Metal Atomizers are advanced technological solutions used to manufacture metal powders, and the interest in these systems is increasing. They utilize high-pressure gas or centrifugal forces to break down molten metal into fine droplets or powder to create necessary powders for various applications. In the case of various metal additive manufacturing methods, metal powders play a significant role as high-quality metal powders directly impact the quality of the end product.
This article explores the basics of Metal atomizers and highlights the challenges faced by research and development labs with powders and the role of ATO metal atomizing systems in solving their various challenges.
Metal Atomizers
Metal Atomizers use techniques to break molten metal into fine droplets or powder. The working principle of these systems can vary depending on the specific technology employed. Metal Atomizers find applications across a wide array of industries.
ATO metal atomizing systems utilize the power of ultrasonic vibrations to break down molten metal into small droplets, which rapidly solidify into metal powder within an inert gas-protective atmosphere. The frequency of the ultrasonic vibrations influences the size of the metal powder particles. Higher frequencies result in smaller particles, while lower frequencies produce larger particles. Other factors that affect particle size and distribution include viscosity, density, ultrasonic amplitude, and the design of the atomizer itself. Ultrasonic atomization using ATO technology begins with introducing the raw material into a pressurized atomization chamber. An electric arc is generated within the chamber to melt the material, forming a molten metal bath. Ultrasonic vibrations are transmitted through a sonotrode, a component that contacts the molten metal bath. This technology ensures that ATO’s systems can be used in various industries.
Metal Atomizing in Metal Additive Manufacturing
Metal atomizers play a pivotal role in metal additive manufacturing. By transforming molten metal into fine powder particles, these systems enable the creation of intricate and complex geometries with high precision.
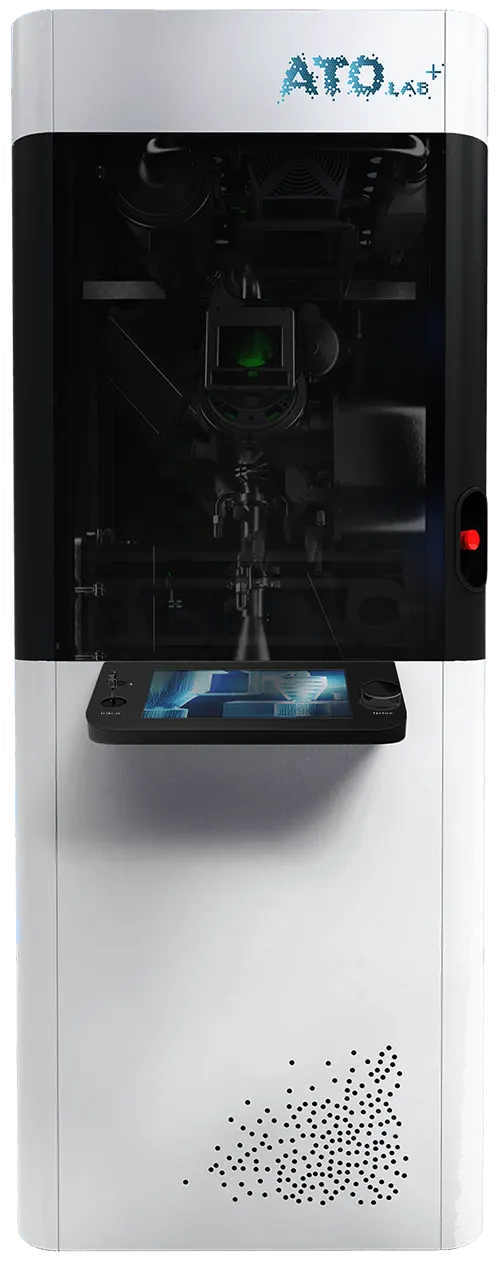
The metal powders are used in various metal additive manufacturing methods such as direct energy deposition, powder bed fusion, binder jetting, and sheet lamination.
Several atomization techniques are employed to produce metal powders with varying properties. Gas atomization involves spraying molten metal through a nozzle with high-pressure gas, resulting in highly spherical powders with narrow particle size distribution. Plasma atomization employs a high-energy plasma torch to melt and atomize metal feedstock, allowing for excellent control over particle size distribution and the production of both spherical and non-spherical powders. The choice of atomization technique depends on the desired powder properties, cost considerations, and specific application requirements, allowing for the continuous advancement of manufacturing capabilities in various industries.
Advantages of ATO atomizer over traditional systems for R&D Labs
In the metal atomization process, metal powders of varying sizes are produced, which are used for various metal additive manufacturing and powder metallurgy applications. The ATO atomizer can achieve a narrow particle size distribution ranging from 20 to 120 μm, which can be used for specific Research and development purposes.
