Tomsk State University and the Institute of Strength Physics and Materials Science (ISPMS) have proposed a new method of 3D printing, which uses materials previously inaccessible for this: metals, metal ceramics, and even high-energy materials.
Unfortunately, there are some material limitations in modern 3D printing methods. Some materials, for example, consisting of metal and ceramics, from refractory and low-melting metals, cannot be used with existing methods, – explains Marat Lerner, Doctor of Technical Sciences, the project manager and head of the laboratory at ISPMS. – My colleagues from TSU and I propose a slightly different way of additively forming parts of complex shapes, which will help us to bypass this limitation. In the method that we are developing, there are no restrictions on the phase composition of materials.
The scientists’ technology will make it possible to use metal, cermet, and high-energy materials for printing complex-profile structures. In the course of the project, scientists will create their prototype of an installation for 3D printing with nanomaterials (nanopowders). The powders for printing are obtained in the laboratories of TSU and ISPMS.
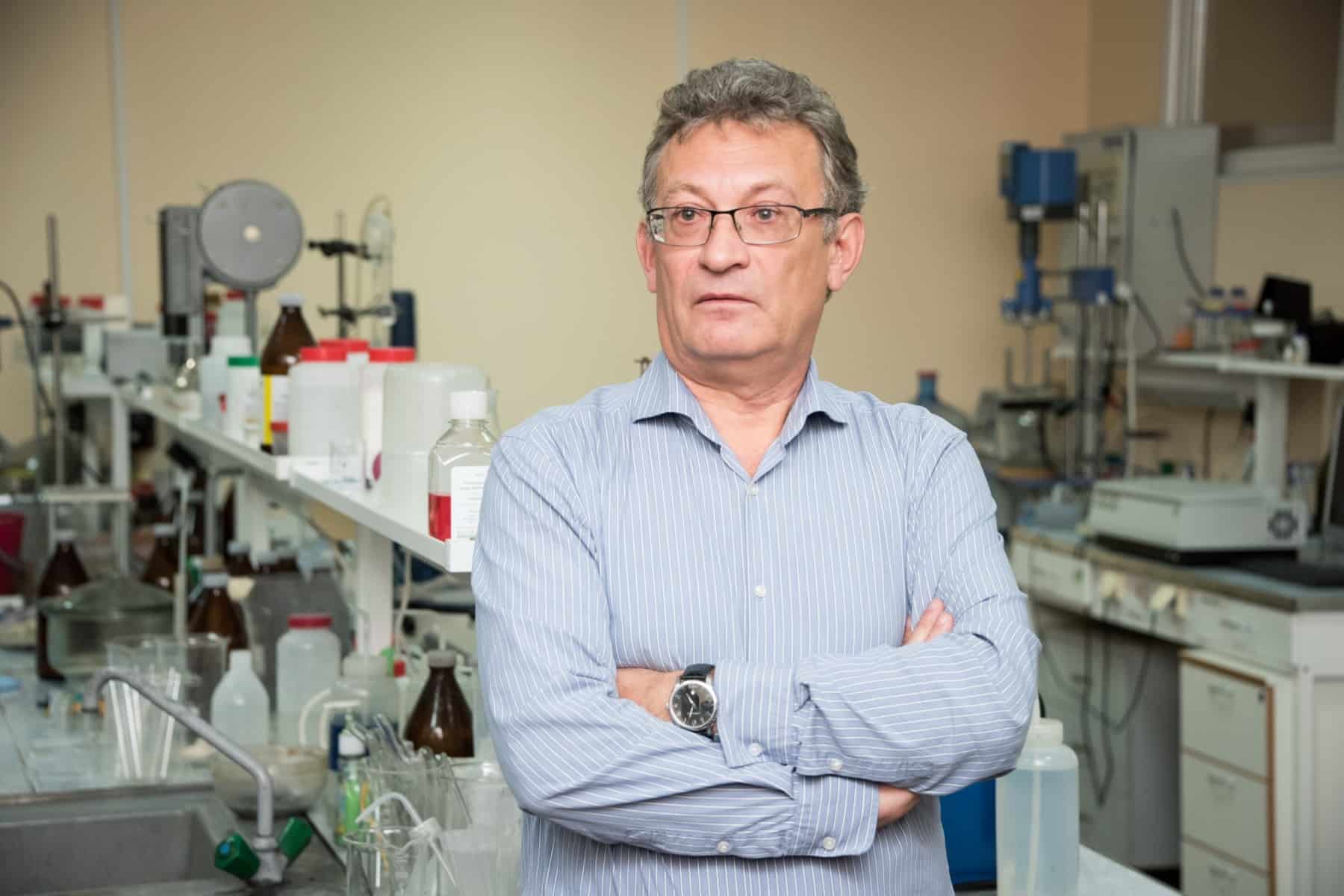
In fact, it will be possible to design a material to give it the required mechanical, magnetic, electrical, energy, and other properties that are difficult or impossible to achieve with the help of single-phase metals or ceramics,- say the authors of the project. – Various combinations of initial nano- and micro-sized components make it possible to vary the properties of the compositions to create new structural and functional materials and parts from them.
Products made from such materials are in demand in power and microelectronics, aerospace, manufacturing, in the manufacture of complex fuel cells, and others.
Also, the combination of high-energy materials and additive technologies has great potential in the production of energy conversion and storage devices that were previously unavailable due to the limitations of traditional manufacturing methods. Also, the versatility of additive molding will provide greater flexibility in the development of fuel and pyrotechnic compositions.
The project is designed for three years and as a result, scientists will present a cheap and affordable method for the majority of consumers for the additive creation of parts of complex shapes.
More on this project, right here!