Material Extrusion is seeing an upsurge in new applications with diverse materials being used including carbon fibre, metal, ceramics, glass and many more and for this tried and tested technology it is a second coming of sorts.
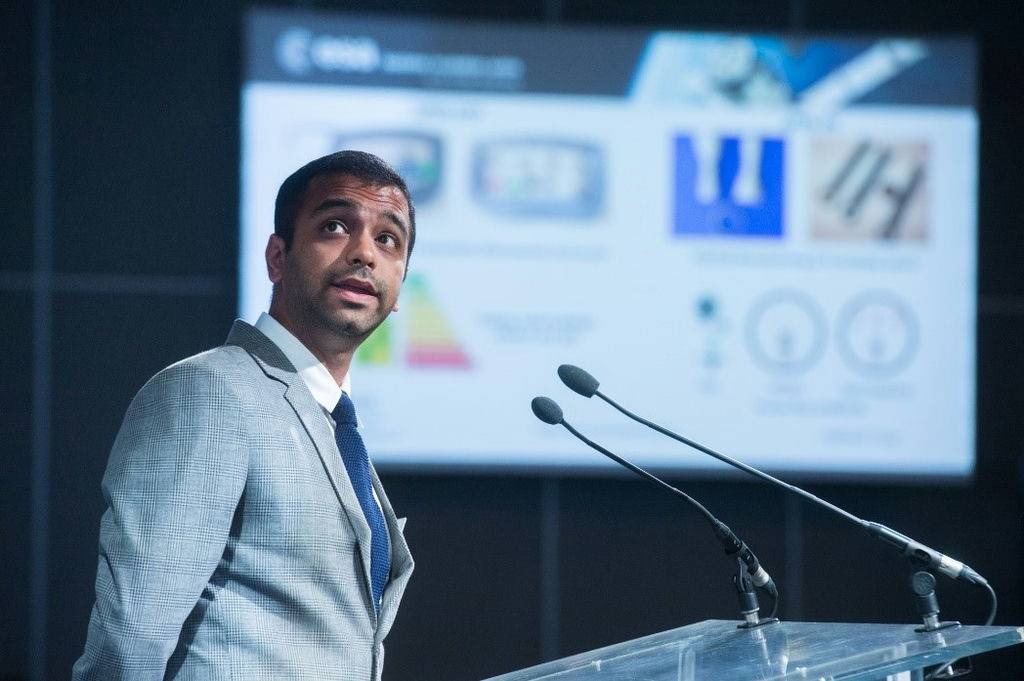
As a part of this series to explore the depth of utilising Material extrusion, Aditya Chandavarkar, Co-Founder of AM Chronicle caught up with Siddharth Tiwari, Founder and Managing Director of ESA-supported Startup TIWARI Scientific Instruments, Germany. Since March 2019, TIWARI Scientific Instruments is hosted at ESA Business Incubation Centre (ESA BIC) Hessen & Baden-Württemberg at its Darmstadt location. Siddharth is a Masters (MSc.) in Space Engineering from Polytechnic of Milan, Italy, and Bachelor of Technology (BTech) from VJTI, Mumbai, India. He has worked on numerous international projects including NASA’s Insight mission to Mars (Launched in 2018 from Vandenberg, USA, and Lander currently on the surface of Mars), Vacuum furnace for CERN in Geneva, and several other R&D Projects contracted via the European Space Agency as well as European Union.
Aditya Chandavarkar Before we dive into the specifics, we would be keen to know how the journey has been at Tiwari Scientific for you and what have been the primary drivers for venturing into utilising Additive Manufacturing for Space Applications.
Siddharth Tiwari: We were accepted into the ESA BIC Program in Germany in 2019 and this really gave us the boost to carry out development activities at a very high intensity. Besides the expectedly good tech support which have received from ESA and industry experts, it also gave us amazing visibility – allowing us to exhibit at Paris Le Bourget and at the startup night organised by the German ministry of Economy and Energy within the first few months after setting up shop. These events helped us to plant the idea of extrusion-based AM in the minds of partners and customers, and over the due course we have been able successfully collaborate with some of them to take the tech further. Space and AM is perfect match – small series of complex parts, varying from mission to mission, that need to be manufactured of high-performance materials. Besides this, the requirements for space are so high that after having a process qualified for space it becomes easily adoptable for terrestrial industries as well.