The average order size for metal powders ranges from 100-150 kgs when procured from any metal powder supplier. The large average order size is a significant constraint for most research and development labs. With the ATO atomizer, the research and development labs can manufacture powders in limited quantities, reducing costs.
The other challenges that research and development labs face are the availability of a limited number of materials. The ATO atomizer system offers remarkable capabilities for producing metal powders. This advanced technology allows for producing metal powders from various materials, including refractory and high entropy metals, with melting temperatures of up to 3400°C. This expanded material compatibility opens up a broader range of research and development applications.
The ATO atomizer system can also be used for large-scale research and development projects, as powders can be manufactured in small and large batches. In addition, its lab fit design also solves the availability-related challenges faced by the labs.
One standout feature of the ATO atomizer is its ability to achieve a narrow particle size distribution. This is achieved through the influence of ultrasonic waves, which can be adjusted by manipulating the ultrasonic frequency and other parameters. This level of control allows the atomizer to generate metal powders of different sizes and shapes to meet specific application requirements, making it an incredibly customizable system. These powders exhibit extremely low oxygen content, ensuring their suitability for reactive alloys. The powders also boast high particle sphericity and excellent flowability, making them ideal for reactive and non-reactive alloys. The innovative sonotrode used in the system eliminates contamination and guarantees a stable and repeatable atomization process.
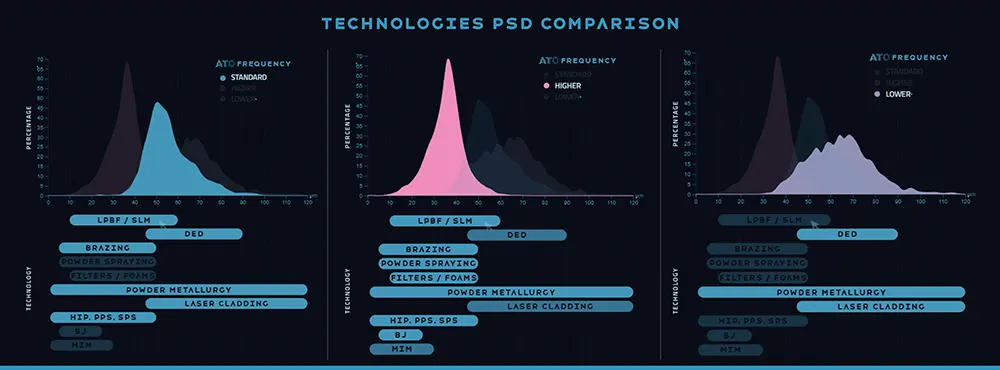
The ATO metal atomizer system’s key features include its lab-fit size, which overcomes compact workplace requirements. Post-installation, the system can produce low oxygen content, high particle sphericity, and excellent flowability for day one. Additionally, ATO processes a range of reactive & non-reactive alloys (steel, aluminum, titanium, nickel-based, and many more), making it ideal for commercial & research needs. The systems also ensure reduced costs and quickly optimize processes with custom powders at a reasonable cost.
Conclusion
Metal atomizers have revolutionized metal manufacturing by providing a versatile and efficient method for producing high-quality metal powders. The emergence of cutting-edge systems like the ATO atomizer further pushes the boundaries of achievable goals, empowering industry professionals to innovate and transform how metals are used in manufacturing. With the continuous advancements in metal atomization technology, we can expect further breakthroughs in material science and engineering, opening up new possibilities for metal-based products in the future.
About Shree Rapid Technologies (SRT)
Shree Rapid Technologies (SRT)Â is a pioneer in 3D Printing Technology and incorporated in 2007. They are specialized in cutting-edge technology into 3D Printing, 3D Scanning and Measurement that enables us to design, validate and create precise and intricate 3D prototypes and end use parts. They cater to variety of applications in multiple industries line Aerospace, Automotives, Bio Printing, Dental, Jewellery, Machine Tooling, Medical Devices, Service Bureaus, etc.
Their state-of-the-art Customer Innovation Center (CIC) is laced with advanced 3D Printers, 3D Scanners, Metrology and Inspection.
To visit the experience center or any other query kindly mail at :Â [email protected]
Contact Number: (+91) 7208843624 / 022-67415403
To Know more visit:Â https://www.shreerapid.com/
Subscribe to AM Chronicle Newsletter to stay connected:Â Â https://bit.ly/3fBZ1mPÂ
Follow us on LinkedIn:Â https://bit.ly/3IjhrFqÂ
Visit for more interesting content on additive manufacturing:Â https://amchronicle.com