Researchers from Concordia University, Montreal, are exploring the 3D printing of graphene oxide liquid crystals to enable materials with previously-unseen levels of strength.
More from the News
Having made headlines for over a decade, graphene is one of those wonder materials that promised to solve a number of our engineering challenges. The sheet-form carbon allotrope comprises a single layer of atoms arranged in a 2D nanostructure resembling a honeycomb lattice. The material is known for its high strength-to-weight ratio, excellent thermal and electrical conductivity, corrosion resistance, and scratch-resistant qualities.
Unfortunately, we haven’t yet been able to translate graphene’s strength from the microscale to real-world applications in the macroscale.
The Concordia team is now using photocuring, the technology behind stereolithography 3D printing, to produce self-assembled graphene oxide structures that are both larger and more complex than today’s possibilities.
Graphene – the strongest known material
Andre Geim and Konstantin Novoselov discovered graphene in 2004, winning the Nobel Prize in Physics for their work shortly after in 2010. At just an atom thick, graphene is around a million times thinner than a human hair but offers a Young’s modulus of 1TPa and a tensile strength of 130GPa. This makes it the strongest known material so far.
Although scaling graphene up is still a huge challenge, the self-assembly of graphene oxide sheets into liquid crystals is a promising approach to jumping the hurdle, as these liquid crystals could potentially be transformed into solid macroscopic structures.
Thus far, the self-assembly process has led to a whole host of macroscopic (albeit thin) structures such as paper, fibers, and aerogels. There are a number of methods for producing these structures, including wet-spinning, freeze-drying, and vacuum filtration. While these approaches do work to preserve the ordered structure in the liquid crystal phase, they’re limited in the thickness and complexity of the structures produced.
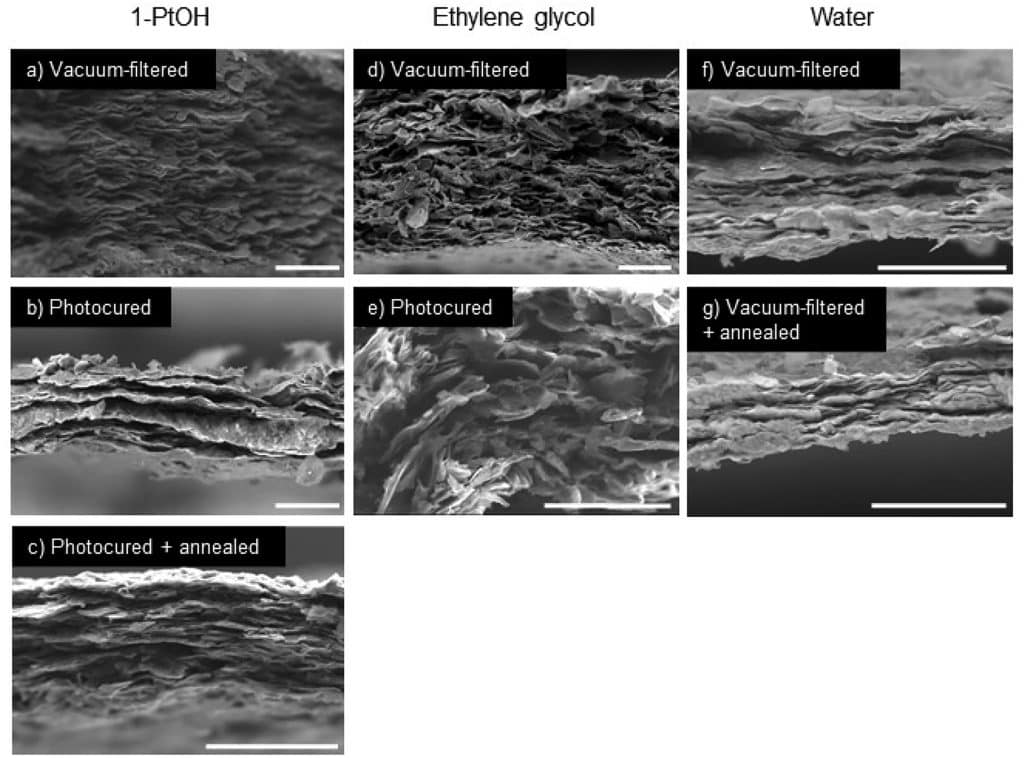
The photocuring approach
The Concordia team turned to photocuring as an alternative. To prepare graphene oxide sheets, they first dispersed graphene in alcohol and mixed in a commercially-available photoinitiator called bis(4-methylphenyl) iodonium hexafluorophosphate. This is the same photoinitiator used in many of today’s 3D printing resins.
The researchers found that they could successfully cure the resulting mixture into thin sheets of graphene oxide, turning it from a liquid state to a solid state using UV light. As such, the method is now thought to be compatible with 3D printing technology.
The novel photocured graphene oxide paper also impressed in a series of tensile tests, exhibiting mechanical properties comparable to those of a benchmark graphene oxide paper, which was prepared via conventional vacuum filtering.
The study writes, “We demonstrate that it is possible to photocure graphene oxide liquid crystals. Photocuring graphene oxide liquid crystals allows for thicker and perhaps more complicated structures than what is possible with current methods such as vacuum filtering or wet spinning.”
Moving forward, the Concordia team would like to adapt the approach to full-scale stereolithography 3D printing in the hopes of fabricating large 3D structures made of graphene.
Further details of the study can be found in the paper titled ‘Photocuring Graphene Oxide Liquid Crystals for High-Strength Structural Materials’.
The additive manufacturing of graphene-based materials has certainly been explored before. Researchers from China’s Harbin Institute of Technology recently 3D printed a soft graphene oxide robot capable of moving backward and forwards when exposed to moisture. The project involved using Direct Ink Writing (DIW) 3D printing and constrained drying techniques, which addressed manufacturing challenges related to porosity, shrinkage, and structure uniformity.
Elsewhere, researchers from Carnegie Mellon University (CMU) and the University of Connecticut (UConn) 3D printed novel calcium phosphate graphene (CaPG) scaffolds that could one day be used for bone regeneration applications. The bioprinted structures offer several desirable properties such as osteoinductivity, biological safety, a long shelf-life, and reasonable production costs.
Subscribe to AM Chronicle Newsletter to stay connected: https://bit.ly/3fBZ1mP
Follow us on LinkedIn: https://bit.ly/3IjhrFq
Visit for more interesting content on additive manufacturing: https://amchronicle.com/