A catalyst is a substance that increases the speed of a chemical reaction without itself being part of the reaction. Shell is a leader in developing catalysts for the energy industry and improving their performance to make petrochemical processes better. 3D printing empower us to innovate catalysts even further.
3D printing technology, also known as additive manufacturing, was introduced in Shell research centre in Amsterdam more than 10 years ago. Our printing capabilities expanded so that today we can print metal, polymer, and ceramic materials. We have proven the value of this technology for the energy sector by producing dedicated R&D equipment and helping pave the way for a digital inventory of industrial spare parts. However, these significant achievements all refer to dense parts. For 3D printing of catalysts, a technology breakthrough was needed to produce unique porous structures.
Overcoming Impossible catalyst designs
3D printing of catalysts is an attractive opportunity because traditional catalyst manufacturing processes like extrusion and pelletizing offer limited options for shape and form of the catalyst. 3D printing help overcome these limitations to improve the desired properties of the final product such as catalyst activity and selectivity.
The requirements for efficient and high-performance catalysts extend beyond their macroscopic shape and form. Microscopic pores hidden inside a catalyst pellet are just as important as they provide high surface area essential in a catalytic reaction. With 3D printing, we can improve both macro- and microscopic designs of our catalysts.
Collaborating with 3D printing technology partners outside Shell
To meet our catalyst requirements, we worked together with 3D printing solution providers specialised in printing porous ceramic materials. Together, we prepared catalyst prototypes for our gas-to-liquids (GTL) technology and for environmental catalysis.
Joining Shell’s unique expertise in catalyst structures, form and post processing techniques with the printer’s domain expertise in porous ceramic materials, we proved the potential for 3D printing to enhance catalyst performance. This recent achievement from our laboratories at the Energy Transition Centre Amsterdam paves the way to further maturing 3D printing technology for catalyst productions.
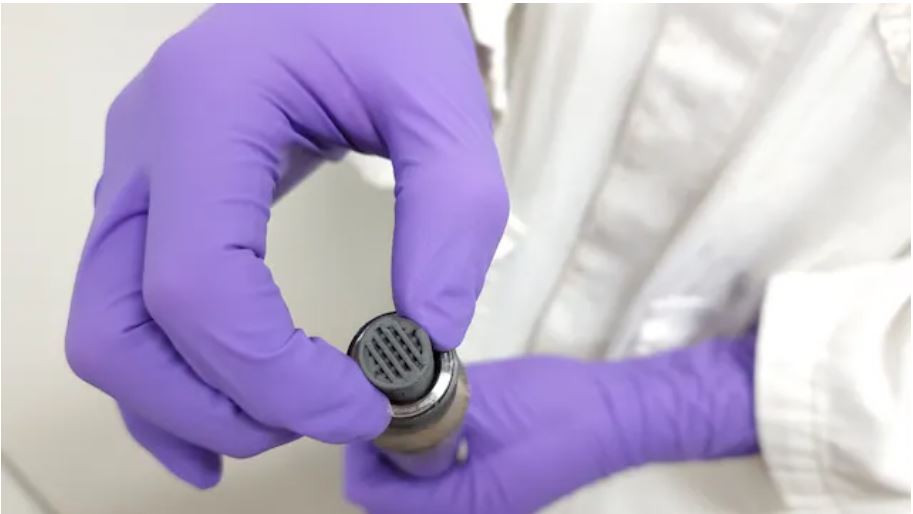
“3D printing is a key enabler to develop advanced catalytic materials which are crucial for the energy transition. This rapidly evolving field offers a myriad of opportunities to improve mass and/or heat transfers with better catalytic performance.”
Ed Ganja, Vice President for Catalyst and Analytical Technology, Shell
Speeding up early-stage catalyst R&D
The future of 3D printing catalysts still has many opportunities and challenges. For example, we believe rapid catalyst prototyping via 3D printing will speed up the early stage of catalyst R&D considerably. The field of 3D printing technology is still advancing rapidly and commercial manufacturing platforms for 3D printed catalyst lie ahead.
When deployed, the benefits of 3D printing catalysts could include:
- faster production;
- improved raw material efficiency;
- close-to unlimited shapes and designs; and
- better performing catalysts for our customers.
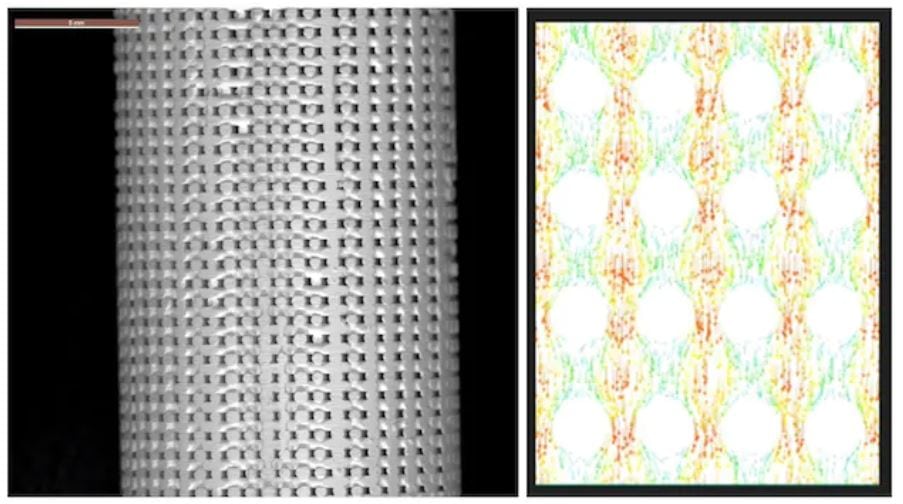
We remain committed to address the evolving catalyst needs of our customers, both in our traditional areas such as ethylene oxide and hydroprocessing as well as in emerging areas related to the energy transition. 3D printing can help us accelerate innovation in catalysts products toenable chemical reactions previously deemed too challenging.
Subscribe to AM Chronicle Newsletter to stay connected: https://bit.ly/3fBZ1mP
Follow us on LinkedIn: https://bit.ly/3IjhrFq
Visit for more interesting content on additive manufacturing: https://amchronicle.com