Digital manufacturing is the way for customization, design innovation, higher energy efficiency and additive manufacturing (AM) is the answer towards promoting sustainability in the digital manufacturing era of Industry 4.0 which is the buzz word today. AM reduces the number of steps in the manufacturing workflow with minimal material wastage and helps in reduction of carbon footprint. AM gives engineers numerous degrees of freedom in design and manufacturing, and thus can bring unique products faster to the market. Additive technologies facilitate quick entry into markets and generate new options of production outside factories, and proximity to availability of materials. On demand making of spare parts, reduction or elimination of inventory and complex supply chains is an added advantage.
While, manufacturers have been using AM processes mainly for prototyping, they are gaining popularity in few areas of supply chains. To penetrate the market and enter into a wider arena of applications of AM, research is required to overcome the key challenges encountered. These are identified as given below.
- Process control: Closed loop control systems and key performance indicators (KPIs) are necessary to improve the reliability of the AM process, increase the throughput without compromising quality.
- Dimensional tolerances: Micron-scale accuracy is required in 3D printed components either in as-printed or post processed conditions.
- Surface finish: The surface finish of the products made through AM route need further improvement. Improvement in geometrical accuracy and surface finish can be achieved by a suitable post processing technique that can result in good corrosion and wear resistance at the same time.
- Validation and demonstration: AM service providers and organizations jointly generate acceptance standards for critical structural materials used in aerospace applications. High confidence levels in AM components or their structural integrity can be ascertained by adequate testing, qualification, characterization and thereby consistency in mechanical properties.
Metal additive manufacturing (MAM) has been gaining more and more popularity in the manufacturing sector due to its huge potential in achieving better performance, weight savings and ultimately cost savings. The main areas of focus in advancing this potent manufacturing area are design, process, material, value chain and AM genome. The attributes in each of these areas are listed below:-
1) Design:
Part customization, small scale production and increase design complexity are the advantages AM carries along with itself as compared to conventional manufacturing. The same is shown in Fig.1.
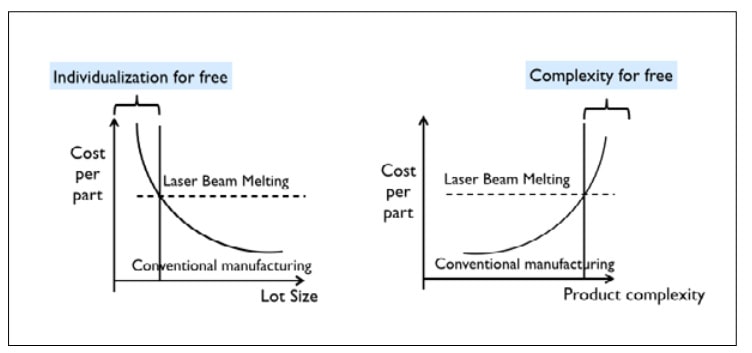
The design factors and their relation in MAM are shown in Fig.2. The design encompasses alloy composition, structure geometry/ topology and AM process parameters. The thermo-chemo-mechanical (TCM) processing domains, microstructure and bulk material properties are treated as hidden design variables. They directly affect the final performance of the product made through AM route. Performance of the product during service is directly depended on the microstructure arising based on the process parameters chosen.
- Complexity exploitation: Identify very complex components and carryout DfAM (Design for additive manufacturing)
- Multipart integration: Identify assemblies of components that can be replaced with single part
- Functionally graded materials: Ex. Thermal Protection systems (TPS)
- Multi-material integration: Ex. Bimetallic adaptors/ joints
- Product individualization and customization
The next important attribute in additive manufacturing is the process or the technology chosen for production. The most widely used MAM processes are laser powder bed fusion (LPBF), powder/ wire fed Laser Directed Energy Deposition (L-DED), Wire arc additive manufacturing (WAAM) and wire-fed Electron beam additive manufacturing (EBAM). The feedstock used in these process ranges from various size ranges of powders to various diameters of wires. The heat source is either a laser beam or an electron beam or a plasma. The process parameters chosen or the resulting heat input in these processes define the microstructure.
