Additive manufacturing has clearly been a major disruptor in sectors where it has been adopted, and this disruption propagates through the supply chain.
Since the rise of additive manufacturing (AM) in the 2010s, many businesses across the world are now looking at this method of manufacturing to see where it can add benefits across the supply chain.
Here we’ll discuss the rise of AM and what we can expect to see in the future.
Andy Imrie:
AM has been around for many years now. Its rise in the 2010s was a very exciting time and we’ve emerged from the ‘hype curve’ to see some very solid use cases for this method of manufacturing. Although we knew that AM had the potential to disrupt many industries, the speed of adoption and adaption of the technology involved by so many different industries is surprising.
One of the most interesting developments we’ve seen is the way that AM was used in response to the COVID-19 crisis, from simple ear protectors to new ventilator parts. However, regulation of medical devices is as critical as ever, so although the parts may have been produced quickly, they could not always be used where needed.
Right now, we are seeing the USA and Europe dominating the AM market, with some excellent work in Singapore, China and Israel, amongst others. AM is a truly global product, with adoption driven mainly by OEMs and supply chains. For example, logistics companies realized very quickly that AM can have a huge impact on their businesses, with spare parts being produced at point of use or close-to-end, which reduces the need for shipping and in some cases, saves items crossing borders and through customs.
We’re also seeing certain countries with their own AM initiatives which are helping to shape the industry further by encouraging more companies to adopt the technology within that country e.g. America Makes in the U.S. and the Dubai Future Foundation in the UAE.
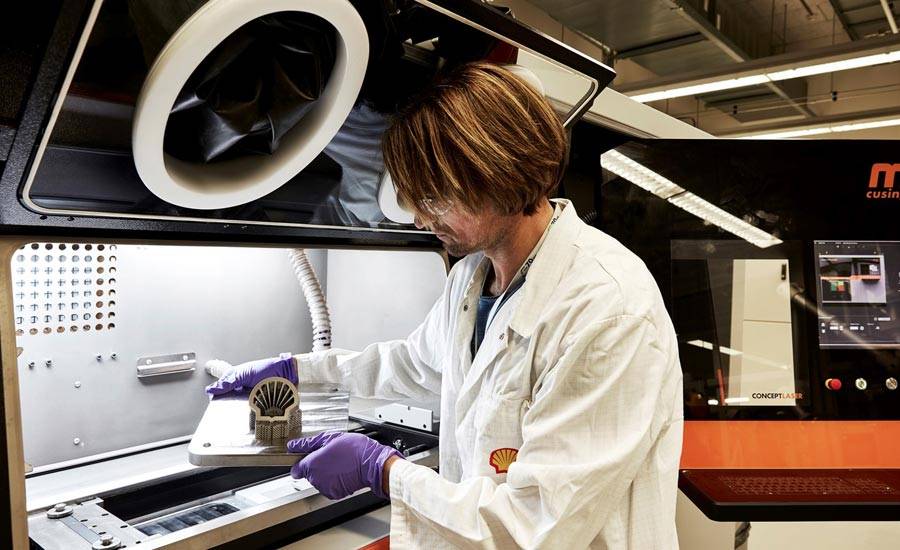
Sector focus
When it comes to sectors, aerospace and medical have been at the forefront of AM adoption and the number of use cases in these industries now runs to the many hundreds, if not thousands. Other sectors now adopting the technology include automotive with many AM parts being incorporated into vehicles, while oil and gas, marine and energy are also now seriously looking at AM. For these sectors, new materials, replacing metals with polymers, digital warehousing, obsolete parts and consolidation of parts into one component are proving to be of great interest. Space is another fast follower and we are seeing satellites with numerous AM parts fitted which reduces weight, improves efficiency and allows for cost effective customization.
Obstacles to adoption
Of course, there are obstacles as with any new technology and one of the largest hampering wider adoption of AM is the lack of regulations and standards. At LR, we’re supporting the development of standards and Joint Industry Projects (JIPs) with the aim to make AM ‘business as usual.’ Currently, there are only a handful of standards with a section on AM, so for industries looking to replace traditionally manufactured parts with AM ones, the route to market can be difficult. When complete, AM will be one of the few industries where standards will be truly global, with the ISO committees working hand-in-hand with their ASTM International counterparts.
Pushing the boundaries
At LR, AM is all about the three C’s: complexity, customization and consolidation. AM enables you to really push the boundaries in all of these areas, which allows failure modes to be designed out. Complexity may allow a heat exchanger to be more efficient for example, reducing the impact on the rest of the system. You can customize parts/ materials for each application, which allows for a bespoke solution that better meets the need of the requirement, using materials that may not be possible using traditional manufacturing. Consolidation is one of the biggest quality advantages—by removing the failure modes at joints and having one component, you have greatly increased the quality of the part, providing (just like any other manufacturing method) the end product is compliant to its specifications.
