As metal additive manufacturers scale AM operations to meet growing demand, they are keen to scrutinize choices made before and during the additive process, such as topology optimization, material choice, powder sizes and layer line thickness, all to optimize production-scale AM. However, manufacturers often overlook the importance of postprocessing for achieving end part requirements.
The benefits of additive manufacturing have facilitated new growth and innovation in key industries–notably the medical device, aerospace and energy industries–to produce high-quality, metal-AM components from turbine vanes in commercial aircraft engines to titanium cages replacing vertebrae in spinal fusion surgery. Manufacturers are keen to capitalize on AM’s growing list of benefits, including its ability to mitigate supply chain disruptions by localizing manufacturing, enhancing rapid-prototyping and reducing lead times with faster design iteration and near-net shape manufacturing, as well as significantly reducing material waste—all of which provide myriad economic and ecologic benefits.
However, as this article will discuss, these benefits are undermined when manufacturers overlook the importance of postprocessing by using costly, prolonged and outdated methods during the final steps of a part’s production.
Engineers are continually working to mitigate the disadvantages of AM by improving the resolution, affordability, and processing speed for metal additive manufacturing. However, AM’s processing speed for production environments has been a persistent disadvantage of most AM methods. Fortunately, additive manufacturers are increasingly keen to the revenue potential of AM volume production applications, especially where per-part costs are critical, and are beginning to make significant advancements towards efficient, high-volume AM. Large-format additive manufacturing (LFAM) is being increasingly utilized not only for its ability to produce large individual additive components, but for machining an array of smaller components in a single build as well.
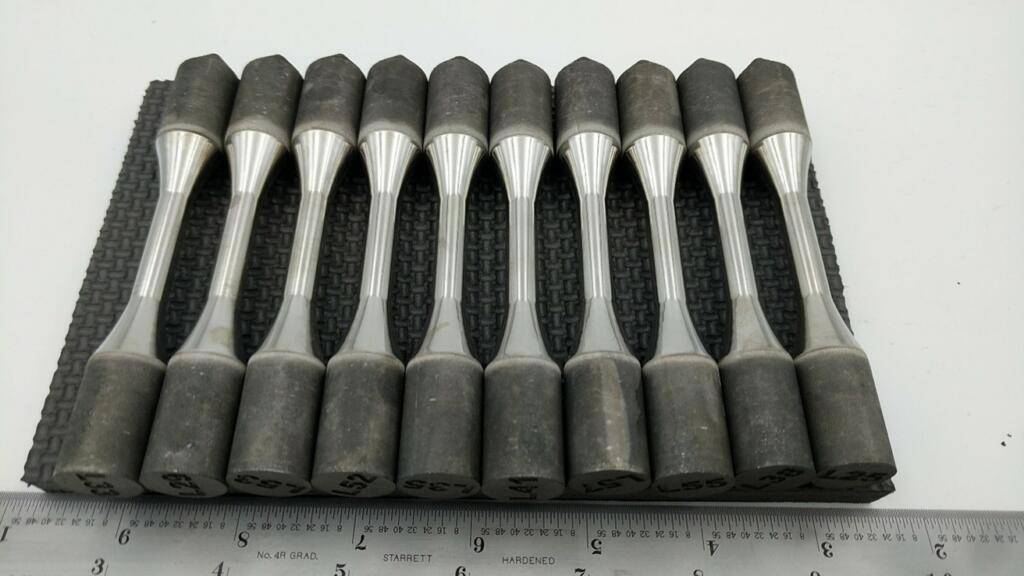
In addition, industry experts speculate the growth of artificial intelligence (AI) can play a part in improving the design and manufacturing processes in AM in tandem with other advancements to facilitate more efficient volume production. For instance, AI can enhance topology optimization, simulate multi-physics models for critical parts, and can possibly be used to generate new designs altogether. Additionally, AI can be used to look at previous feedback to adjust parameters in the AM process itself (such as powder size, layer line thickness or scanning strategies) to produce higher quantities of parts with improved efficiency.
