ArcelorMittal SA, one of the world’s largest steel companies, has announced it is building an industrial-scale atomiser in Aviles, Spain, to produce steel powders for multiple Additive Manufacturing technologies. It was added that a new company, ArcelorMittal Powders, has been established to commercialise its metal powders, targeting users of Laser Beam Powder Bed Fusion (PBF-LB), Binder Jetting (BJT) and Directed Energy Deposition (DED) AM technologies.
The inert gas atomiser, which is expected to start production in January 2024, will have a batch-size production capability ranging from 200 kg to 3 tonnes, and an initial annual capacity of 1,000 tonnes. In line with ArcelorMittal’s commitment to sustainability and decarbonisation, the atomiser will produce powders from scrap steel, using renewable electricity, atomising with industrial gases produced by renewable energy, and using recycled and recyclable packaging solutions.
The steel powders will be offered in size ranges suitable for all existing powder-based metal AM technologies in manufacturing industries such as aerospace, defence, automotive, medical, and energy. They can also be used in the latest technological developments such as the brake disc coatings being developed to help automotive OEMs and Tier Ones comply with the EU7 regulation on particle emissions. A layer of powder deposited on the brake disc provides wear and corrosion resistance which significantly reduces the particulate emissions of braking.
“Additive Manufacturing is an area we have been investing in and building our capabilities for several years, and we are now ready to scale up our production and offer our customers and partners a reliable and competitive source of high-quality steel powders,” stated Colin Hautz, CEO of ArcelorMittal Powders. “From our facility in Spain, we will offer a range of steel powders tailored to our customers’ needs. A technology as innovative and disruptive as Additive Manufacturing not only allows us to think about changes in the design and manufacturing process of many parts and components we use today, but also exploit one of the inherently sustainable characteristics of steel – its recyclability.”
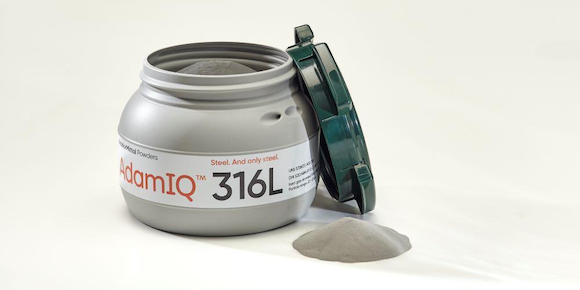
Marketed under the AdamIQ™ brand name, ArcelorMittal’s product portfolio will include stainless steels (316L, 430L, 17-4PH), tool steels (H11, H13, M300) and low alloy steels (a dual-phase alloy; 4140 equivalent). Drawing on its metallurgical experience, ArcelorMittal’s research and development team dedicated to AM technologies and steel powder production intends to add further steel powder products for customers to test in 2024.
The company is now looking to scale up its participation in the AM market and intends to scale its steel powders offering in collaboration with customers and industrial partners, through co-design and co-engineering projects.
ArcelorMittal has been producing steel powders in a pilot atomiser at its Additive Manufacturing lab in Aviles since 2018. With its dedicated research and development facilities and over 50 full-time researchers, ArcelorMittal has developed a detailed understanding of the interactions between steel alloy design, atomisation parameters, AM process parameters and the final properties of the printed parts.
ArcelorMittal has already collaborated with customers and partners on various projects, such as the development of a generative design steel motorbike chassis, the optimisation of AM productivity through software algorithms and, with a JV partner, the production of over 10 tonnes of 1,600 different spare parts per year, for its own steel plants.
Two factors helped ArcelorMittal decide that now is an appropriate time to enter the steel powders market. Firstly, the belief that Additive Manufacturing, while still at an embryonic phase, offers exciting growth potential, and there are significant benefits to gain from being an early participant able to foster the direction of growth. Secondly, feedback from industrial customers was that variations in batch-to-batch quality is a significant issue that is impacting production reliability and repeatability and is thereby impeding the broader uptake of AM in larger production runs. This, plus the trend to ever-larger AM machines prompted the decision to build an atomiser with a large batch size.
“We are proud to launch ArcelorMittal Powders, a new business unit that reflects our vision to be at the forefront of innovation and sustainability in the steel industry,” stated Gregory Ludkovsky, Chief Executive Officer of Global Research and Development, ArcelorMittal. “By producing and supplying steel powders for Additive Manufacturing, we are expanding our portfolio of advanced materials and solutions for the future of manufacturing. We believe that steel has great potential to become the material of choice for Additive Manufacturing, thanks to its versatility, performance and sustainability.
“The Additive Manufacturing industry has grown phenomenally over the past decade and is expected to continue to grow in double digits over the next ten years,” he continued. “While the production of steel powders is a new venture for ArcelorMittal, we are confident that our metallurgical expertise and solutions-based approach will provide our customers with the support they need to improve the quality and reliability of their Additive Manufacturing projects.”
Subscribe to AM Chronicle Newsletter to stay connected: https://bit.ly/3fBZ1mP
Follow us on LinkedIn: https://bit.ly/3IjhrFq
Visit for more interesting content on additive manufacturing: https://amchronicle.com