Founded in 2012, BeAM is a company that has been developed rapidly since its inception. Headquartered in Strasbourg, France, BeAM delivers a new generation of (Directed Energy Deposition) DED Solutions. Its technology and clients develop and industrialize their manufacturing and repair processes with an extensive range of services of their production cycle: from feasibility studies and the pilot production phase to the sale of production units and corresponding training programs.
BeAM’s DED solutions are truly a critical ingredient in your “factory of the future”, that are designed durably for the industrialization of metal additive applications. Its first machines made in Strasbourg have been in use in the French aviation industry for two years. Following the company’s acquisition by AddUp, its pace of development and production capacities have increased further.
BeAM’s employees are working on the new machines of the Modulo series at a newly built industrial facility in Strasbourg. The company presented the latest machines from the Modulo series at Formnext 2018, as well as received many orders for them.
With an aim to make additive manufacturing of metal components considerably more cost-effective, the young French enterprise’s technology delivers significantly higher deposition rates, as compared to the powder bed method. It enables the company to further expand the application areas for additive manufacturing.
Acquisition by AddUp allowed BeAM to expand its industrial capability
Based in Clermont-Ferrand, the French metal 3D printing machines manufacturer AddUp has completed the 100% of acquisition of BeAM in mid-2018. With this deal, AddUp is able to expand its portfolio of metal additive manufacturing technologies to better satisfy the needs of its customers and to strengthen its worldwide geographic coverage. This acquisition also strengthens AddUp’s role as a leading player in the French metal 3D printing ecosystem with more than 100 engineers working on the development of new solutions.
“BeAM was at a key stage in its development with the broadening of its product line and its geographic expansion. The arrival of AddUp and its shareholders, Fives and Michelin, enables us to secure BeAM’s development and to benefit from their industrial expertise and the pooling of our respective resources”, specified Vincent Gillet, BeAM’s CEO.
Following the acquisition, BeAM will continue as an independent company under the AddUp umbrella, Frédéric Le Moullec promises. At the same time, BeAM benefits from synergies: for example, when it comes to producing systems based on CNC machines from Fives or ADF. Presently, BeAM is planning production capacities of more than 20 machines per year. “AddUp has given us the resources to significantly expand our industrial capability”, explains Le Moullec. And that includes stepping up international activities, with new branches in Singapore and in Cincinnati, an important center for aviation in the USA.
“Although BeAM has been on the market with its machines for just three years, the French company wants to quickly catch up with the older additive machining processes. The potential of our technology is on a par with that of the powder bed process”, says Le Moullec.
BeAM’s first steps with complex aviation parts
The history of French company BeAM is extraordinary. In 2012, researchers at the IREPA Institute in Illkirch near Strasbourg developed DED technology for additive manufacturing by using conventional deposition welding as a basis and integrated the new method into a CNC machine. The technology was evolved under the BeAM umbrella – initially with just two employees and at a comparatively moderate pace.
When aviation companies Safran and Chromalloy ordered two machines in 2015, BeAM gained a major boost to its development activities. Chromalloy wanted to repair flying parts; Safran wanted to use them forge ahead with its AM development, Le Moullec recalls. We had two customers with very high expectations. These requirements have shaped the further development of the machines and the company and have determined BeAM’s DNA.
Investments by French industrialists enabled BeAM to increase its headcount to 25 in twelve months. The first prototype was developed into a production machine in just one year and was delivered in 2016. And the reference projects generated further inquiries and orders. In the meantime, says Le Moullec, BeAM has delivered 20 machines, mainly to big-name aviation suppliers as well as test and research institutes.
Complex systems work without supporting structures
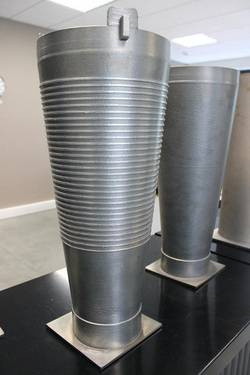
BeAM is capable of building highly complex systems with a relatively small team, because it buys many components like laser sources, powder conveyors, and controllers. The closely guarded technical expertise of BeAM focuses mainly on the integration of these components and on the deposition head. Here the powder, surrounded by argon, flows in a thin stream onto the component and is melted by a laser with rated power of up to 2000 watts. In the five-axis machine, the component plate can be rotated about two axes (B and C) so that additive manufacturing can be carried out in different directions, even without supporting structures.
Le Moullec explains that the great benefit of the DED technology is its high deposition rate of 0.1 to 2kg per hour and its large building envelope. However, DED technology also has its limitations: Internal cavities or lattice structures with optimized topologies are not possible.
Additionally, the wall thicknesses of the component are identified by the thickness of the stream of powder. In addition to repairing additive components and adding to conventionally manufactured parts, Le Moullec considers the BeAM machine’s field of application to lie primarily in areas where powder bed technology or milling reach their limits in terms of cost-effectiveness: for example, where large components made of stainless steel or titanium are involved. We want to manufacture conformal components to minimize postprocessing.
BeAM at Formnext 2018
BeAM showcased its newly manufactured, more compact Modulo 250 at the Formnext 2018. The machine allows a system for automatically eliminating components to be connected through a small antechamber on the side, for example. Even if we may be bringing this to market a little early, the future is modular, explains Le Moullec.
Director Le Moullec explains that welding, and machine operation specialists are in particularly high demand, in order to operate the systems. This expertise is often already available at the factories, and hence, our machine is such a good fit for the workshop.