3D printing with most processes and materials generally comes with tradeoffs in terms of speed and quality, and this is especially true when printing with FFF (fused filament fabrication) systems.
If you want to print with the highest quality on an FFF printer, then you need to print with smaller layers, and thinner extrusion roads (smaller nozzle diameters) to get the most intricate details on the parts. Naturally, such increases in quality come at the expense of build time- it takes a lot longer to print parts with higher detail. This tradeoff in particular is a bottleneck for manufacturers employing this type of printing, and the problem becomes more exacerbated when wanting to print bigger parts.
Currently, if wanting to deposit large amount of material in the shortest time possible, the only real options are to increase the nozzle size, and increase the layer height. Naturally, this results in highly stepped surfaces. This may be acceptable for functional parts where aesthetics are of no concern, but for parts that need to be attractive, these stepped artifacts can be a pain to remove with post-processing.
However, researchers at Rutgers University in New Jersey have come up with a process called Multiplexed Fused Filament Fabrication (MF3), that allows for the high resolution deposition thermoplastic filament while maintaining fast deposition rates.
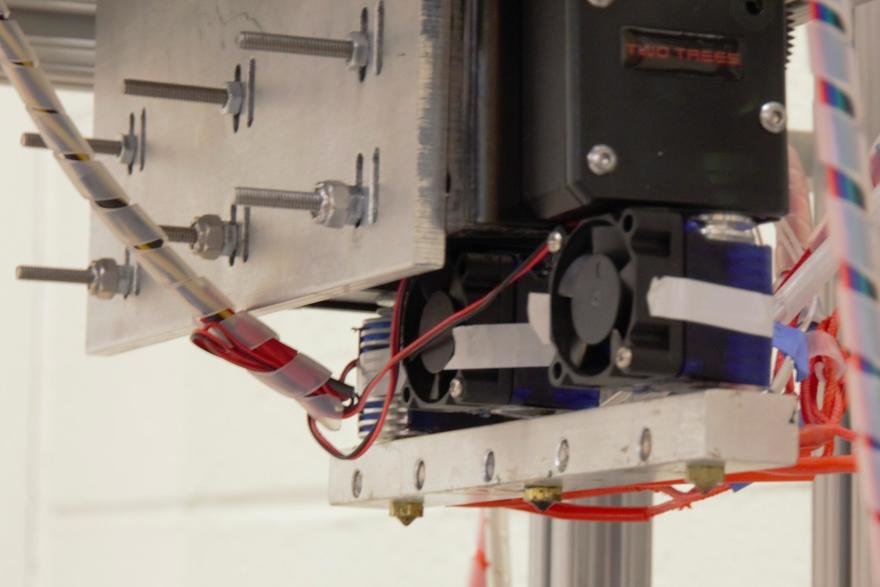
(Source: Rutgers University)
The secret? Mutliple print heads, all working together in parallel. In this system, there were three off-the-shelf extruders mounted to a single gantry, without independent motion, and with a fixed bed. So clearly, the three extruders must all follow the same motion.
The difference is that each extruder switches on and off independently, according to the toolpaths defined by the custom slicer software.
So for example, while all three extruders may be following the same motion path, the first extruder could be activated for printing the certain features on its own square toolpath, the second extruder could extrude other parts along that path, and the third extuder could print other features.
You can see this demonstrated in the photograph below.
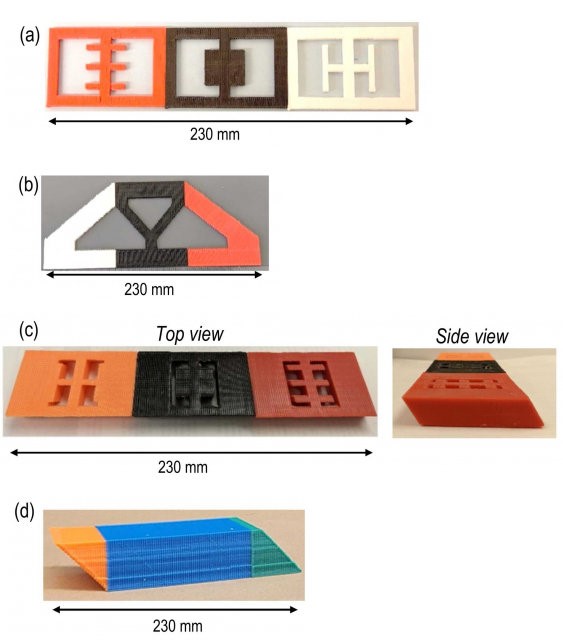
(Source: Rutgers University)
While the concept of printing in parallel has been demonstrated with a variety of approaches, they all have limitations of some kind.
For example, IDEX systems also use dual extruders mounted to the same gantry, but as they use typical FFF toolpaths, IDEX systems are only capable of printing periodic geometries on separate parts – that is to say, they can only print duplicates based on a common toolpath. They cannot print multiple sections of the same part, with differing (non-periodic) geometries.

(Source: Rutgers University)
So overall, the MF3 process has three unique capabilities. The first, as we have seen, is the ability to print non-periodic sections with more than two extruders, without independent motion control. either as individual parts or as sections of the same part, in different resolutions, and even different materials.
The second feature is the ability to simultaneously print multiple sections of the same part, with non-periodic geometries (or print separate and distinct parts of differing geometry and resolution). And the third unique feature is the ability to tolerate extruder failure without stopping production.
All of these features combined help to break the tradeoff of speed versus quality, increasing the throughput of the printer in question. And according to the researchers, their experiments using PLA have shown that resolutions Note that our choice of nozzle sizes means that the resolutions 2.5–4 times greater than that of BAAM (big area additive manufacturing) are possible using the MF3 method, and the throughput of BAAM systems can be exceeded simpy by adding more extruders to the array. And because the MF3 system can be manufactured with basic, off-the-shelf extruders, it is now possible to build a high quality, high throughput FFF printer, equal to BAAM in terms of extrusion rates, but orders of magnitude cheaper than commercially available BAAM systems.
For more information, the research can be found here.
Subscribe to AM Chronicle Newsletter to stay connected: https://bit.ly/3fBZ1mP
Follow us on LinkedIn: https://bit.ly/3IjhrFq
Visit for more interesting content on additive manufacturing: https://amchronicle.com
Company Press Release