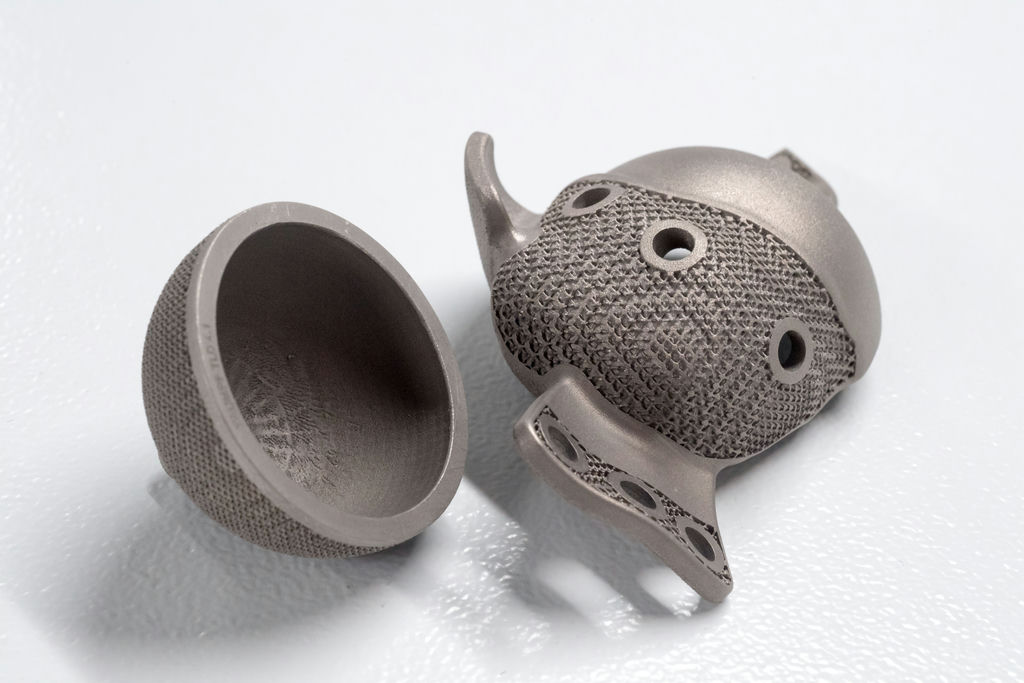
TRUMPF’s latest 3D printer processes significantly more materials than conventional systems. At the international Formnext trade fair in Frankfurt, the high-tech company demonstrated how the TruPrint 5000, preheated to 500 degrees Celsius, prints high-carbon steel or titanium alloy components that don’t crack or severely warp. “Tool and mold makers can now easily print forming tools, punches and dies. Previously, without preheating, that wasn’t possible,” says Tobias Baur, TRUMPF General Manager Additive Manufacturing with responsibility for technology. The company also has a new green laser with pulse function, enabling pure copper and precious metals to be processed in a 3D printer for the first time. “This makes it attractive for use in mechanical and plant engineering, as pure copper can be used to print particularly conductive inductors and heat exchangers,” Baur says. The green laser also holds great potential for gold printing in the jewelry industry, enabling individual unique pieces to be produced on demand while simultaneously saving expensive material.
Preheating to 500 degrees Celsius reduces temperature drop
In 3D printing, the devil often is in the detail: for instance, tool and mold makers frequently work with carbon tool steel 1.2343, an extremely hard and wear-resistant material that dissipates heat particularly well. To date, however, it couldn’t be processed in 3D printers because the components crack during printing. “The laser beam melts the component surface, which subsequently cools back down to room temperature. The components weren’t able to withstand this temperature drop, and cracks formed,” says Baur.
That’s why the substrate plate of the TruPrint 5000 3D printer can be preheated to 500 degrees Celsius. This lessens the temperature drop following laser melting. “The material quality and surface of carbon steels are significantly better than without preheating, preventing fractures in the components,” explains Baur.
Implants come out of the printer ready for use
Preheating also offers major advantages for prostheses and implants produced using additive manufacturing. “When the ambient temperature drops too sharply, the parts warp and we have to rework them. In addition, we often require support structures that are difficult to set up and take down,” says Baur. Preheating the TruPrint 5000 reduces stresses, improves processing quality and, in many cases, eliminates the need for support structures. It also often reduces the need for downstream heat treatment, as well as making the titanium more resilient and the implants more durable.
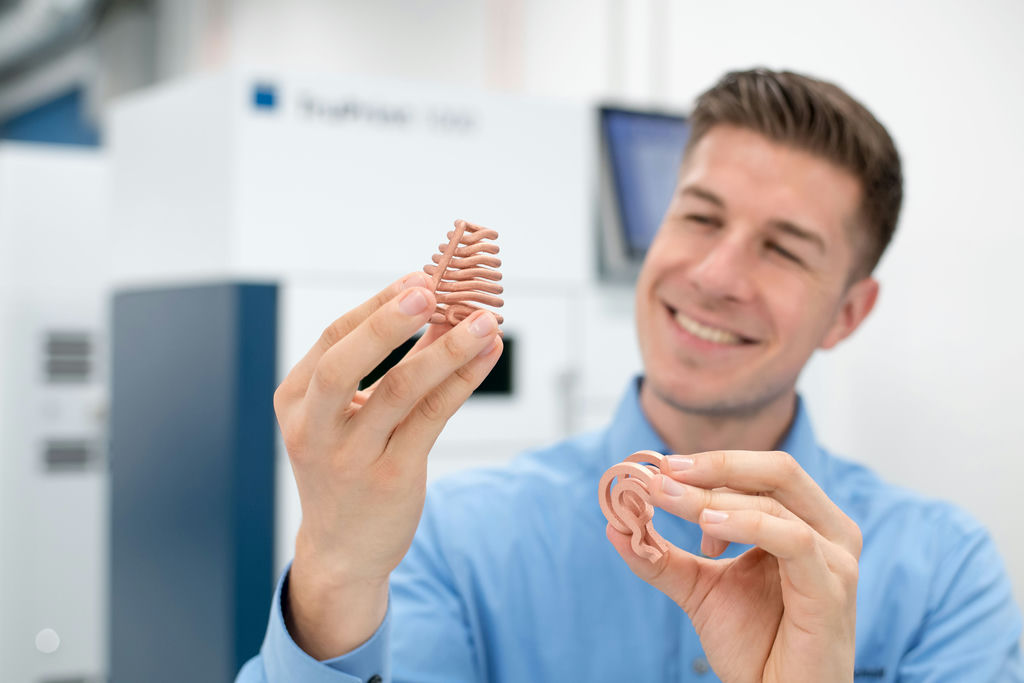
World premiere in copper printing
At Formnext, TRUMPF used a green laser with pulse function to demonstrate for the first time how to print pure copper and other precious metals. To achieve this, the developers connected the new TruDisk 1020 disk laser with the TruPrint 1000 3D printer. “Conventional systems use an infrared laser as the beam source, but its wavelength is too long and it can’t weld highly reflective materials such as copper and gold. This can be done with laser light in the green wavelength spectrum,” said Thomas Fehn, TRUMPF General Manager Additive Manufacturing with responsibility for sales. According to Fehn, this will open up new possibilities for 3D printing, for example in the electronics and automotive industries.
Customized jewelry with little loss of material
Using the green laser is especially lucrative in the jewelry industry, too. “The 3D printer doesn’t waste expensive gold and silver,” Fehn says. Printing is therefore often more economical than milling or casting a piece of jewelry, which inevitably entails a loss of material.
Trumpf is also printing their Industry 4.0 solutions into Additive Manufacturing. You can read it here