Founded in 2011 by Dr. Johannes Homa and Dr. Johannes Benedikt, Lithoz began as a small garage venture. Today, it has grown into the global leader in ceramic 3D printing.
Lithoz offers powerful ceramic 3D printers to meet the demands of high-performance industries. Their line of CeraFab System printers, based on patented Lithography-based Ceramic Manufacturing (LCM) technology, delivers ultra-high precision, design flexibility, and complex manufacturing capabilities.
Table of Contents
The company’s LCM technology makes it possible to produce even the most intricate geometries and miniaturized structures, enabling designs which are unachievable using conventional ceramic processes. Up to 100 CeraFab System S65 printers can be wirelessly connected for global series production through intuitive CeraControl software, enabling mass production across independent locations.
With over 150 employees and four global locations, Lithoz operates its headquarters and production facilities in Vienna, Austria, where it also manufactures premium ceramic materials in a cleanroom environment under ISO 9001:2015 certification. With Wendt India as a partner, visitors at this year’s AM Tech will have the chance to see Lithoz parts on display and experience the power of LCM technology for themselves.
Valuable Partnership with Wendt India
As a pioneer in ceramic 3D printing, Lithoz values partnerships with other forward-thinking manufacturers to help drive innovation in ceramic 3D printing forward. In 2021, Lithoz formed a strategic partnership with Wendt India, marking a major expansion of LCM technology into the Indian market. With installations in Bangalore and Mumbai, Lithoz is making cutting-edge ceramic 3D printing technology accessible to a new range of industries in India. The partnership was inaugurated at IMTEX 2023 with a Lithoz CeraFab System machine live at the Wendt India booth.
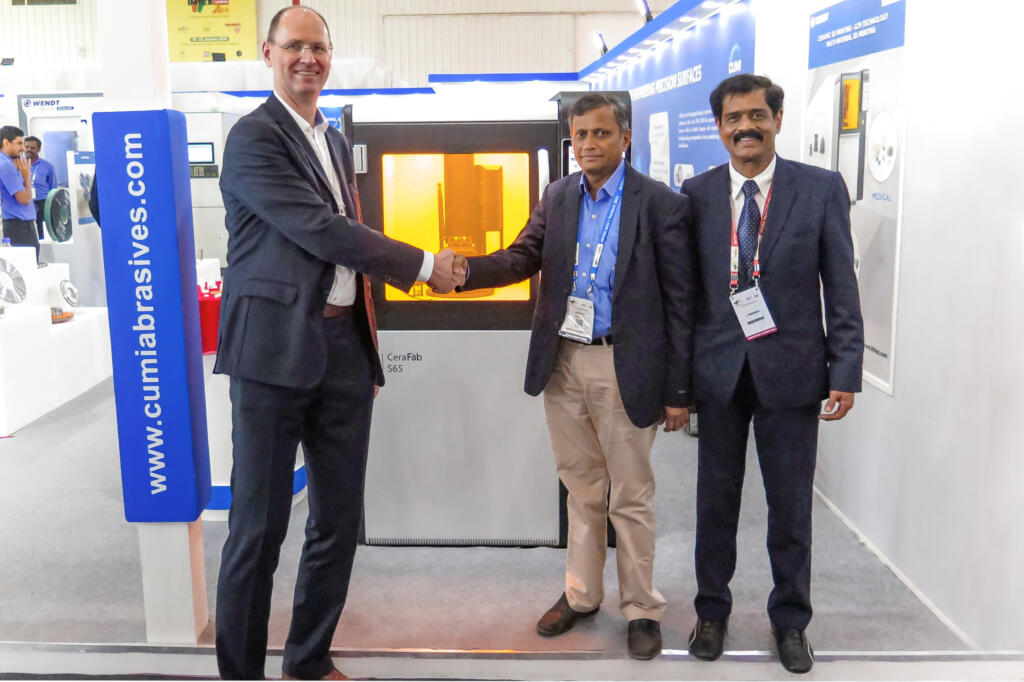
With Lithoz bases already set up in other locations around the world, including in Austria, the USA and China, this cooperation ensures a much deeper understanding of the market and its specific needs to lay the solid foundation for the strategic business development in India.
The Future of Ceramic 3D Printing: LCM Technology
Lithoz’s LCM technology is revolutionizing the production of highly complex geometries and miniaturized structures. This capability is critical for industries where precision and innovation are paramount. The state-of-the-art CeraFab System S65, as the industry-leading 3D printer for technical ceramics, leads the way in serial production of ceramic 3D-printed parts. This machine has been designed for ultra-precise, large-scale production with a freedom in design which is unachievable using conventional manufacturing methods. Another member of the CeraFab System family, the newly launched CeraFab System S320, caters to the highly productive serial production of mid-sized parts with its significantly enlarged build platform, which is five times bigger than that of the S65.
