Metal Additive Manufacutring is quickly gaining popularity in India since it brings together the design flexibility of 3D printing and the mechanical properties of high-performance metal alloys. This makes it an ideal way to create lightweight, strong, and unique parts for various applications. Laser powder bed fusion (PBF) and metal binder jetting are two popular processes used for metal 3D printing.
Laser powder bed fusion (PBF) is a type of additive manufacturing (AM) where a laser is used as a heat source to consolidate material in powder form to form three-dimensional (3D) objects. On the other hand, in an industrial printhead deposits a liquid binding agent onto a thin layer of powder particles.
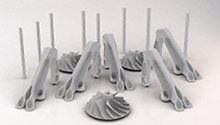
The biggest challenge in designing for additive manufacturing is finding the balance between optimal design, cost, and AM process feasibility. The design needs to consider the interdependence between part design and build strategy, including factors such as component geometry, orientation, as well as support location, type, and density. Design for Additive Manufacturing (DfAM) also leverages “rules” and experience with lots of trial and error. Software tools can help achieve the required time, cost, and quality.
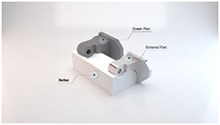
In metal binder jetting, the sintering process or the thermal process of converting loose fine particles into a solid, coherent mass is prone to distortion. Therefore, designing a sintering cycle using simulation can help avoid the number of trials, and this saves time, cost, and resources.
Simulation can be used end-to-end across the additive manufacturing workflow to ensure that a part is printed right the first time.

Even before we jump into the actual process of 3D printing, we must start with design optimisation and light weighting. This includes not just structural optimisation but optimising parameters such as minimum angle thickness and overhang, which are critical for 3D printing.
During the manufacturing stage, software tools can help predict the best orientation support structure to eliminate any failures and ensure print quality. There are several variables that affect print quality. We can perform sensitivity analysis to determine which variable has the highest influence.
Hexagon has several versatile solutions for use in many different cases for additive manufacturing. These include MSC Apex Generative Design, Simufact Additive (AM with metals), Digimat AM, and Nexus AM
There are several tools available for optimisation of additive manufacturing. These include options for geometry import, intelligent smoothing, design, geometry export, manufacturing validation, and design validation. Tools such as Simufact Additive can help assess parameters such as part printability, manufacturing risk, process optimisation, and perform post-build operations. Hexagon is also designing a single GUI to integrate all stages of the additive manufacturing process by combining AI/ML tools with AM simulation tools.
At the input stage of the AM process, one can determine the most optimal orientation, support structure, number of parts, laser power, scan speed, layer thickness, and material type. At the output stage, tools can help determine distortion, peak temperature, residual stress, cost per part, recoater interference, and manufacturing risk.
This, in turn, can help streamline the process by reducing the number of runs for optimisation and enabling sensitivity analysis. ML also informs new additive designs and processes. It enables the selection of the best orientation and process parameters.
Take the example of building a Schubert gripper with an end-to-end workflow. The use of MSC Apex for generative design will be followed by performance analysis with MSC Nastran and process simulation using Digimat. Similarly, tools from Hexagon can assist with print job preparation, MES/production and data acquisition (optical/CMM/CT), data clean up, quality inspection, and model reconstruction (surface/solid/CAD). This can be followed by defects analysis, FEA analysis (effect of defects), machining toolpath generation and machining simulation.
To know more about how Hexagon can facilitate a truly optimised and intelligent additive manufacturing process, read this whitepaper on additive manufacturing or visit the website of Hexagon.
Subscribe to AM Chronicle Newsletter to stay connected: https://bit.ly/3fBZ1mP
Follow us on LinkedIn: https://bit.ly/3IjhrFq
Visit for more interesting content on additive manufacturing: https://amchronicle.com