This shift towards higher-volume production is substantial–according to Protolabs data, the number of surveyed additive manufacturers printing more than ten parts in a single production run grew exponentially from about one-third in 2020, to over two-thirds by 2023. While much of this growth is attributed to plastics, advancements in DED and PBF technology have allowed metal additive manufacturers to optimize their processes and lower costs as they increase volumes to production scale. Additive manufacturers are often taking this a step further by reducing costs via faster laser scan strategies, using larger powders and using thicker layer lines.
However, these decisions often come at the detriment of resolution, feature size and surface quality, thereby requiring more time and effort concentrated to the secondary machining, postprocessing and finishing. Yet, many additive manufacturers continue to employ inefficient secondary machining or finishing processes that can not only damage the components via finishing process forces or thermal distortion, but require constant tool replacement costs that can hinder throughput and raise overall costs. As additive technology continues to grow in critical industries, the issue of surface quality grows in importance.
In many environments, superfinished surface quality is crucial– within aerospace and energy applications, surface quality can govern a part’s strength, fatigue performance, corrosion resistance, and temperature-flux resistance. Within medical applications (notably orthopedic solutions), surface quality is directly correlated with joint mobility, sterilization and the osseointegrative capabilities of some implants (more specifically, which areas of the implant should and should not fuse with the patient’s bone).
Certain PBF methods (such as Direct metal Laser Melting, or DMLM) are often employed while manufacturing complex-geometry, high-volume AM components, leading to two distinct surface quality challenges requiring additional resources for postprocessing: support structure remnants and downskin surfaces.
One issue arising from the use of certain PBF methods occurs when support structures (needed for increasingly complexifying geometries with overhang features) must be removed, creating support structure remnants which must be removed via conventional or non-conventional postprocessing methods. Additional surface quality issues are found in similar ‘overhung’ areas known as downskin surfaces, as with most AM methods, surface quality decreases with certain non-line-of-sight geometries of a part. Increasing stringency on part performance makes this issue worse as manufacturers seek to find a material removal method capable of enabling “homogenous material removal with an effective line-of-sight.”
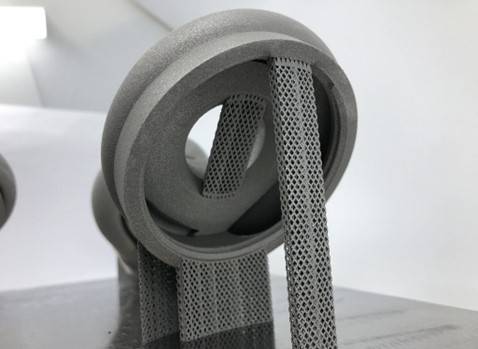
While optimizing designs or choosing new materials may alleviate some of these challenges, many additive manufacturers would benefit from advanced postprocessing technologies, which may not only help manufacturers enable new designs, new material usage and enhance part resolutions but simultaneously allow manufacturers to continue to employ expense-reduction strategies like using thicker layer lines and bigger powders. One technology in particular can take these qualities a step further and enable these advantages in production-scale AM environments—this technology is called pulsed electrochemical machining (PECM).
PECM
Pulsed electrochemical machining is a non-contact, non-thermal material removal method that utilizes electrochemistry–rather than heat or friction–to machine the workpiece material by dissolving it with extreme precision, atom-by-atom, lending it distinct advantages over conventional methods. While PECM is used primarily as a replacement for conventional manufacturing methods for high-volume manufacturing, as it uses a custom cathode (tool) it can also be employed as a postprocessing method for additive parts.
The lack of contact or heat in the PECM process allows it to machine and finish delicate features and complex geometries found in critical AM applications. For instance, consider the critical features, materials and tolerances required for an additively-manufactured turbine vane within an aircraft engine. High temperature-flux resistant materials like Inconel are needed for these environments, and thin features on the blades can facilitate optimal airflow.
