John Deere, one of the global agricultural machinery manufacturers, has used metal additive manufacturing to produce stainless steel valve for the tractor’s fuel system. According to the company, the 3D printed value is 50% cheaper and uses less materials when compared with conventional manufacturing systems. The part is one of the first parts launched under the long-term manufacturing strategy of John Deere.
The 3D-printed steel valve will be used in the latest versions of John Deere 6R and 6M tractors as a result of 2 years of research and development effort by John Deere. Udo Scheff, engineering director for John Deere’s small and midsize tractors, stated that the product development process started with computational fluid dynamic analysis followed by prototyping. Additionally, metal additive manufacturing resulted in rounded parts with smooth internal channels. This was not possible by conventional manufacturing because, at the area of the intersection of two drill holes result in sharp edges, which reduces the efficiency.
John Deere manufactured the part with the partnership of GKN Additive. GKN Additive used a binder jetting process of metal additive manufacturing, and HP’s Metal Jet S100 machine was for prototyping. The research team at John Deere selected the binder jetting process because it is faster and more reliable than other metal AM processes.
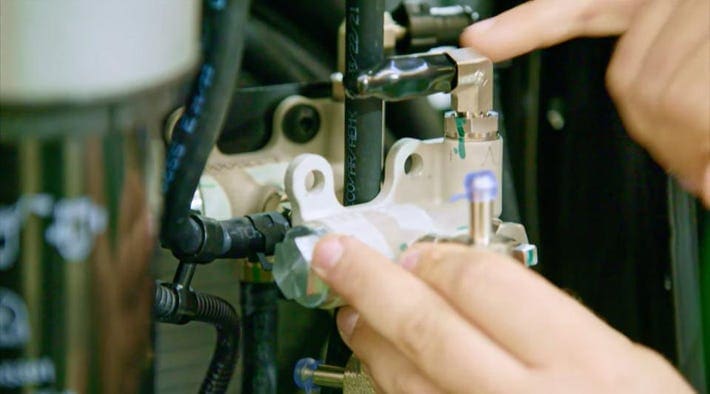
The part went through rigorous testing before the application in the 6R and 6M tractors. The testing was done to compare the performance of the metal AM-manufactured part with the part produced by conventional manufacturing. Field testing was also one of the critical phases of the testing process. It is interesting to note that the part passed all the required tests and fitted in the assembly workflow.
More than 4,000 valves are being transported from GKN to the John Deere tractor factory for assembly. The cost of production of the valve using metal additive manufacturing is less than the conventional manufacturing process.
John Deere plans to use metal additive manufacturing technology for spare parts management. The company is currently looking at parts in their warehouse which can be converted into digital models and printed on demand using metal additive manufacturing. Additionally, they plan to use the technology to repair worn-out parts to meet future needs.
The company has been using metal additive manufacturing to produce jigs and fixtures at all most all the factory outlets. The key reasons for using additive manufacturing for jigs and institutions are the cost economics and the reduction in the time for production. The additive manufacturing technology helps to serve the 24/7 demand for jigs and fixtures from the various facilities of John Deere.
The stainless steel valve is the first part that John Deere is manufacturing using the metal additive manufacturing process, and we will see more details and applications in the coming future. For the metal additive manufacturing industry, the application helps to understand the use of technology to overcome various challenges.
References:
https://www.deere.com/en/index.html
Subscribe to AM Chronicle Newsletter to stay connected:Â Â https://bit.ly/3fBZ1mPÂ
Follow us on LinkedIn:Â https://bit.ly/3IjhrFqÂ
Visit for more interesting content on additive manufacturing:Â https://amchronicle.com