In an exclusive interview with I3DPn team, Andy Kalambi, President and CEO of US-based additive manufacturing company RIZE, talks about the company’s latest innovations and technologies in 3D printing. He throws light on his vision for the company, as well as describes the target segments for RIZE.
Mr. Kalambi also discusses the company’s plans for Indian 3D printing industry, with sustainable innovations, investments and strategic partnerships.
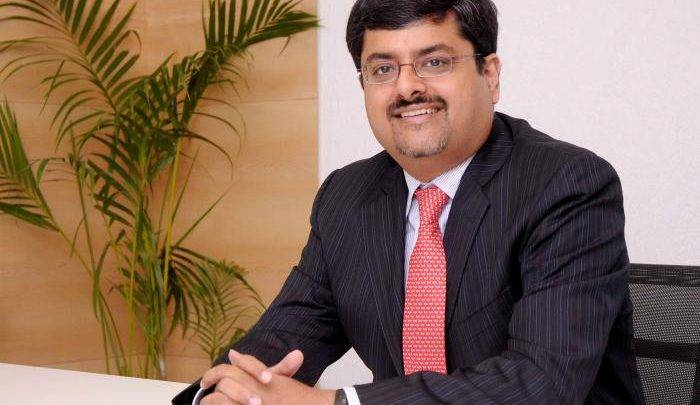
I3DPn: What are the Innovations which RIZE brings to the 3D printing industry?
Andy Kalambi: In 2017, we introduced a breakthrough platform, RIZE™ ONE, that defined Desktop Industrial 3D Printing. The new platform makes industrial 3D printing safe and easy for additive manufacturing labs, small-to-medium businesses and enterprise customers.
This new solution was the world’s first hybrid 3D printer, which combines two discrete technologies, material extrusion and material jetting that allows a one-touch experience to produce parts at the lowest total cost of ownership. These parts have the capability to digitally connect to Industry 4.0 technologies.
Our unique and patented technology, called Augmented Deposition, made this possible. The RIZE ONE printer offers inclusive multi-material printing with minimal post processing, which also allows sustainable use of safe, non-toxic and recyclable materials.
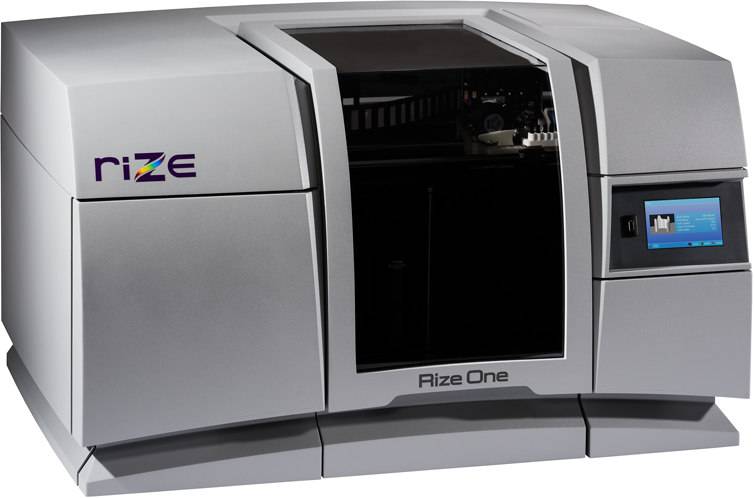
In early 2018, we introduced the first ever Digitally Augmented Parts for authentication, traceability and Industry 4.0 capabilities. With these new innovations, our company has been recognized as an ’IDC Innovator – Plastic-Based 3D Printing 2018’ and received the award for ‘2018 Best Practices in Technology Innovation in the Zero-Emission Polymer Material Additive Manufacturing Industry’ by Frost and Sullivan.
At Formnext 2018 in Frankfurt, Germany, we did it again, redefining industrial 3D printing forever. We enhanced the value of our RIZE ONE printer by providing a compelling range of new materials such as carbon composite, in order to enable a new set of industrial applications. Our current materials, RIZIUM™ ONE White and Black are already demonstrating their value in delivering strong and safe parts for functional prototyping, jigs, tools and fixturing and end-use service parts. At Formnext, our company added RIZIUM™ CARBON and we will release an additional material called RIZIUM™ ENDURA in 2019.
At Formnext, our company also previewed a new desktop additive manufacturing system, XRIZE™, which will, for the first time, enable users to manufacture functional polymer and composite parts in full color. Like our first product, RIZE™ ONE, the experience of using the XRIZE 3D printer is as easy and safe as an office 2D printer. Users can use our XRIZE printer for manufacturing full-color prototypes for FEA and stress analysis, tooling with safety instructions, consumer products, package design, GIS mapping, anatomical parts for patient/clinician communication, pre-surgical planning and parts for marketing and the entertainment industry.
