Aircraft maintenance plays a critical role in today’s aviation industry, especially given the current challenges in global supply chains. As the demand for new aircraft increases, it is essential to keep existing aircraft in service as efficiently as possible. This is where 3D printing is making a significant impact by revolutionizing the production of spare parts. Companies like THE AVIATION AM CENTRE GmbH (AAMC) and EOS are using additive manufacturing technologies to improve the availability and cost-effectiveness of spare parts.
In this interview, Stephan Keil, Managing Director of AAMC, and Thomas Friedberger, Key Account Manager Aerospace & Defense at EOS, discuss the benefits and business case for 3D printing in the aviation industry. They explore how this technology not only drastically reduces production and logistics lead times, but also lowers costs and reduces physical inventory. They also explain which product categories are best suited for 3D printing and how it could become the primary approach for manufacturing spare parts.
What is the business case for this method to become the main method for spares manufacturing, and in what timeframe do you believe it will become prevalent?
The business case is driven by three core factors: producing spares at a lower cost than conventional, significantly reducing lead times for production and logistics, and a reduction of physical inventory in the long run.
Locally printed aircraft (cabin interior) spare parts can be produced 30-50 % cheaper than the cost of the OEM spare parts, with the added benefit that lead-times for production and logistics of usually 12 weeks (or significantly more) can be shortened to two weeks or even just a few days.
Another added value of industrial 3D printing technology is that the design of the parts can be improved to address known weaknesses or to enable part customization. As one of few OEMs, EOS provides high quality technology and materials to deliver parts into regulated industries such as aviation.
An incremental benefit of additive manufacturing is that it enables on-demand manufacturing of required parts in a mixed parts batch, which significantly reduces stock-keeping. Again, this will lead to cost reductions. Companies have two options – a) source parts from certified service providers (like AAMC) or b) build up their own MRO production hub. We see that the capability to offer in-house manufactured spare parts is a strong USP and customer retention tool for Aircraft Maintenance Service Providers. In this case EOS can offer a whole end-to-end solution to operate a production hub. And with the partnership with AAMC, we can offer the enablement to customers to comply with regulatory norms.
Industrial 3D printed spare parts are certified and “in-flight” as we speak, so the question is more when AM will fully scale to series production. Geopolitical crisis and supply chain resilience already drive this adoption faster than we anticipated.
What products do you foresee as leading candidates to be manufactured by 3D printing for spares?
Cabin interior parts are the primary candidates for on-site printing, as they are exposed to the highest wear and tear. Certification of this parts category mainly revolves around flammability testing, which our EOS material PA 22241 FR fulfills for the targeted part sizes that are suitable for printing on EOS systems such as the EOS P 396 or EOS P 770. We also see those parts from the flight deck and cargo areas, as well as electronic equipment bay are a perfect fit for our customer. Recently, we also saw that previous aluminium parts can now be additively manufactured using our EOS HT-23 material for applications in the fuel pump systems, etc., adding again to the weight reduction target of airlines.
About EOS
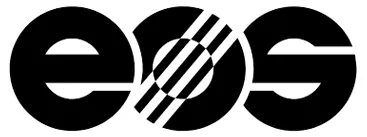
EOS provides responsible manufacturing solutions via industrial 3D printing technologies to organizations around the world. Since 1989, EOS has shaped the future of manufacturing by enabling its customers to innovate and differentiate through expert guidance, technology and services, leveraging its end-to-end additive manufacturing (AM) industry partnerships. From strategy to education to production, EOS is the leading global partner for both metal and polymer AM solutions, accelerating time-to-market for its customers through high-quality production efficiencies and sustainable solutions.