur, MD, STEPL adds “The AM technology thrust has to come from the OEM and TIER 1 end users, who inturn will be the real beneficiaries, this will offset the initial high tooling cost of the mold due to AM”