Created with advanced computational engineering technology from LEAP71, to be displayed at Formnext
Chinese 3D printer OEM EPlus3D has produced the world’s largest single-piece 3D printed rocket thruster, standing at over 1.3 meters in height. Designed to leverage the enormous build volume of the EPlus3D EP650-1600 metal powder bed fusion printer, this thruster leverages cutting-edge advancements in computational engineering, provided by LEAP71, and 3D printing.
Engineered by Josefine Lissner at LEAP71, the thruster boasts an impressive thrust capability of 200 kilonewtons (kN), making it 40 times more powerful than the Noyron TKL-5 thruster, which had its successful test run earlier this year. This engineering feat was achieved through a collaborative effort with EPlus3D, pushing the boundaries of additive manufacturing in aerospace applications.
Two weeks of continuous printing
The rocket thruster was constructed from aluminum, a notoriously challenging material for high-temperature applications due to its cooling requirements. EPlus3D’s thruster employs a dual cooling mechanism that integrates cryogenic liquid oxygen to cool the main combustion chamber, while kerosene provides cooling for the nozzle’s upper section. This complex, functionally integrated design was printed in a single, uninterrupted run over 354 hours, demonstrating the robustness and capabilities of the EPlus3D EP650-1600.
Incredibly, the thruster required no post-processing; the as-printed surface finish achieved a quality level rarely seen in additive manufacturing, making this rocket engine both a functional and aesthetic accomplishment.
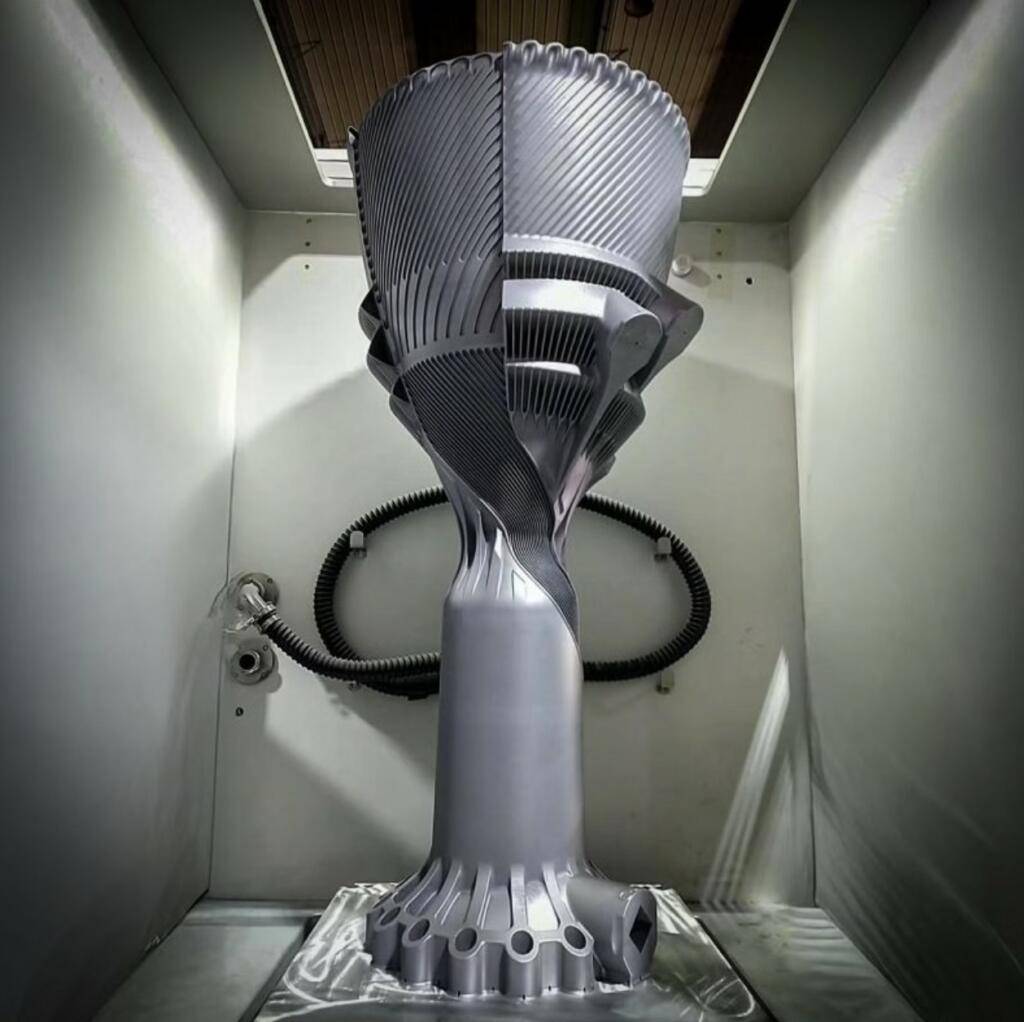
Designed directly from specs
Central to this breakthrough is the use of LEAP71’s Noyron Large Computational Engineering Model, enabling a sophisticated design optimized for propulsion and thermal dynamics. The model’s computational power allowed LEAP71 engineers to manage complex thermal stress and fluid dynamics challenges. Additionally, the thruster is built upon LEAP71’s PicoGK geometry kernel, renowned for its compact yet powerful performance in high-precision engineering tasks.
Although it is mostly intended as a demonstrative part to be displayed at Formenxt, this project from Eplus3D and LEAP71 undoubtedly demonstrates the capacity for large-scale 3D printed parts in aerospace but also showcases the potential for functionally integrated parts in applications where durability and high performance are paramount. The success of this collaboration highlights the advancements in additive manufacturing machines capable of producing massive, high-functional parts.
More information on the rise of large-format, high-productivitymetal PBF technologies is available in VoxelMatters’ newest Metal AM Focus 2024 eBook, which was released just last week and can be downloaded for free at this link.