In 2023, Lithoz GmbH, world market and technology leader in ceramic 3D printers and materials, announced its sales partnership agreement with Wendt (India) Ltd. This cooperation with WIL, as an internationally reputed partner in the field of super abrasive grinding wheels and machines, will strategically extend operations to the subcontinent’s fast growing 3D printing market and enable both companies to further expand and develop their business in India.
Wendt India Ltd.: Technology Leaders in Super Abrasive Products, Grinding & Honing Machines
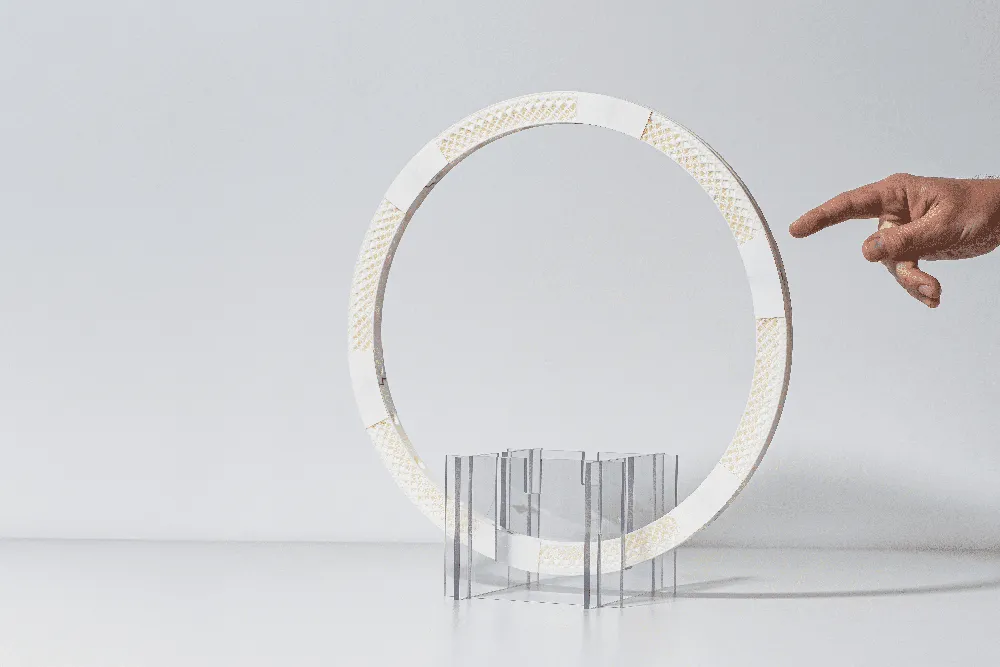
Wendt India manufactures CNC grinding, honing machines, super abrasive products and precision products using Wendt SA and machine facilities.
Wendt India Ltd. is known for its diversified and impressive product portfolio, innovation strategy, strong product development, personalized technical services and providing technology solutions in grinding to its 750+ direct customers in the domestic market. Wendt India believes in direct sales to its customers who are serviced through highly trained application-orientated sales engineers located in India and with well-versed supplier partners globally.
Transforming Semiconductor Production
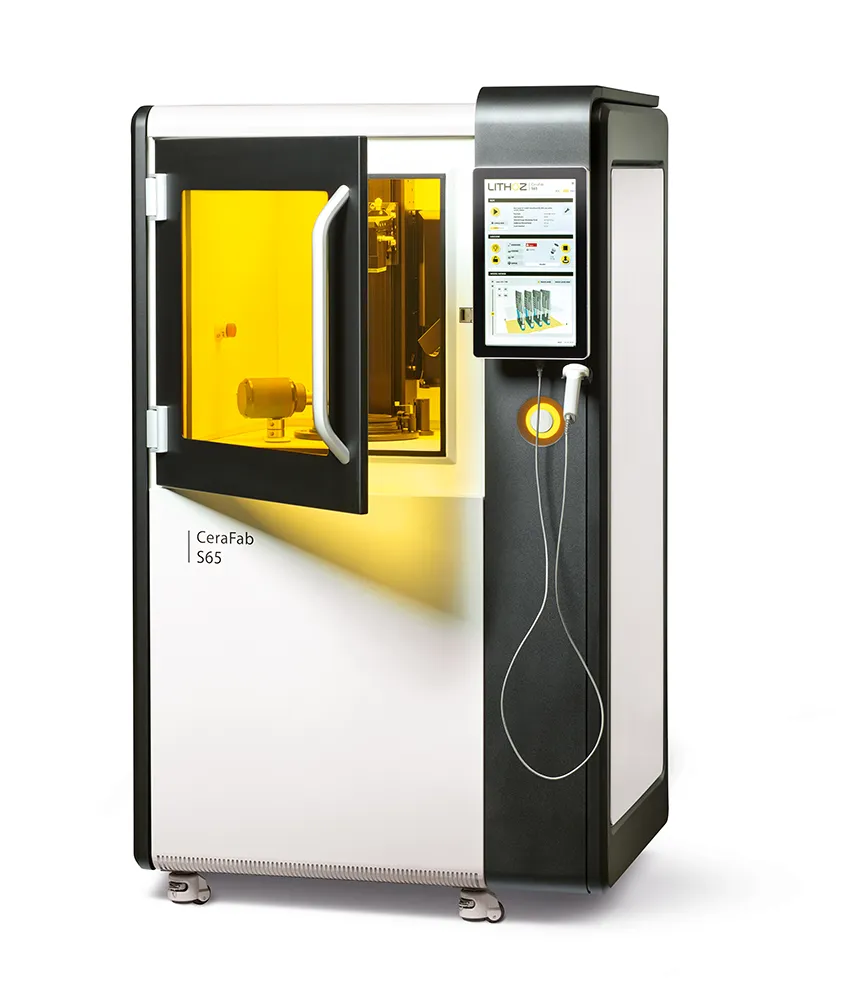
Ceramic materials are used where metals and polymers fail, particularly in semiconductor manufacturing, where harsh environments demand superior durability. Components in these industries face rapid wear from exposure to reactive gases and corrosive chemicals.
