Additive Manufacturing can be applied to many cases, including the reproduction of broken or worn components, whose spare parts are difficult to obtain or no longer available. Circumstances like these are even more and more frequent nowadays; the impossibility or delays in finding spare parts can compromise the workflow of production cycle with consequent loss of time and money.
The reverse engineering process, combined with professional 3D printing and high-performance composite materials, allows the broken or worn production tool component to be quickly reconstructed and replaced, allowing the production system to immediately return to operational status, saving a great deal of time and money. The following case study, can be extended to the situations above.
It is about the reconstruction of a T-shaped attachment bracket using reverse engineering process, selective laser sintering technology and Carbon-fiber reinforced composite material. The T-shaped attachment bracket is fixed to a linear actuator for large electro-mechanical blinds.
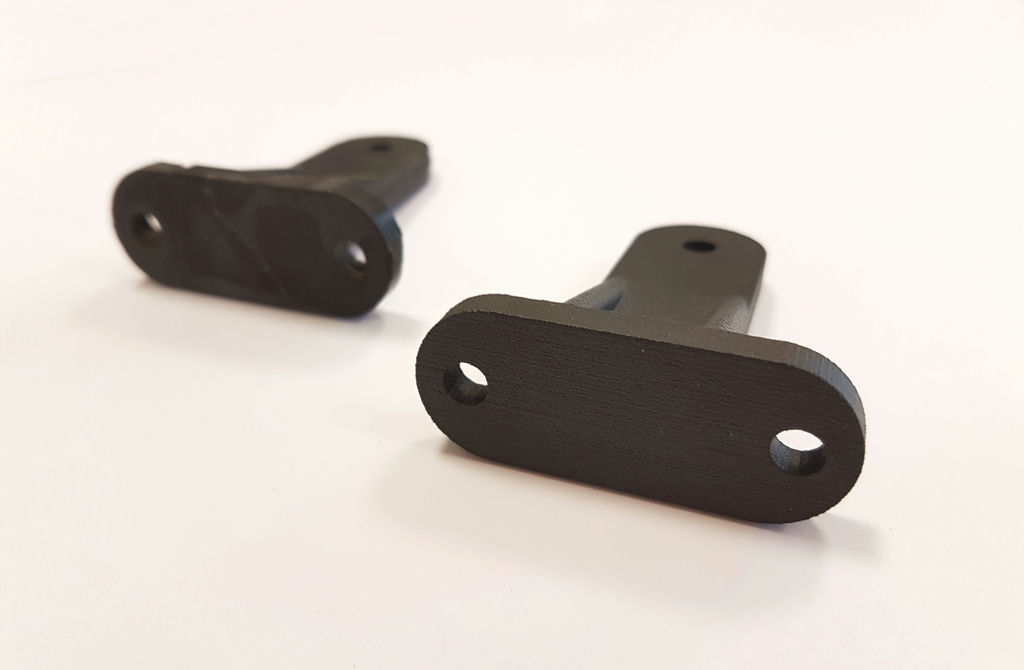
Due to wear and prolonged use, this part broke into three parts making it impossible to open and close the blinds.`The setback has been turned into an occasion for a field-testing, to demonstrate that the most advanced technologies are vital when – for example – obsolete spare parts are no longer available. In fact, advanced technologies can quickly rebuild components, allowing the production process to get back to operate immediately, with a huge savings of time and money.
CRP Technology, the 3D printing company based in Italy and world leader in the field of the most advanced additive manufacturing technologies and composite materials, conducted the field-testing. The CRP Technology’s manufacturing path starts with the evaluation of the 3D file of the component to be built.
Already at this point, however, the CRP Technology experts found themselves facing an obstacle: the impossibility to get the 3D file of the T-shaped attachment bracket.
Thanks to the experience gained and 3D laser scanning technology, the CRP Technology team has managed to overcome the issue by using reverse engineering: this is a process that replicates a design by Laser scanning, to create 3D data that allows for modifications, adaptations or reconstruction of the part. CRP Technology’s expert team then applied reverse engineering process:
- Digitization phase – Data captured from the surface of the T-shaped attachment bracket by scanning, to obtain its initial geometry.
