Credit: VDMA‘s interview with Roland Ladewig, General Manager, ExOne GmbH
ExOne GmbH from Gersthofen develops and builds binder jetting systems. In this interview, their general manager Roland Ladewig explains which materials can be processed in the inkjet-based 3D print technology, where this technology might be applied, and how he imagines a typical additive process chain in the year 2030.
Could you provide us with a short introduction to ExOne?
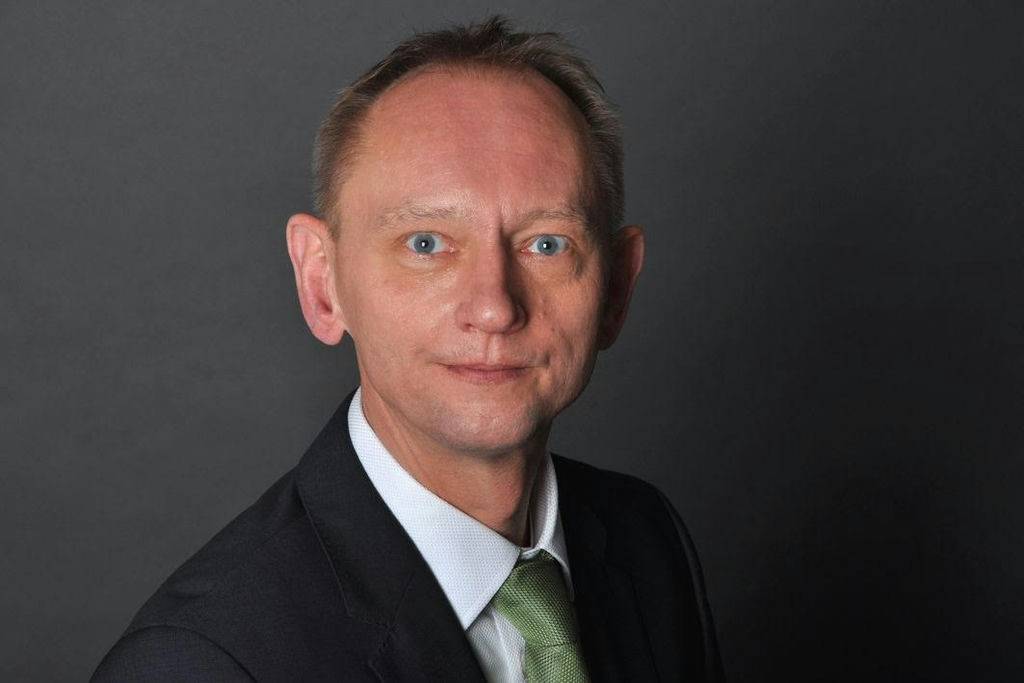
Roland Ladewig: With pleasure. Our roots go back to the year 1999, as this was when an Augsburg start-up of the name Generis developed a first 3D prototype printer for the production of sand molds and cores. Apart from us, the company Voxeljet also arose from Generis. ExOne has been existing since 2005. Today, we have 300 employees worldwide, 140 of them in Germany. Apart from our headquarters close to Pittsburgh and two other US locations, we have a production service center in Japan, six other local branches in Asia, as well as our S. Kent Rockwell 3D Printing Innovation Center in Gersthofen. This is the core area for our mechanical engineering. We develop and build binder jetting systems for series production, prototype construction, and for research purposes. We are dealing extensively with processes of mold construction, and we are the global market leader in the production of sand blasting systems. However, the range of materials for binder jetting is growing. This allows us to directly print metal parts– apart from our indirect contribution through our sand molds and cores for foundries, among other things.
Which materials may be processed with the binder jetting technology?
Ladewig: The range includes quartz sand, synthetic ceramic beads, chromite sand, or zircon for sand molds and cores, as well as metal alloys for direct printing. Among them are the stainless steels 316L and 17-4PH, stainless steel-bronze and iron-bronze, Inconel 625 and 718, as well as bound tungsten which has come to replace lead in many markets. Our technology can also be used to process iron-chromium-aluminium, cobalt-chromium, and ultra-hard tungsten-carbide.
How do your systems differ from the competition?
Ladewig: Our binder jetting technology works without a laser or electron beam source. Instead, the powderbed is spread out and gets bound with a liquid binder suited to the respective material in an inkjet process. This is done layer by layer, the working platform being lowered bit by bit. In this manner, one large or several smaller parts get created by and by. There is no need for supporting structures or a linkage to the working platform. After the binder jetting process, the parts are mechanically stirred and freed from any residue powder through compressed air. Afterwards, metal parts may be cured in a follow-up sintering process, and if necessary, through hot-isostatic pressing. With sand molds, there is often no need for post-processing – this depends on the applied process. A large difference to other technologies is its productivity: our currently largest system has an installation space volume of 2200 x 1200 x 60 mm, and this can be doubled by integrating a second construction chamber. The system produces with an hourly build-up rate of up to 400 liters. In test series, we have achieved tolerances in the mere micrometer range. Together with customers, we are working on exact measurements of the shrinkage resulting from sintering and pressing of directly printed metal parts, so as to optimize construction with these data.Which part of the added value chain of additive manufacturing do you cover?
Ladewig: About 80 percent of our turnovers belong to mechanical engineering, which means sales of our systems. Next to that, we offer the construction and production of molds and cores as well as metallic direct printing parts, and in the United States in particular, we are part of government-funded research projects in the area of material research. The in-house production of components is important to us in order to optimize technologies and systems, and so as to qualify them to each of our customers’ requirements respectively – and to customize them as needed. In indirect technologies as well as in direct printing, we are replacing the expensive, usually material- and energy-intensive tool construction. In this manner, AM means a crucial contribution to sustainable process chains.
Where do you see the greatest need for development in the AM sector?
Ladewig: Our customers care mostly for the technologies’ productivity and their integration into existing process chains. The market demands concepts that allow for integrating 3D printed components into manufacturing chains and distribution channels without any manual steps in between, if possible. We’re addressing the question of industrialization together with our customers in order to direct our machine development towards this target.
How do you imagine a typical AM process chain of the year 2030?
Ladewig: Until then, it will be possible to use the design freedom of additive technologies in industrial processes in full scope. So far, the components’ high individualization results in a need for manual cleaning and post-processing processes. Until 2030, these post-processes will be automated. This will make the integration of 3D-printed components into individualized end products much more efficient. In addition, we will supply a much broader range of sectors and markets – up to individually designed interiors from concert halls to museums. Additive technologies here allow for completely new amalgamations of function and aesthetics. A central prerequisite for opening up new markets is a further development of the material base – in our case, from powders up to binders.
What were your goals in joining the Additive Manufacturing Association within VDMA?
Ladewig: It offers a platform for us to meet representatives from various industries and companies who are dealing with all areas of additive manufacturing; whether it is AM systems, periphery, materials, construction, manufacturing, or research. Where else could you possibly encounter so many perspectives? – And this is not an end in itself, rather, we take up important ideas for the development of our systems and for our orientation from the discussions of the Association. In this way, we have identified a number of projects and topics which we intend to deal with extensively. The exchange helps us to think outside the box, to view our systems in a larger context, and to angle them towards future changes in the production area.