In recent years, advancements in 3D printing technology have been reshaping various industries, from aerospace to healthcare. One particularly transformative application has emerged in the field of orthopedics – the 3D-printed immobilization devices. This innovative approach to immobilizing and supporting fractured limbs is changing the way we approach injury recovery.
The world of medicine and technology is witnessing a groundbreaking development with the emergence of 3D printed Orthotics. Traditionally, when a person suffers a leg fracture or injury, they are fitted with a heavy, uncomfortable plaster cast that often leads to inconvenience and discomfort during the healing process. However, 3D printing technology is changing the game, offering a more patient-friendly and efficient solution.
In this article, we will delve into the world of 3D-printed orthotics, exploring their benefits, applications, taking example of a recent case done by Falcon Technologies International along with RAK Hospital.
The Traditional Leg Cast
For decades, the conventional plaster cast has been the go-to solution for immobilizing and supporting fractured and injured limbs. While effective in its purpose, plaster casts have several drawbacks. They are heavy, uncomfortable, and often cause skin irritation. Furthermore, their application is a time-consuming process, requiring skilled technicians and multiple layers of casting material.
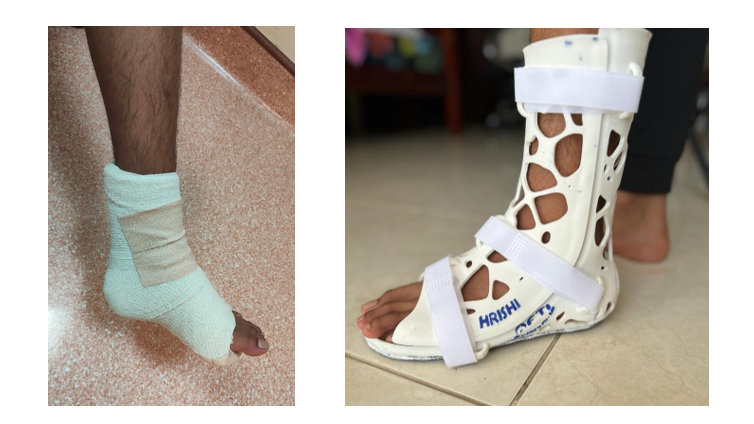
The Emergence of 3D-Printed Orthotics
3D printing, also known as additive manufacturing, has opened up new possibilities for customizing medical devices. With the ability to create intricate, patient-specific designs, 3D printing has revolutionized the field of orthopedics.
Benefits of 3D-Printed Leg Casts
Customization: Perhaps the most significant advantage of 3D-printed leg casts is their ability to be tailored to each patient. Through quick surface scanning of a patient’s limb using Structured light scanner, the 3D Image of the patient limb is available, and a cast can be precisely designed to match the contours of the patient’s limb. This level of customization ensures a snug and comfortable fit, reducing pressure points and enhancing overall comfort.
Lightweight and Breathable: Unlike traditional plaster casts, 3D-printed casts are considerably lighter and allow for better ventilation. This results in improved patient comfort and a reduced risk of skin irritation.

Hygiene and Maintenance: 3D-printed casts are waterproof, allowing patients to shower and swim without compromising the integrity of the cast. This significantly improves hygiene during the recovery period. Additionally, these casts are less likely to develop cracks or deteriorate over time, reducing the need for frequent replacements.
Improved Healing: The precision of 3D-printed casts ensures that the injured limb is immobilized effectively, promoting proper alignment and faster healing. The reduced weight also means less strain on the patient’s body during the recovery process.
Removable and Reusable: The 3D printed cast can be removed very easily and worn back. This will help the doctors to examine the patient incase of any issues and can be worn back every easily.
Process of Making a 3D Printed Leg Cast
Biocompatible material: The 3D printed cast is made of Bio compatible, PA 12 polymer.
Made in FTI Ras Al Khaimah – The only 3D printing facility in the region which is ISO 13485 Certified and GMP Certified by MOH for Medical devices manufacturing.
Patient Experience and Rehabilitation
The patient experience is a crucial aspect of healthcare, and 3D printed leg casts significantly enhance it. Patients report feeling more comfortable, less restricted, and generally happier with 3D printed casts compared to their traditional counterparts. This improved comfort often results in better compliance with treatment plans, leading to faster and more successful recoveries. The designs can be very trendy and improves the metal state of the patient while wearing the cast. Moreover, the lightweight and breathable nature of 3D printed casts allows patients to engage in certain physical activities and exercises, promoting better muscle tone and overall rehabilitation.
Challenges and Future Prospects
While 3D printed leg casts offer numerous advantages, they are not without challenges. Some patients may still require traditional casts due to the severity of their injuries. The cost of 3D printed casts can be higher. The hospital staff needs to be trained to capture the body contour scan. There could be an additional visit required to hospital to don the 3D printed orthotics. Since it is a customized product, from the body contour scan to manufacture, it could take 24 hours. Insurance approval is another area which needs to be addressed. However, as the technology advances and becomes more widely adopted, these challenges are expected to diminish.
Conclusion
The advent of 3D-printed orthotics represents a significant leap forward in the field of orthopedics. By combining precision, customization, and comfort, these casts are poised to revolutionize the way we approach limb immobilization and support during the recovery process. As technology continues to evolve, we can anticipate even greater strides in patient-specific care, ultimately leading to faster, more comfortable recoveries for those with orthopedic injuries.
Subscribe to AM Chronicle Newsletter to stay connected: https://bit.ly/3fBZ1mP
Follow us on LinkedIn: https://bit.ly/3IjhrFq
Visit for more interesting content on additive manufacturing: https://amchronicle.com