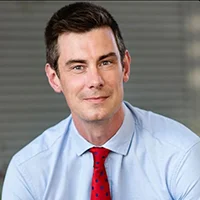
Calum Stewart, a leading figure at SPEE3D, has been at the forefront of integrating advanced manufacturing technologies into military operations worldwide. With a focus on deployable additive manufacturing, Stewart and his team have revolutionized how militaries produce essential components, enhancing logistics and operational efficiency in the most challenging environments.
In this interview, Stewart shares his insights on the successes SPEE3D has achieved, the challenges they’ve overcome, and the future of additive manufacturing in the defense sector.
Can you share some of the key successes you’ve achieved in building AM capabilities for military clients during your tenure at SPEE3D?
It all started in 2019 in Darwin with the Australian Army. Over two years, it became the first and most in-depth program focused on deploying advanced manufacturing as a practical capability, beyond the novelty of 3D printers, in the harsh, remote bush environment where Defence operates. These trials led to the development of XSPEE3D and the Expeditionary Manufacturing Unit (EMU). Our technology gave the military the confidence to realise what a realistic, deployable advanced manufacturing capability looks like in a Defence environment. This was SPEE3D’s first success: establishing the infrastructure and securing client confidence in applying a trusted and proven advanced manufacturing capability within military operations.
Because SPEE3D was able to establish this confidence in our clients, this resulted in a rapid adoption of that capability within militaries across the world such as the UK, US, Japan, and Ukraine, and now with a focus of expanding that within the Middle East and Africa. Militaries are more realizing the need to build up their own supply chains, and the possibility of being able to fabricate their own parts of consequence, in hours – not weeks – where they need them, to keep in the fight more of the time. Over the years of working closely with militaries, our biggest success has been truly understanding our customers’ environments and realizing the advanced manufacturing capability they needed. This achievement is unique to SPEE3D, as we now offer militaries a rugged, compact metal manufacturing capability that didn’t exist before. That’s the value we have successfully delivered to our customers.
What are some of the biggest challenges you’ve encountered while implementing additive manufacturing in military programmes, and how have you tackled them?
The biggest challenge has been convincing militaries to view our advanced manufacturing equipment as just another tool, which it is. Our EMU capability functions as a deployable foundry, something craftspeople can easily adapt to. The capability consists of just two containers, with no sensitive lasers, requiring only a generator to operate. One 20ft container houses the XSPEE3D for making metal parts, while the other contains the SPEE3Dcell to post-process them, complete with a furnace, CNC, and testing equipment.
Another thing is our defense-experienced team, many of whom are ex-military, has been key in helping our customers quickly overcome the stigma associated with additive manufacturing as being complex to operate and implement. Part of our success lies in providing military customers with intimate support and understanding when integrating this capability into their infrastructure. The capability is never just the printer; it includes training, applications requiring solutions, and more to equip militaries for success when using additive manufacturing in theatre.
How do you see the role of additive manufacturing evolving in the defence sector over the next five years, particularly in terms of strategic and operational benefits?
We know it is possible for militaries to deploy an additive manufacturing capability around the world to make metal parts and secure a more reliable inventory to keep kit in the fight. What’s needed now is for OEMs in the Defence industry to be more involved with additive manufacturing, and to incorporate it into their operations.
Involving OEMs has been a challenge. Militaries want them involved with advanced manufacturing technologies like ours. They want to see their OEMs using this technology to manufacture equipment and spare parts for their soldiers, and help them return to warfighter more quickly. The opportunity is there for them to better service their clients with the equipment they make and supply.
So, a strategic focus for SPEE3D in the next five years is to collaborate with OEMs. To understand their applications and material needs that will enable them to shorten their supply chain and increase their response and flexibility for their military clients. Why? Well, traditional manufacturing is not responsive enough to meet readiness requirements in theatre. Militaries have seen this for years. Digitized, deployable manufacturing is here, and OEMs need to take advantage of that for their clients, clients who already see the value in advanced manufacturing and are using this technology already.
What are some specific examples of how additive manufacturing has improved logistics and maintenance for military operations?
Additive manufacturing has been helping soldiers make thousands of parts all over the world, mainly plastic parts right now, but what is recent are metal parts of consequence. This is a capability SPEE3D has focused on with our military clients. Militaries don’t invest in a capability like this just to make plastic widget. Plastic widgets can be very useful for certain applications, but it’s the metal parts of consequence that allows Defence equipment to get back in the fight. Parts of consequence are the difference between having an application that fixes your broken engine platform in active theatre, to merely having some small bracket to hang your coffee cup in your car, for example.
The problem is militaries worldwide have sixty plus year-old land and naval platforms, platforms that are fraught with obsolescent parts, that need replacement metal parts from foundries that shut down twenty years ago. Casting is also heinously unreliable, takes months, and the part often results in cracks, or just fails. What a deployable additive manufacturing capability offers the Defence supply chain is reliability; and the ability to create metal parts of consequence needed in the moment. Our capability offers the confidence in knowing the standard of the metal part, material, weight, and size coming out of the printer each time is always the same. We know this because Defence has used our technology hundreds of times in field and dockside trials worldwide.
Digitised manufacturing results in militaries not having to overstock their inventory, and the ability to create one-off parts for decades-old equipment without abandoning the entire platform. With SPEE3D’s capability, personnel can manufacture large, sturdy metal parts in just minutes or hours—just enough for a soldier to achieve their mission, or lasting for years if post-processed. Deployable additive manufacturing enhances military logistics and maintenance by providing repeatable parts and enabling militaries to sustain platforms longer and more quickly. With more parts needed every day, less foundries globally, and increasingly complex supply chains, supplying Defence spare parts is something that current traditional manufacturing just cannot keep up with.
At AM Conclave, you’ll be discussing the future of AM in defence. What are the key points you hope to convey to attendees about the opportunities and potential hurdles in this field?
At AM Conclave we hope to convey that deployable manufacturing is a technology that exists and is possible, it’s something we offer, and is in use by militaries worldwide. We can offer the training and engineering doctrine for your personnel, and the support to make this capability a reality within your military infrastructure, or for you to better support the clients you serve.
The hurdle is understanding how you need to future-proof your current manufacturing capabilities, and spare parts supply chain. If you’re currently struggling to source spare metal parts made quickly, it’s time to consider this. Cold spray additive manufacturing offers a way to make large, cast-equivalent replacement metal parts that meet your standards, parts needed for deployed vehicles or naval ships to return to theatre.
About SPEE3D
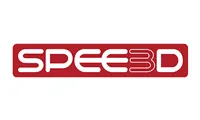
SPEE3D is an Australian-based company that has made significant strides in the field of metal 3D printing. Their technology is focused on providing a rapid and cost-effective solution for producing metal parts, challenging the traditional manufacturing processes.