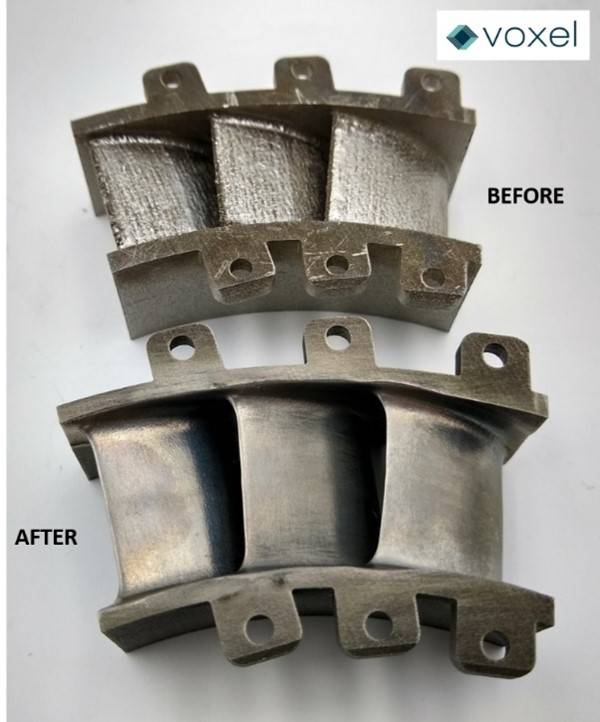
Postprocessing this component conventionally can be risky, as the thin walls can be sensitive to tool vibration and thermal distortion posed by conventional processes (such as CNC or even EDM). PECM, however, has demonstrated the formation of <0.075mm wall thickness without coming into contact with the material.
Another advantage is the process’s indifference towards material hardness; PECM is capable of postprocessing additive Inconel 718 at a similar rate to copper.
PECM’s ability to postprocess complex geometries can also enhance current designs by removing other surface irregularities with superfinished surface finishing. Consider, for instance, the aforementioned surface irregularities found in processes like DMLM like support structure remnants and low-resolution downskin surfaces. PECM can machine these complex surfaces, including certain non-line-of-sight geometries, with high repeatability and without incurring a recast layer, allowing manufacturers to continue employing these methods.
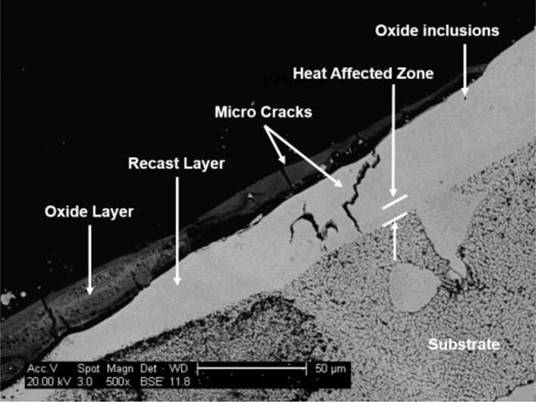
Data from Voxel Innovations has shown that PECM can improve the surface quality of metal AM parts from 5-10um (196-393uin) Ra down to less than 0.5um (19.6uin), Ra, and has even brought surface quality down to 0.1um (3.9uin) Ra.
These surface finishing capabilities are inherent to the process, meaning PECM can act as both a secondary machining process and a finishing process simultaneously, reducing the steps necessary to produce a finished additive component.
Summarized, rather than treating postprocessing as an afterthought, additive manufacturers can enable new ideas before, during and after the additive process itself with the right postprocessing technology:
- Advanced postprocessing can provide manufacturers additional agency before the process even begins— advanced, AI-driven part designs can be enabled that may include otherwise tough-to-machine aspects such as downskin surfaces and internal features. Manufacturers can also choose to utilize a broader range of materials that may otherwise pose challenges for conventional heat-based and contact-based postprocessing techniques like CNC or EDM (such as tool vibration, thermal distortion, burrs or recast layers) without concern.
- During the additive process itself, manufacturers choosing an advanced postprocessing method like PECM can employ strategies geared towards high-volume production, including the use of larger powders and faster laser scanning strategies. With the right postprocessing methodology, lower-resolution AM strategies don’t necessarily inhibit the final component’s tolerances.
Kirk Gino Abolafia is the technical marketing and sales manager for Voxel Innovations, an advanced manufacturing company specializing in pulsed electrochemical machining (PECM) who has written for a variety of technical publications including Additive Manufacturing, Surgical Robotics Technology and Aero-mag. Voxel has recently relocated their operations to a larger facility, increasing their bandwidth for critical, high-volume manufacturing. To learn more about PECM’s applications, visit their site.