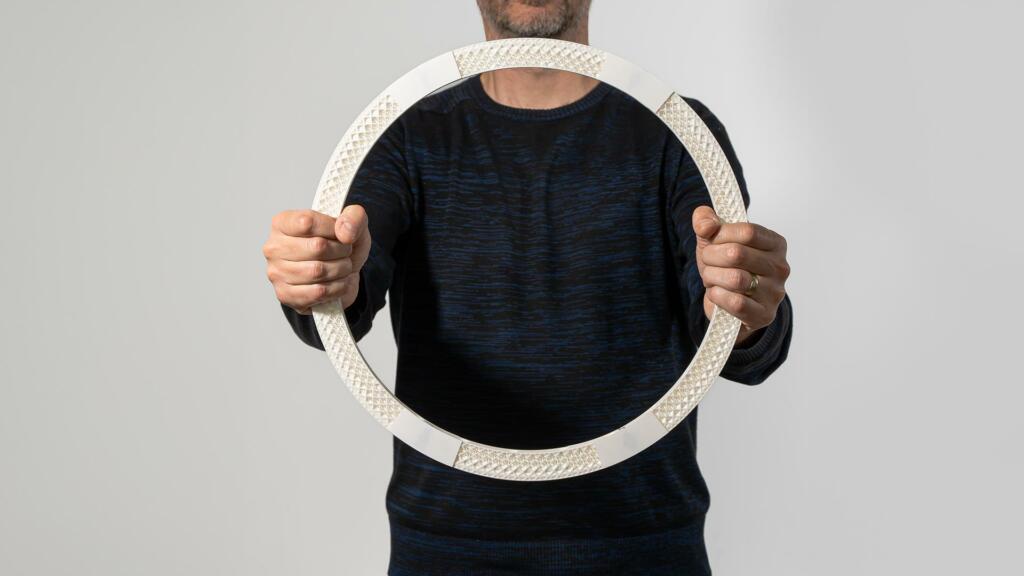
In addition, the CeraFab Multi 2M30 allows for the combination of multiple materials – such as ceramic and metal – within a single part or even a single layer, pushing the boundaries of multi-material 3D printing and unlocking a wealth of new possibilities. For businesses just beginning to explore ceramic 3D printing, the CeraFab Lab L30 offers a compact yet powerful entry point. Despite its smaller footprint, this machine delivers the full manufacturing capabilities of Lithoz’s LCM technology, making it an ideal solution for those new to ceramic 3D printing. The CeraFab Lab L30 enables precise fine-tuning of parts and designs, supporting innovation and experimentation in research environments.
High-Performance Materials for Every Industry
In addition to their market-leading machines, the company is also a forerunner in developing specialized ceramic materials for the LCM process. Their portfolio includes ceramics designed for high-performance sectors such as industry, aerospace, and medicine. From robust alumina and thermally resistant silicon nitride to biocompatible zirconia and bioresorbable hydroxy apatite for medical applications, Lithoz ensures that industries can leverage the right material for their specific needs. Aluminum nitride, as another key material, ideal for use in the semiconductor industry due to its durability and thermal properties.
Case Study: LCM-Printed ALD Ring
Significant breakthroughs have already been made in industry and aerospace using the company’s LCM technology. For example, a 15-inch alumina gas distribution ring was produced by Alumina Systems using Lithoz CeraFab printers, offering superior performance compared to conventionally made rings. The design, optimized for minimal material usage, resulted in a lightweight, thin-walled structure while maintaining constant gas flow, even with reactive gases. This innovative approach also enabled on-site production, turning the concept of digital warehouses into reality, reducing storage needs and enhancing efficiency in manufacturing.
Experience Lithoz technology in person: Wendt India at AM Tech
As a valued Lithoz partner, Wendt India will be showcasing several highly complex parts for industry and aerospace produced using Lithoz LCM technology. Make sure to visit Wendt India at the upcoming AM Tech event at stand D7 to see these parts for yourself!
Technical Writer, AM Chronicle
Chinmay Saraf is a scientific writer living in Indore, India. His academic background is in mechanical engineering, and he has substantial experience in fused deposition-based additive manufacturing. Chinmay possesses an M.Tech. in computer-aided design and computer-aided manufacturing and is enthusiastic about 3D printing, product development, material science, and sustainability. He also has a deep interest in "Frugal Designs" to improve the present technical systems.