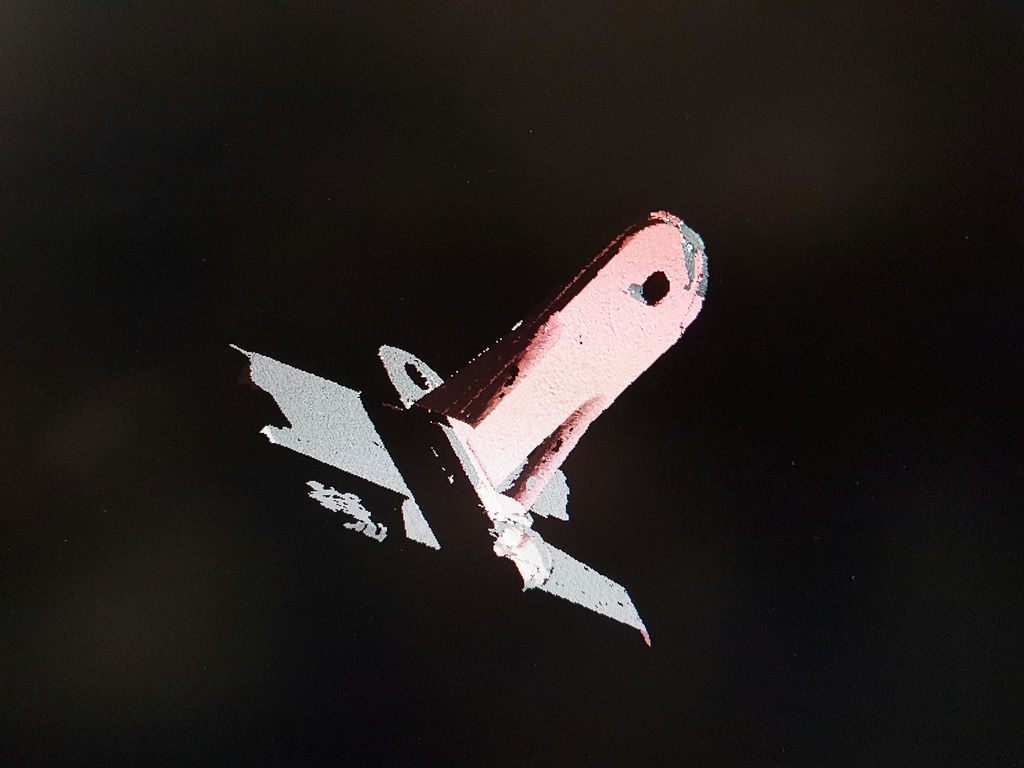
- Reconstruction phase – Data processing
From the mesh, through the use of special engineering CAD software the solid geometry is reconstructed and fitted to the original shape.
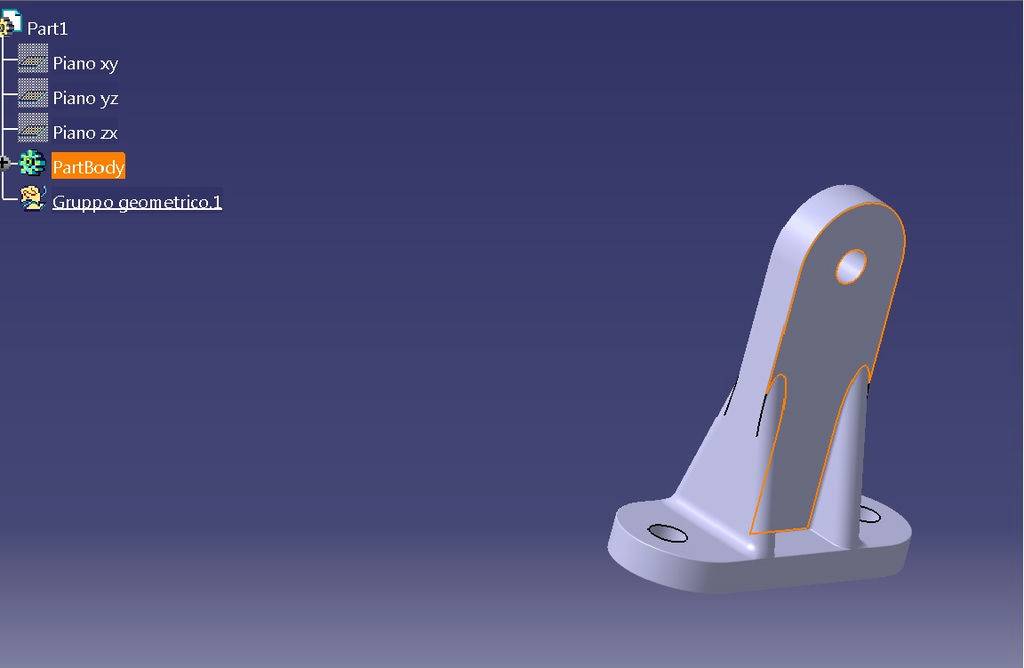
Production phase – Manufacturing of the functional part via professional 3d printing and Carbon-composite material
Once the 3D .STL file was produced after reverse engineering, CRP Technology team proceeded with the creation of the T-shaped attachment bracket using Windform® TOP-LINE composite materials and selective laser sintering technology. As a manufacturing material, Windform® SP was chosen, a polyamide-based Carbon composite material from the CRP Technology’s TOP-LINE range of high-performance composite materials. The material has excellent mechanical properties, with high level of impact strength and elongation at break, as well as excellent resistance to high temperatures.