AC: Material Extrusion or FFF has been widely known and has seen success as a entry level technology for prototyping with polymers. However, this technology is having a second coming of sorts, with more advanced materials being used including composites, metals and ceramics. What are your thoughts on this ?Â
ST: Desktop 3D printers have become cheaper and cheaper in recent years and there’s been a lot of interest in mixing in materials with traditional print stock. This slightly-altered version of Material Extrusion print process uses thermoplastic filaments that are embedded with particles of the metal or ceramic the part is to be made from. Once the printing is finished, the part – known as a ‘green body’ – is put through a thermal treatment to eliminate the plastic, leaving behind a metal or ceramic item. Due to the improvement in not only the quality of filaments manufacturable but also optimisation and streamlining of individual process steps, the achievable maximum relative density of parts has gone from 90% to beyond 98%. This includes high-performance materials like Steel, Titanium, Copper, Silicon Carbide, Aluminium oxide, Tungsten Carbide etc.
AC: What role do you see Raptor playing in the manufacturing process along with other established technologies like powder bed fusion and binder jetting for advanced metal and ceramic materials.
ST: Each technology has its pros and cons and I think the choice for tech has to be made based on applications. Extrusion-based systems offer advantages in terms of material flexibility (both metals and ceramics can be processed), and if heat treatment is done in bulk the cost per part is low.
Material Extrusion based systems offer a performance-to-price ratio that can possibly not be matched by other manufacturing technologies. The more users we are able to convince, the cheaper the tech will get. In a way – as a colleague of mine always says – we are trying to democratise AM, making it available to all! With this mind we also launched our online tool to give users quick idea of the price of the parts.
AC: Can you share few examples of components designed using the Material Extrusion technology developed at Tiwari Scientific?
ST: You can see here few generic examples of parts we have printed using Material Extrusion
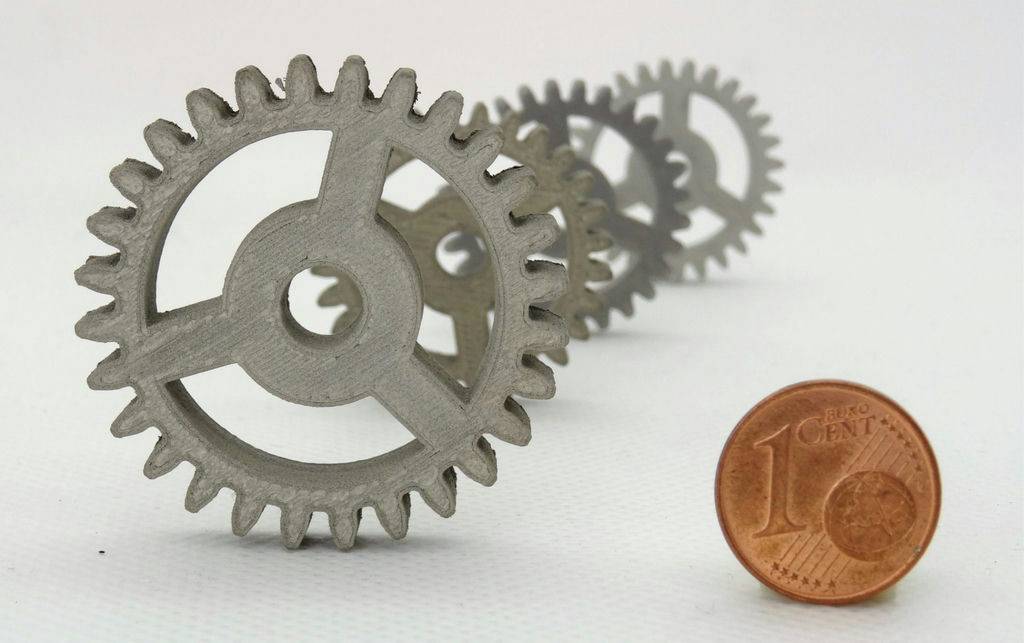
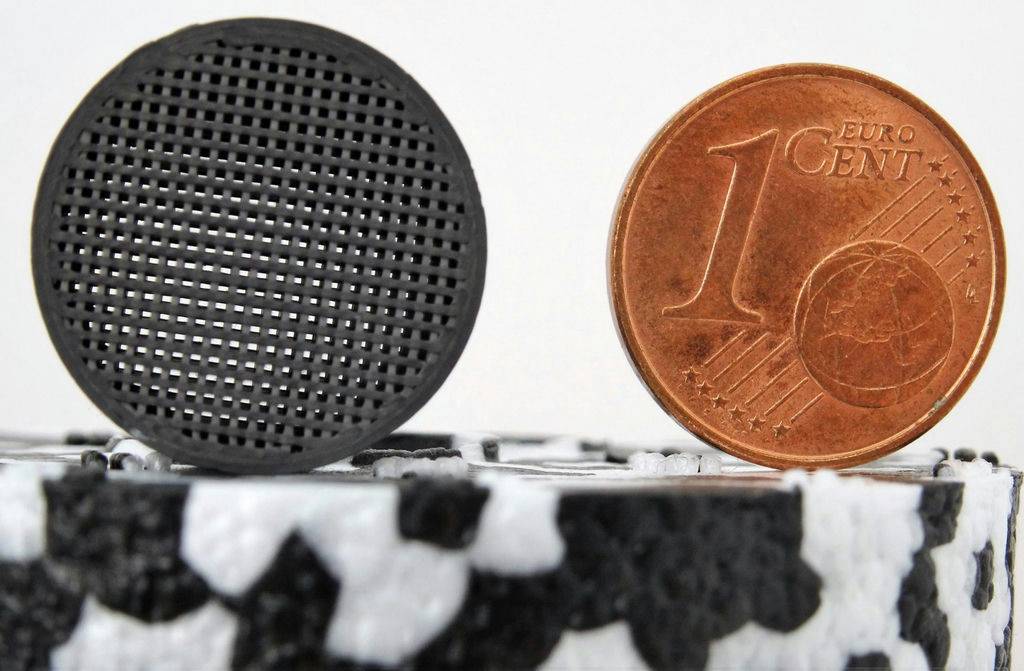
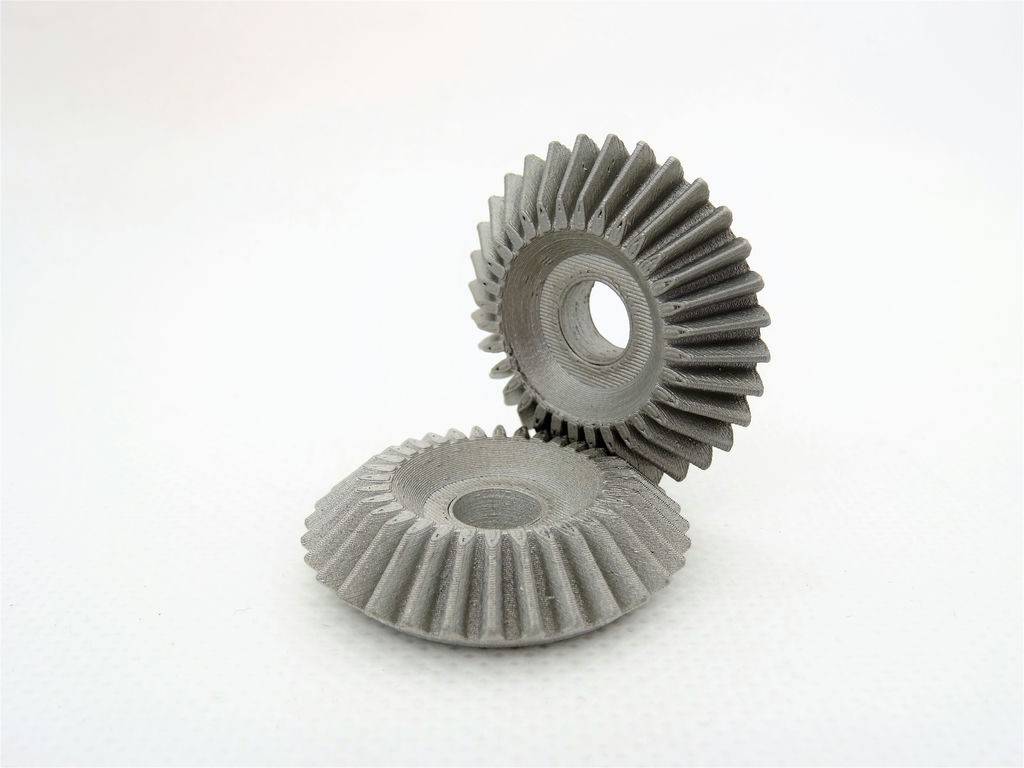
AC: How does the roadmap for Tiwari Scientific look like from here on?
ST: I would sum-up our roadmap in the following steps:
- Adopting and qualifying new materials
- Penetration into various market sectors through successful implementation of pilot projects
- Digitalisation of manufacturing
- Building up a reliable and scalable supply chain