Appropriate alloys need to be selected for the different MAM processes. Alloys specific to MAM require that the feedstock is made in necessary powder or wire form. Post processing capability to achieve the specified geometrical features, tolerances and the minimum guaranteed mechanical properties is another key requirement. The ability of the component to perform under various service conditions is another prerequisite. As MAM has evolved in the last one decade, specific classes of alloys have been assigned to specific MAM processes.
- Target higher build speeds- Use processes such as Directed Energy Deposition (DED)
- For Accuracy, Higher resolution –Laser Powder Bed Fusion (L-PBF), Hybrid process – LPBF/ DED +Machining
- Surface quality/ Surface roughness improvement – PBF/ Hybrid, Abrasive flow machining
- Maximum part size components – Choose TIG/ Plasma based Wire Arc Additive Manufacturing (WAAM) route / Electron Beam Additive Manufacturing (EBAM) route
- For 3D Printing of reactive and refractory materials- EBAM
- Minimize cost- EBAM/ WAAM
3) Material
Buy-to-fly ratio is a key attribute in manufacture of components through conventional or AM route where the aim of the later is to reduce and bring it near to unity [4]. Engineers are looking towards AM to minimize the material requirements and manufacture aerospace components of complex shapes and with intricate internal shapes/ structures.
- Standardized feedstock materials- Alternate grades of powders/ wires. Based on Heritage use specific alloy powders/ wires
- Benchmark material property data of each alloy made through different processes – LPBF, DED, WAAM, EBAM technologies
- Document data& process parameters for all alloys being developed through 3D printing route
- Map the Process-property-structure relationships
- Process window boundary has to be modelled and validated through experimentation
- Post-processing guidelines and specifications have to be finalized
4) Value Chain
Reduction of cost is the primary driving factor to adopt MAM into sustainable manufacturing supply chain. Cost reduction can result from either cycle time reduction reduction in feedstock cost, use of cost effective alternate alloys as well as cost of inspection etc.
- Reduce processing costs- use of cost effective alternate alloys
- Reduce material consumption- DfAM, alternate technologies- WAAM
- Reduce feedstock costs- use wires in place of powders
- Reduce quality control costs- Artificial Intelligence(AI) based Process control rather than inspection
- Reduce Labour/ productivity costs- make processes less labour intensive
- Use of Hybrid machines- to reduce cycle time by eliminating additional setting time for machining of components
- Energy efficiency costs
Integrated Computational Materials Engineering (ICME) aims to design materials, components and the processing methods. They link the various materials models at different length scales. Computational modeling significantly lowers the time involved in experimentation. However, it does not totally eliminate experimentation as validation of generated computer models require at least limited experimental data. The ICME framework for metal additive manufacturing is shown in Fig.3.
- Carryout computer-aided materials development – Integrated Computational materials engineering (ICME)- physics based & material properties assisted by models or prediction tools
- Use modular open simulation software/ frameworks
- Use of transparent material property/ open data & validation of the models
- Multi-scale data handling & cloud sharing
- Material property characterization techniques – new and novel ideas for material property characterization (simulation based)
Summary
- An attempt has been made to bring out the focus areas of metal additive manufacturing viz. Design, process, material, value chain and AM genome to make it a value proposition for sustainable manufacturing supply chain.
- AM should be brought into supply chain at the design stage itself by way of design for additive manufacturing.
- ICME based approach involving modeling combined with experimental validation of AM process would accelerate the establishment of processing windows for newer grades of materials
- Cost reduction is the primary driving factor to adopt MAM into sustainable manufacturing supply chain which can be achieved by way of reduction of cycle time, feedstock cost, use of cost effective alternate alloys as well as cost of inspection.
References
- http://s550682939.onlinehome.fr/CommissionsThematiques/DocComThematiques/EPMA_Additive_Manufacturing.pdf
- https://doi.org/10.1007/s11837-020-04028-4
- DOI: 3390/met9111138
- https://www1.eere.energy.gov/manufacturing/pdfs/additive_manufacturing.pdf
- https://doi.org/10.3390/ma15176172
Subscribe to AM Chronicle Newsletter to stay connected: https://bit.ly/3fBZ1mP
Follow us on LinkedIn: https://bit.ly/3IjhrFq
Visit for more interesting content on additive manufacturing: https://amchronicle.com