A group of researchers specializing in soft robotics at Fondazione Istituto Italiano di Tecnologia in Italy, collaborating with a colleague from the University of Montpellier in France, has devised an innovative robotic system that utilizes 3D printing to construct its own body, enabling it to extend in length. The team outlines the development process and potential applications of this unique robot in a paper published in the journal Science Robotics.
As advancements in science and technology progress, scientists explore inventive ways to integrate different innovations, giving rise to emerging forms of technology. In this recent endeavor, the research team merged the realms of robotics and 3D printing, resulting in the creation of a distinctive robot capable of intentional lengthening.
A snake-shaped robot, named FiloBot, employs additive manufacturing principles and mimics climbing plant behaviors to navigate through unstructured environments. The robot features a spinning head that utilizes 3D printing to generate additional body mass, causing the robot to elongate. Programmable growth options, such as moving towards light or defying gravity, enable the robot to adopt a vine-like growth pattern.
FiloBot incorporates a tube within its body that supplies a 3D printer ink, a type of plastic, to the rotating head. The head prints in a coiling manner, extending the robot’s body. The rear end of the robot contains a base housing the inkwell, a pump, and a power source.
The head of FiloBot includes electronics that respond to signals from external sensors, allowing the control of the printer’s output. This control mechanism regulates the spin rate and ink supply, providing direction to the growth process.
The researchers envision various applications for FiloBot, such as monitoring or interacting with natural environments, constructing autonomous structures, assessing avalanche or landslide risks, and conducting pollution level tests in challenging terrains.
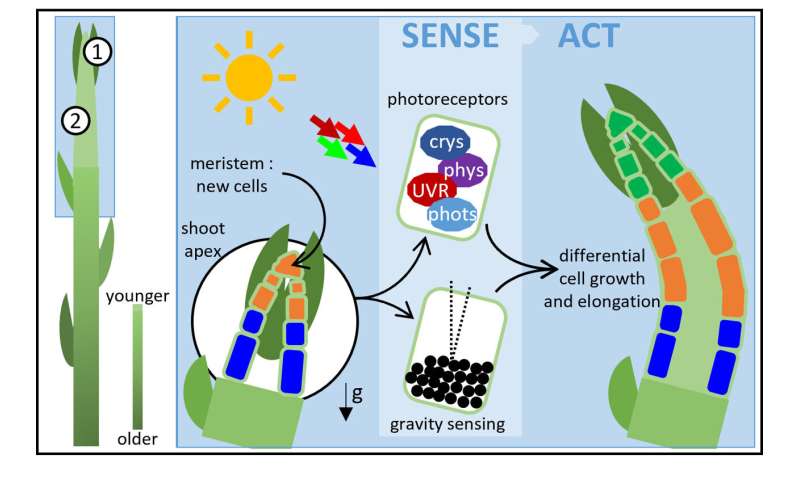
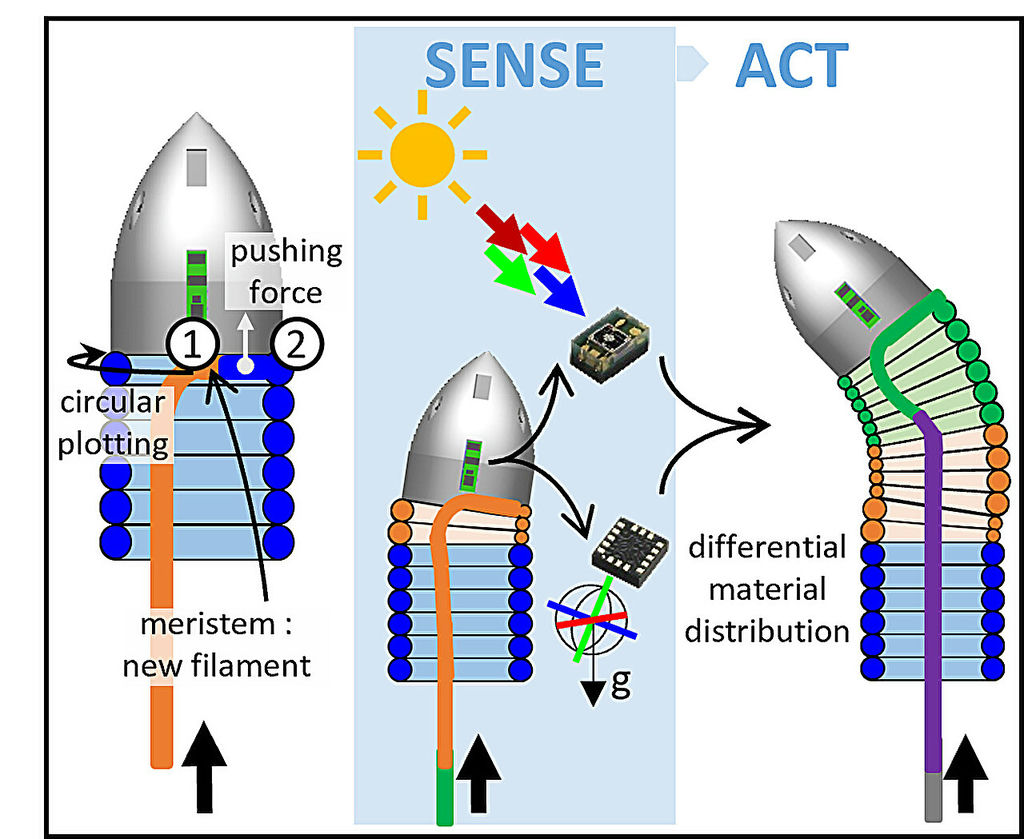
Subscribe to AM Chronicle Newsletter to stay connected: https://bit.ly/3fBZ1mP
Follow us on LinkedIn: https://bit.ly/3IjhrFq
Visit for more interesting content on additive manufacturing: https://amchronicle.com