The overall manufacturing, from the reverse engineering phase to the construction via 3D printing, took place in just a few days. The CRP Technology team inspected the Windform® SP, T-shaped attachment bracket, and were very satisfied with the result obtained.
Dimensional control, validation and assembly on site
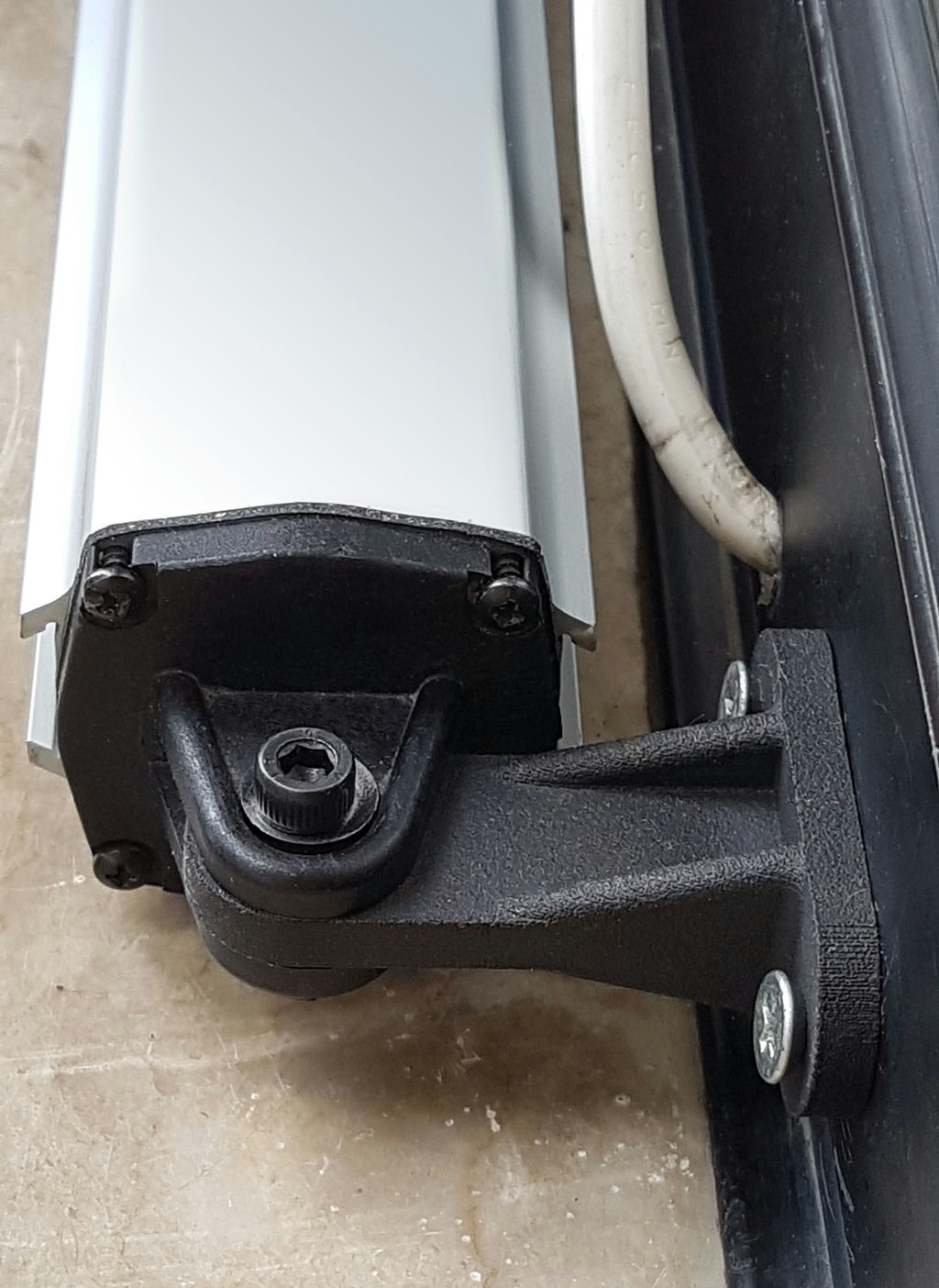
The Windform® SP T-shaped attachment bracket has been scanned again to check for dimensional accuracy to ensure its conformity with the original. Once the validation phase was completed, the Windform® SP T-shaped attachment bracket has been mounted in place of the original. Field-tests led to excellent results, and the correct functioning of the Blinds was restored. The use of cutting-edge technologies has allowed the reconstruction and implementation of the component in a short time. The material used, the highly performing Windform® SP, has guaranteed the full restoration of the original functions of the structure.