Lithoz’s LCM (Lithography-based Ceramic Manufacturing) 3D printing technology produces parts with the exceptional material properties of high-performance ceramics, such as exceptional chemical corrosion resistance, minimal surface roughness and outstanding thermal resistance. These qualities significantly extend the lifespan of critical components, reducing downtime and improving operational efficiency. A major part of the solution also lies within the smart design of those parts. By realizing parts with previously unachievable complexities through the design freedom offered by LCM technology, this next generation of critical spare parts significantly boosts production output.
Advancing Aerospace Engineering
The aerospace sector demands components capable of withstanding extreme environments—high temperatures, thermal shocks, and corrosive conditions. Even the toughest metals and alloys wear down quickly under these stresses.
Lithoz’s LCM technology empowers the production of high-performance ceramic parts from materials such as silicon nitride, aluminum nitride, and alumina. These parts offer exceptional strength, toughness, and resistance to thermal and chemical stresses, ensuring superior performance and longevity. The consolidation of multiple components into a single, integrated ceramic part also reduces weight, improves structural efficiency, and minimizes failure points.
This innovative approach enables the design of propulsion systems and other aerospace components that are lighter, more efficient, and more durable, meeting the sector’s relentless drive for higher performance.
Revolutionizing MedTech Applications with Bioceramics
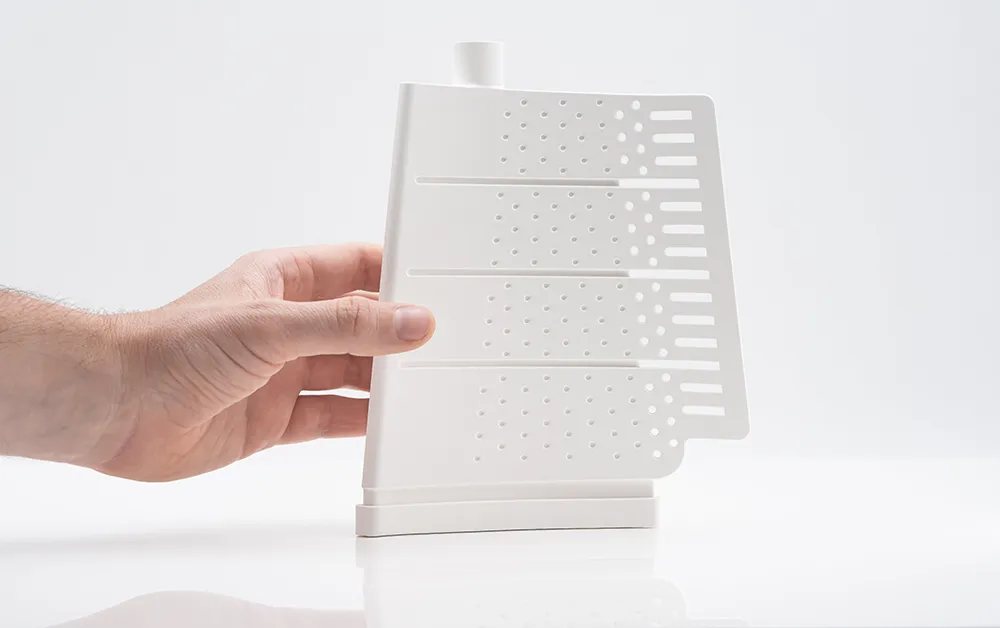
Ceramic materials, particularly calcium phosphates, have transformed medical applications due to their bioresorbable properties. Implants made from such ceramic materials are gradually replaced by natural bone, eliminating the need for secondary surgeries.
With Lithoz’s LCM technology, patient-specific implants can be produced with complex geometries that mimic natural bone structure. These implants promote efficient healing and regrowth while expanding possibilities for customized treatments. Bioceramic implants work seamlessly alongside metal components, offering enhanced recovery and outcomes for patients.
Visit Wendt and Lithoz at AM Tech
Explore the groundbreaking applications of ceramic 3D printing at AM Tech in Bangalore, December 11–12. Wendt India will showcase advanced ceramic components for semiconductor, aerospace, and medical applications using Lithoz’s LCM technology.
Visit Stall D7 to see how this partnership is driving innovation in ceramics and experience the future of manufacturing in person!
Company Press Release