The Middle East has been a global powerhouse in the energy industry, primarily due to its vast oil and gas reserves. However, as the world is transforming rapidly, the region is faces new manufacturing challenges. Additive manufacturing (AM), has emerged as a transformative technology that eases these challenges and develops new opportunities for Middle East’s energy sector.
In this blog by AM Chronicle, we will explore key manufacturing challenges in Middle East Energy Industry and AM as their potential solution. Additionally, we will also discuss some case studies that will help to understand the role of the additive manufacturing technology.
Manufacturing Challenges in the Middle East’s Energy Industry
The Middle East’s energy sector faces several manufacturing challenges that impact its ability to adapt to the changing global energy landscape. Traditional manufacturing methods are often challenging in producing highly customized components and equipment tailored to the specific energy industry needs, whether in renewable energy or oil and gas. AM allows for the production of highly customized components and equipment.
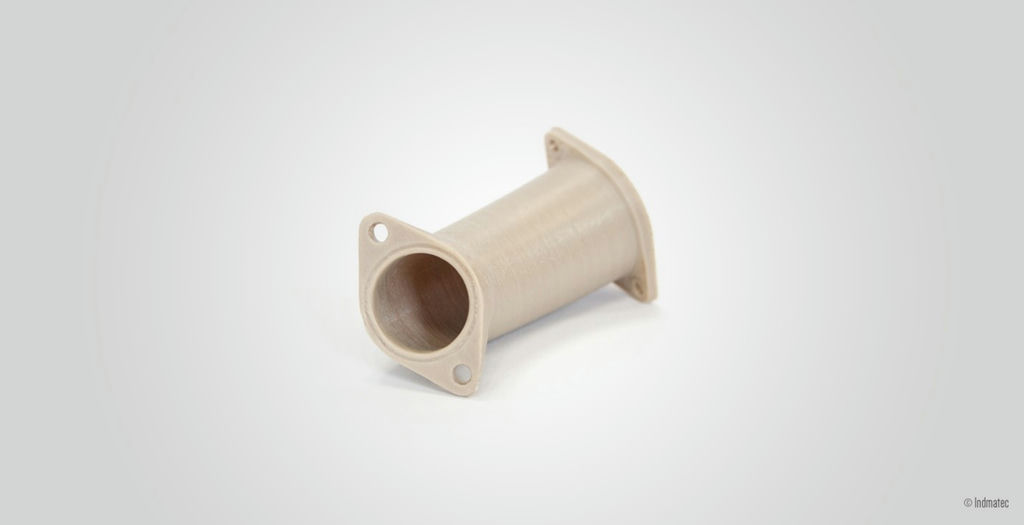
The region’s dependence on global supply chains for critical energy components can lead to vulnerabilities and delays, especially during times of crisis or geopolitical instability. By enabling on-site or localized manufacturing, AM reduces the region’s reliance on global supply chains, improving resilience and reducing the impact of external disruptions. Companies can produce essential parts and equipment as needed.
Developing and testing new energy solutions can be time-consuming and costly using traditional manufacturing methods, hindering innovation. 3D printing accelerates the design and testing process, reducing time and cost. An example is Saudi Aramco, which uses AM for rapid prototyping of downhole tools for oil and gas exploration and production.
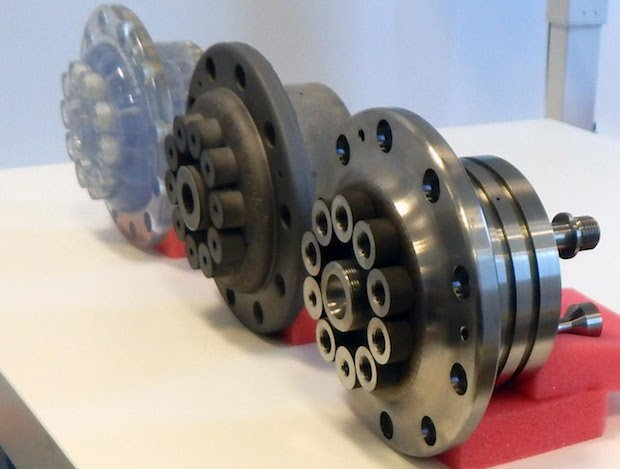
Downtime for maintenance or repair can result in significant financial losses. Waiting for spare parts can exacerbate these issues. Additive manufacturing allows companies to produce spare parts on-demand, minimizing downtime and reducing costs. This is particularly beneficial for the oil and gas industry in the Middle East, where downtime can result in substantial financial losses.
Case Studies
The collaboration between Mimete and NAM was aimed to develop a 90 kg pump impeller using metal additive manufacturing. The impeller was made from Duplex 22CR (MARS F51), an iron-base material. NAM is a company that repairs, modifies, and builds new parts using laser-based Directed Energy Deposition (DED) technology. The impeller passed a fatigue test which showed its capabilities.
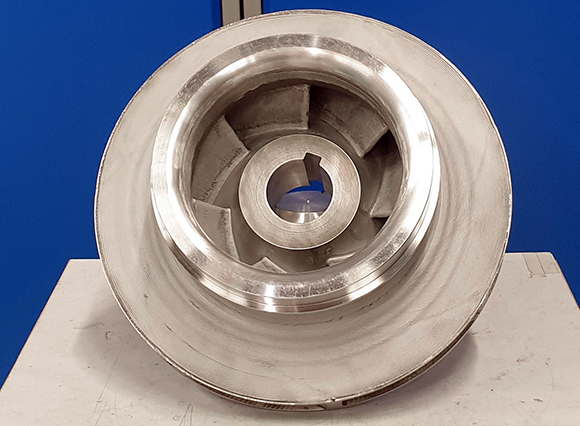
3D printing is revolutionizing the oilfield drilling industry by reducing lead times and costs, and enabling the creation of complex geometries. One example is the EOSINT M 280, which can be used to create long-lasting drilling parts in a short space of time. This has helped to reduce downtime and improve efficiency. Another example is the use of 3D printing to create custom drill bits. These bits can be tailored to the specific needs of each well, resulting in improved performance and reduced wear and tear.
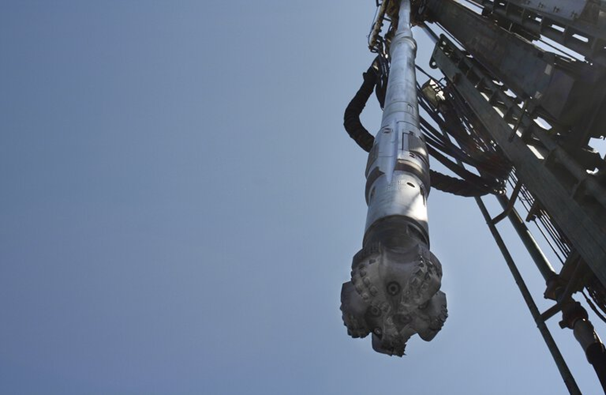
Overall, 3D printing is a promising technology for the oilfield drilling industry. It has the potential to make drilling operations more efficient, cost-effective, and safer.
Conclusion
Additive manufacturing is becoming a game-changer in the Middle East’s energy industry, easing manufacturing challenges and driving innovation. By enabling customization, improving supply chain resilience, and accelerating design iterations, AM is facilitating the transition to cleaner and more sustainable energy sources while enhancing the efficiency and profitability of the oil and gas sector. The Middle East’s adoption of this transformative technology is a testament to its commitment to staying at the forefront of the global energy landscape.