A major training base for the U.S. Army provides realistic joint and combined arms training to develop the U.S. Army’s soldiers and leaders for the battlefield. They train soldiers for upcoming deployments, wherever that may be in the world.
By using additive manufacturing technology, the Army is able to create readiness factors that decrease downtime.
The Challenge
“Readiness” is a term the U.S. Army often uses, which refers to the need for troops, formations, and equipment to perform under the pressures of military operations. They constantly strive to increase readiness by innovating faster and better than other military groups around the world.
The military-grade vehicles and equipment that are critical for mission support endure a tremendous amount of wear and tear. If a part breaks, soldiers have fewer resources to use at the training center, as lead times for replacement parts are as long as three months due to the facility’s remote location. The process is long and inefficient as well as costly, and a single part breaking can have severe ramifications on a squadron.
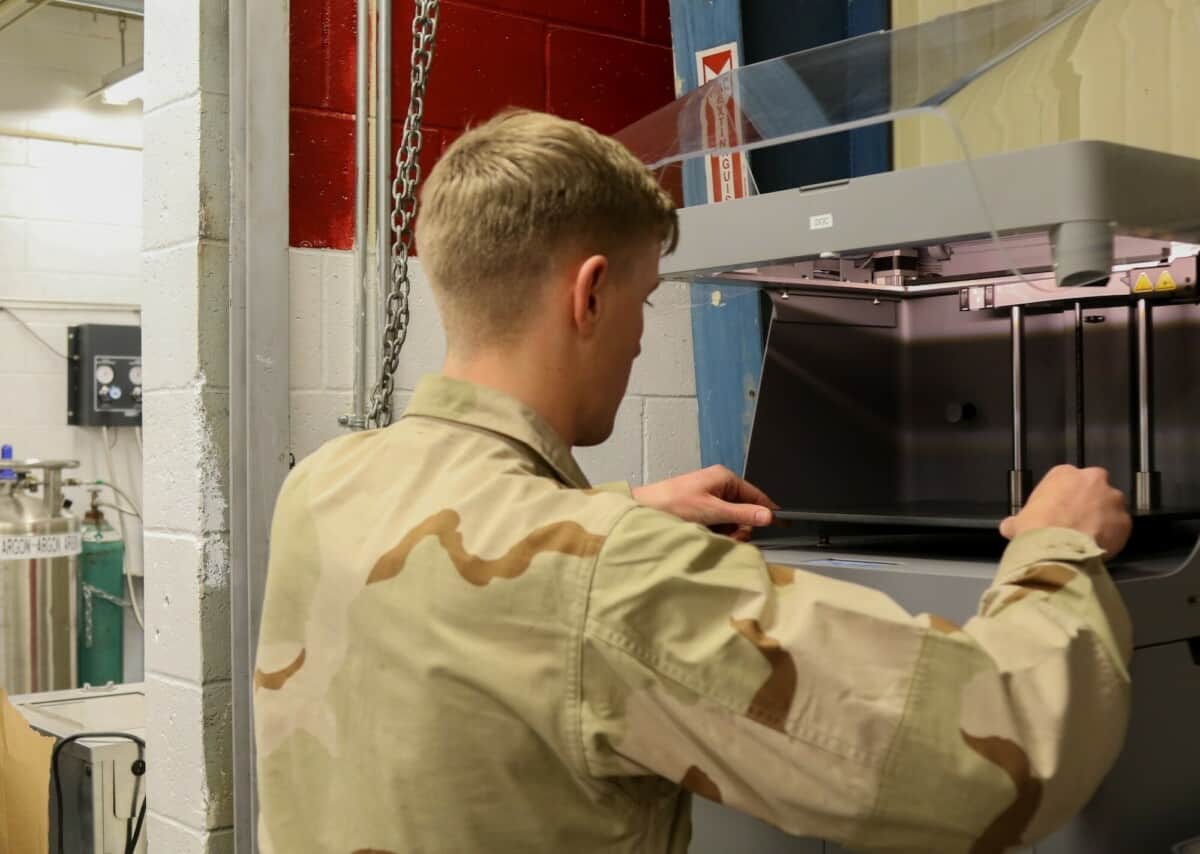
The Solution
There are currently 10 centers in the U.S. that focus on specific areas to train soldiers and servicemembers. In late 2019, after researching various types of 3D printers, one training base brought in two Markforged X3 industrial 3D printers and one Mark Two desktop 3D printer. The regiment needed durability, functionality, and versatility — and Markforged machines’ Continuous Fiber Reinforcement (CFR) printing process gives them the ability to print with continuous carbon fiber, fiberglass, and Kevlar®. The U.S. Army’s Markforged composite printers have been used for personal protective equipment (PPE), window wiper brackets for military vehicles, tools, and low-volume production parts.
The regiment has also started to 3D print a critical low-volume replacement part for a component that is no longer available: a hatch plug that sits on top of a vehicle used in low-light scenarios. The hatch plug helps the driver see at night, giving the driver the ability to tell the soldiers to engage. Unfortunately, this part is not in production anymore, and would cost roughly $10,000 to reproduce, not to mention the 3-month lead time. With Markforged, the regiment printed the hatch plug in Markforged Onyx material for $230, and then another using 17-4PH Stainless Steel on the Metal X for $800. This application alone has saved the regiment $244,000.
The regiment has saved a significant amount of time and money with Markforged printers, but they have also simplified the hatch plug with fewer components. It’s now an easier, simpler product — the previous design comprised ten parts, but is now down to four. The U.S. Army base intends to continue printing tooling and fixtures, as well as small production parts with traditionally long lead times, to ensure their soldiers are able to properly utilize the resources at the center.
Along with the printers, Eiger — Markforged’s powerful slicing software — has been beneficial for the regiment and Soldiers. Users within the regiment have seen the benefits of the Digital Forge platform, and have found the software to be highly optimized for both the printers and the platform. While other additive manufacturing software platforms are free rein when it comes to choosing temperatures and speeds, Eiger has an optimized, hands-off approach that works with their machines, resulting in higher-quality parts.
The Future
This U.S. Army training center has been utilizing Markforged printers since early 2020, with plans to bring in more additive manufacturing capabilities. Markforged University also plays a big role in the U.S. Army’s readiness by training soldiers how to properly use the Markforged platform. Getting several soldiers certification on Markforged software and printers is a significant value add for the U.S., as without a proper understanding of how to best use Markforged technology, the team may not be as effective at designing parts for additive manufacturing.
The training center’s use of Markforged technology has become a catalyst for other similar centers around the U.S., who have come to visit to get an idea of what is possible.
Subscribe to AM Chronicle Newsletter to stay connected: https://bit.ly/3fBZ1mP
Follow us on LinkedIn: https://bit.ly/3IjhrFq
Visit for more interesting content on additive manufacturing: https://amchronicle.com/