David Hardacre:
We’ve seen numerous successful applications of AM across various industries, although different industries typically seek to achieve different benefits from using AM. For example, in aerospace, huge reductions in the buy-to-fly ratio have been achieved for specific parts, which leads to savings not just in time and cost for the production of the part itself but also weight reductions, leading to efficiency improvements through the operational life. In other industries, such as medical, the ability to customize a part to a particular application (or patient) presents the opportunity to overcome challenges that could not be achieved previously. Similarly, in industries such as energy and marine, reduced lead times for production and potentially ‘local’ manufacture can lead to significant reductions in the number of spare parts required.
What we’ve seen to date is that AM has clearly been a major disruptor in sectors where it has been adopted, and this disruption propagates through the supply chain. Currently, adoption in many sectors is still relatively low but where the targeted benefits are being realized, manufacturers are recognizing the potential for further benefits, for example, setting up virtual stores of digital parts that can be printed on demand. This leads to a reduction in the number of physical spare parts, which in turn, can lead to reduced production load on suppliers, reduced transportation requirements and reduced insurance premiums (due to reduced total asset value), so the disruption goes beyond the manufacturing facilities which adopt these new technologies.
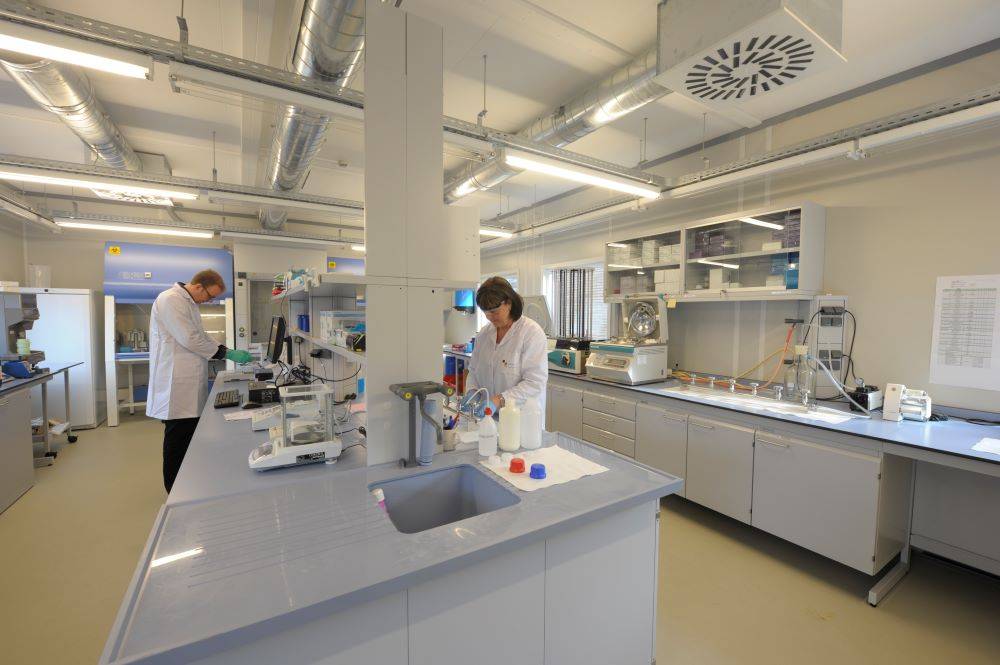
Materials of choice
Within metal AM, the most popular materials to date have been titanium alloys (especially Ti-6Al-4V), nickel alloys, aluminum alloys and stainless steel. For powder-based technologies, popular materials are easily identified by the availability of published ASTM powder specifications. This has been dominated by early adopters, especially in aerospace and medical industries, but as more industries adopt AM technologies, more materials will become more widely available to meet the requirements of those industries. There has also been significant interest in replacing parts that are traditionally metal with composite or polymer-based alternatives. This, of course, requires a feasibility assessment of the proposed replacement material for the application but, where appropriate, presents potentially significant savings in both cost and production time.
The role of standards
Once manufacturers progress from producing prototypes and demonstration parts to producing products that are intended for placing on the market and putting into service, then the regulations or codes applicable to the part being produced remain relevant regardless of the manufacturing method used. Typically, the most efficient way to demonstrate compliance with the regulatory requirements is to utilize an application-specific standard that includes the method of manufacture used.
However, many of these application-specific standards do not yet include AM methods, in which case the most efficient way to demonstrate an equivalent level of safety would be to use AM-specific standards to bridge the gap. Furthermore, standardization can help to set the required benchmark for various activities and compliance with these standards as a way to provide confidence that the AM materials and parts can be used safely.
Future predictions
Currently, due to the inherent variability and uncertainties of these technologies, coupled with an incomplete suite of published standards, the amount of post-build inspection and testing required can limit the benefits realized. There is currently a significant amount of research and development work that is investigating the use of in-process monitoring to perform inspection during manufacture and this offers the potential to reduce the overall lead time significantly. The use of digital stores, coupled with distributed, qualified facilities for production, would enable ‘local’ and ‘just-in-time’ manufacture.
This insight has been published from QualityMag.