I3DPn: Can you throw some light onto the technology and its benefits?
A.K: Our first innovation, RIZE™ ONE, builds enhanced engineering-grade thermoplastic parts with unmatched features, such as digital traceability and part identification. It comes with best-in-class Z-strength and simple post-processing.
We have built the RIZE ONE printer with industrial class features, including a heated build chamber that ensures parts are printed with dimensional accuracy and superior layer adhesion. It also features an automatic filament swap that simplifies supplies management to ensure uninterrupted printing, a locking cover that prevents operator injury and it complies with regulatory safety standards. And consumable cartridges are digitally encoded to ensure the correct process parameters are applied for every print job.
Our Augmented Deposition process, is a hybrid of extrusion and jetting. It allows jetting of a specially formulated release agent between layers of extruded material and the support structures which enables the support structures to be quickly, easily and removed, leaving a superior finish on supported surfaces. Jetting also provides for the indelible application of graphics, text and digital tracing information on any part surface.
We have designed RIZE ONE to work in any environment. It offers Zero VOC emissions that make this printer the right choice for offices, factory floors, educational institutions and any environment with health and safety concerns.
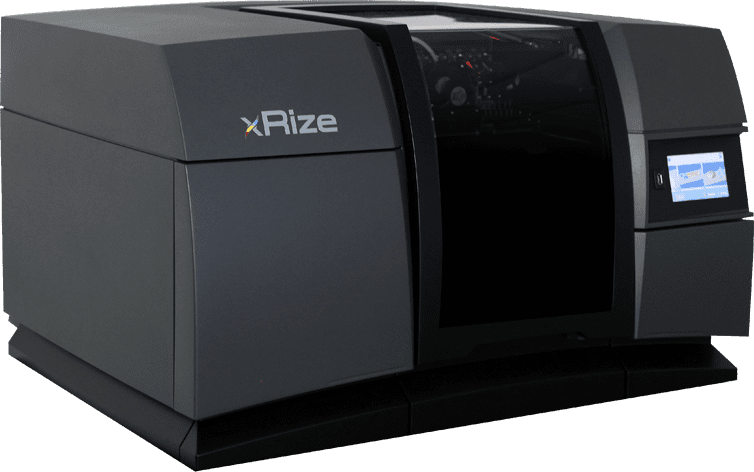
Our latest innovation, the XRIZE 3D printer, also leverages RIZE’s hybrid Augmented Deposition process by extruding our proprietary compound of engineering-grade thermoplastic and simultaneously jetting C, M, Y, K (cyan, magenta, yellow and black) inks through industrial printheads wherever they are needed to achieve the full-color part. Similar to RIZE ONE, release Ink is jetted between the part and its automatically-generated supports to enable the user to quickly peel the supports away from the part, leaving a smooth surface finish and eliminating the need for additional finishing. With our RIZE OneTouch software, users can quickly and easily apply text, images and texture maps to monochrome part files or import color CAD files.
I3DPn: What are the target segments for RIZE?
A.K: Our customers generally fall into three categories:
Additive manufacturing lab managers or model makers who need to augment their current capacity of extrusion printers to deliver parts to their end users faster and who want to increase end user satisfaction with our unique ink marking capability.
Small-to-medium size business owners who need a “workhorse” to deliver a wide variety of additive manufacturing needs, including functional prototypes, tooling, jigs, fixtures and service parts. They select our company for the low investment, an ROI of less than 4 months, our safe and easy process, increased revenue and reduced costs.
Heads of departments at large enterprises need to produce custom tooling, jigs, fixtures and service parts. They purchase RIZE to augment their tool room capacity, freeing up existing machines for larger jobs.
As mentioned earlier, with XRIZE, users throughout the enterprise, from engineering to marketing to the manufacturing floor, can easily manufacture prototypes and functional parts for a range of applications and industries. Moreover, the full-color capability of XRIZE enables a wide range of applications across academic departments, such as architecture, geology, geography, life sciences, engineering product design and the arts.
I3DPn: What plans does RIZE have for India?
A.K: Our approach to driving inclusive and sustainable innovation is well aligned to India’s focus on ‘Make in India’ and ‘Digital India’. Our focus is to help additive manufacturing drive competitive advantage both on cost and innovation for both large and SMB companies. We will invest in establishing a significant presence through strategic partnerships with existing 3D printing resellers, software and systems integrators. RIZE is a Co-Innovation Partner of Tata Consulting Services (TCS). Our company has also established a reselling relationship with Aurionpro Ltd, a publicly listed technology company.